- Joined
- May 1, 2023
- Messages
- 115
- Points
- 113
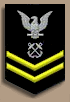
Hi, colleagues!
Over the past few days, I have been troubleshooting an issue with my CNC machine. Finally, I discovered the culprit - one of the power supplies was experiencing undervoltage. Unfortunately, this led to a spoiled future part of the ship model. However, it also provided me with a better understanding of the limitations of CNC processing when working with composite wooden materials.
The experience appeared to be so valuable to me that I have decided to share it with you.
So. I've decided to upgrade the front wall of the admirals' cabin. Scale 1:65. Instead of just using planks, I decided to create a layered structure using veneer at the bottom, walnut planks in the middle, and pear wood on top. The idea is that after CNC machining, the relief parts of the wall will remain made of pear wood, while the rest of the pear wood will be machined out, revealing the walnut planking.
The pie should be like this (the concept, not a real part):
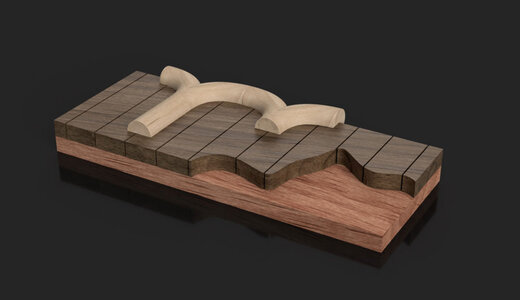
I designed a model in Fusion360. It took me some time
And even made a prototype - so far just form pearwood (no composite yet):
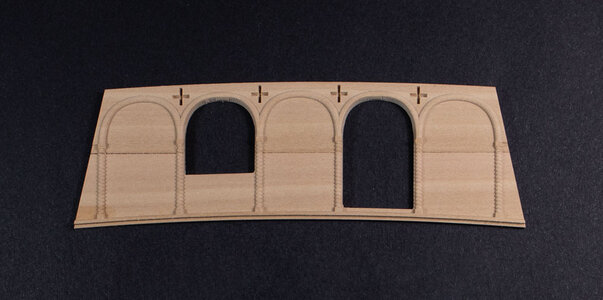
The result appeared fine to me. Therefore, I decided to proceed.
I made the material by gluing all the layers together and started machining.
At that time, the program (g-code) was conservative, too long, and not optimal.
Despite this, everything was going well, and I believed it would continue in the same manner.
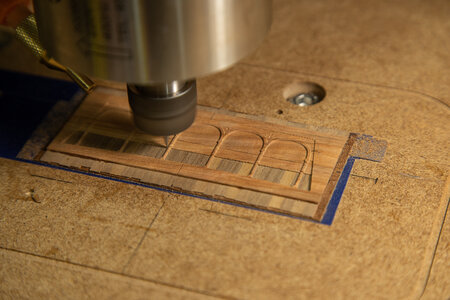
However, the power supply suddenly malfunctioned.
Between the power failures, I decided to reset the zero point but made a mistake in the process.
As a result, the walnut planks were cut too deeply, and in some areas, they were completely removed.
Furthermore, due to the power supply failures, the mill stopped a couple of times, causing the spindle to descend uncontrollably.
Consequently, you may notice a hole (with putty applied) created by the uncontrolled spindle.
Additionally, part of the pearwood column was broken, possibly due to the peeling of the walnut plank or insufficient glue between them.
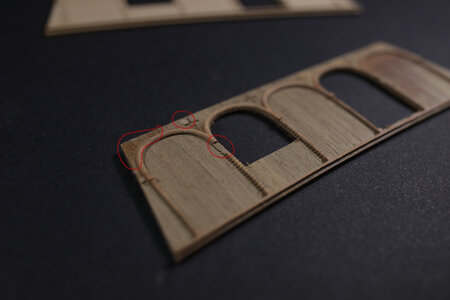
In general, I found the concept of using a composite material appealing. And perhaps, I will continue to explore it further. However, due to various reasons and issues, for this time, I have decided to take a simpler approach. I have returned to the "just pearwood" concept. But after another unsuccessful experiment, I decided to reinforce the material by gluing a veneer on the bottom side.
I have also made some minor changes to the design, including the addition of fake planking and a couple of shields on the wall.
These additions were made to incorporate more intricate details.
