- Joined
- Sep 23, 2021
- Messages
- 137
- Points
- 113
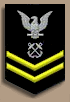
I will not be starting my next build for a while but I thought I would give it a “heads up” now that I have the kit in the shipyard.
Part 1 - Start of a Long Voyage
Choice of Kit - an Odd (or Familiar) Story?
The windjammers/clippers from the mid to late 19th century have always fascinated me for their sleek hull lines and sheer amount of sail. The Cutty Sark is a classic model to build of this type and there are a number of kits to choose from. I looked at some reviews and builds of Cutty Sark kits on the SOS forums and other web sites. Robertd’s recent build of the Sergal/Mantua kit < R'Ds CS > came out very nicely. I was intending to buy that kit later this year but I spotted an estate clearance auction listing for an “old” model boat kit of the Cutty Sark. It turned out to be Billing Boats BB564 complete with the separate fittings kit that had been purchased as a “project” but never started. I left a silly low commission bid and to my surprise won the auction. When I received it I found that it was still in its original shipping box and wrapping paper and had only been opened for inspection. The kit itself is in near mint condition, just some slight damage to the box where the sealing tape had been. The fittings box ( that you had to purchase separately back then) was unopened.

Judging from the postage labels the kit was bought in the mid 80’s and has spent the past 37+ years languishing at the back of a cupboard (it makes me wonder just how many model kits have been bought with good intentions but are now just collecting dust?).
I think that it is time for this Cutty Sark to see the light of day and spread her sails (probably not the Stuns’ls!).
Gathering My Thoughts on a Build Plan
Although it is not my first choice of kit it will be a good challenge (but I may also regret this one). It will also be the biggest model I have attempted. The completed model is 1.1m (43”) long and the desk I use for my hobby work is 1.4m wide so I am going to struggle (I also have no idea where I will put it when it’s done!). I am also