Below version represents the final model:
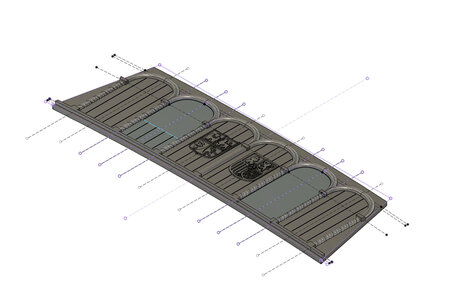
The rendered version:
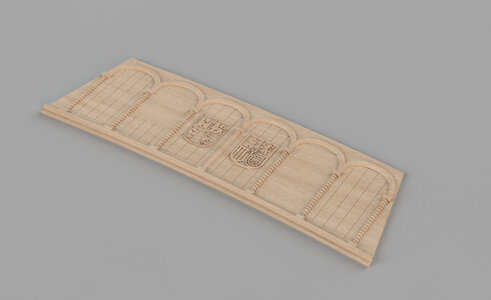
This time machining went well, and here is the result:
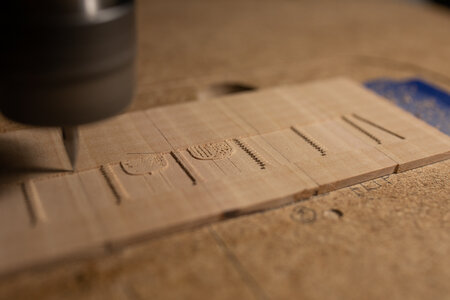
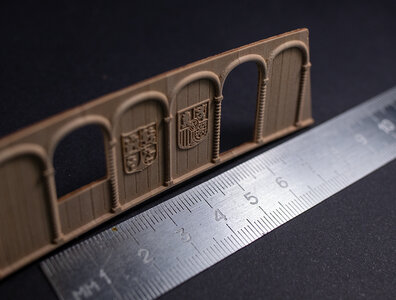
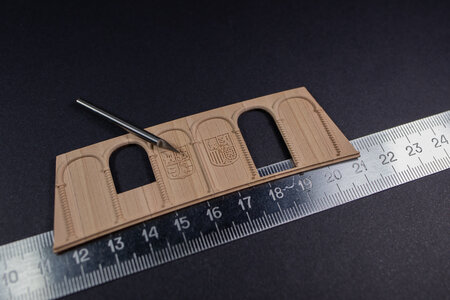
You may notice some "chips" on the curved surfaces, but they can be easily removed with a brush.
For the main tool, I used a 30° engraver with a 0.1mm end.
My conclusion:
In the end, I am pleased with the outcome.
Utilizing a CNC machine with a 0.1 mm engraving tool can yield remarkably sharp and precise details, even at a 1:65 scale.
I'm going to continue my experiments
Have a nice day!
Over the past few days, I have been troubleshooting an issue with my CNC machine. Finally, I discovered the culprit - one of the power supplies was experiencing undervoltage. Unfortunately, this led to a spoiled future part of the ship model. However, it also provided me with a better understanding of the limitations of CNC processing when working with composite wooden materials.
The experience appeared to be so valuable to me that I have decided to share it with you.
So. I've decided to upgrade the front wall of the admirals' cabin. Scale 1:65. Instead of just using planks, I decided to create a layered structure using veneer at the bottom, walnut planks in the middle, and pear wood on top. The idea is that after CNC machining, the relief parts of the wall will remain made of pear wood, while the rest of the pear wood will be machined out, revealing the walnut planking.
The pie should be like this (the concept, not a real part):
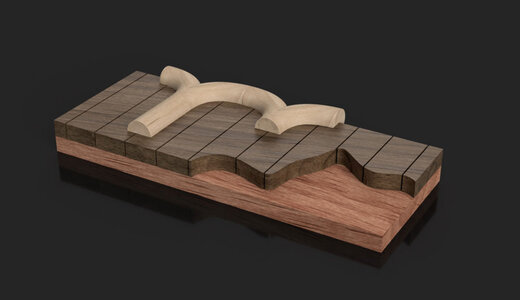
I designed a model in Fusion360. It took me some time

And even made a prototype - so far just form pearwood (no composite yet):
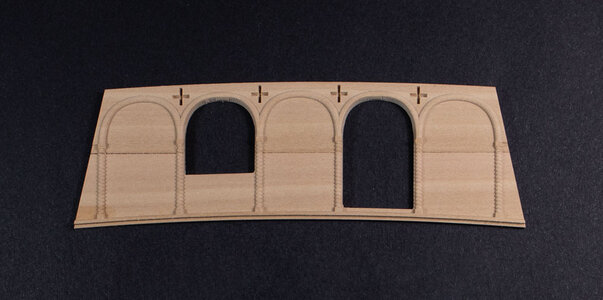
The result appeared fine to me. Therefore, I decided to proceed.
I made the material by gluing all the layers together and started machining.
At that time, the program (g-code) was conservative, too long, and not optimal.
Despite this, everything was going well, and I believed it would continue in the same manner.
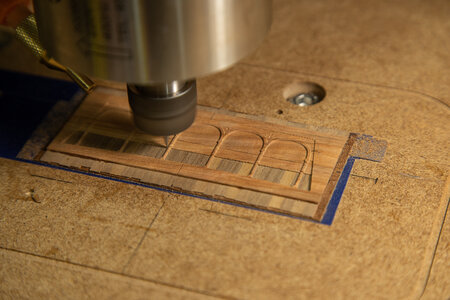
However, the power supply suddenly malfunctioned.
Between the power failures, I decided to reset the zero point but made a mistake in the process.
As a result, the walnut planks were cut too deeply, and in some areas, they were completely removed.
Furthermore, due to the power supply failures, the mill stopped a couple of times, causing the spindle to descend uncontrollably.
Consequently, you may notice a hole (with putty applied) created by the uncontrolled spindle.
Additionally, part of the pearwood column was broken, possibly due to the peeling of the walnut plank or insufficient glue between them.
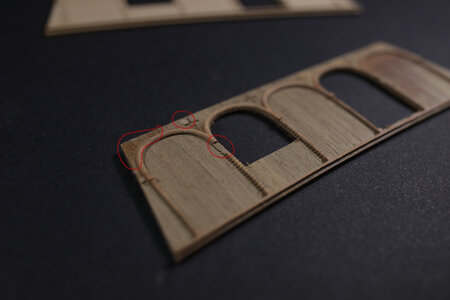
In general, I found the concept of using a composite material appealing. And perhaps, I will continue to explore it further. However, due to various reasons and issues, for this time, I have decided to take a simpler approach. I have returned to the "just pearwood" concept. But after another unsuccessful experiment, I decided to reinforce the material by gluing a veneer on the bottom side.
I have also made some minor changes to the design, including the addition of fake planking and a couple of shields on the wall.
These additions were made to incorporate more intricate details.
Below version represents the final model:
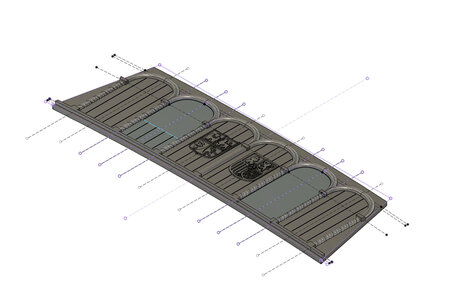
The rendered version:
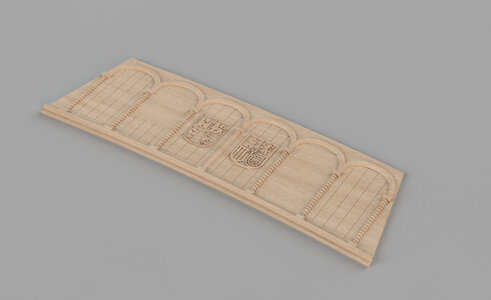
This time machining went well, and here is the result:
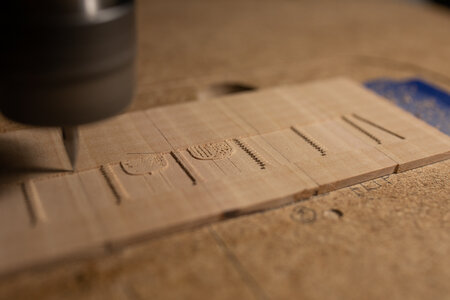
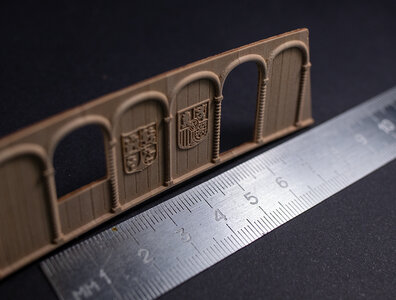
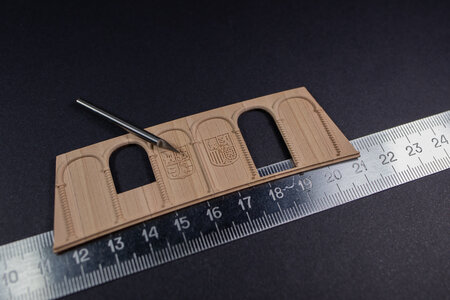
You may notice some "chips" on the curved surfaces, but they can be easily removed with a brush.
For the main tool, I used a 30° engraver with a 0.1mm end.
My conclusion:
In the end, I am pleased with the outcome.
Utilizing a CNC machine with a 0.1 mm engraving tool can yield remarkably sharp and precise details, even at a 1:65 scale.
I'm going to continue my experiments

Have a nice day!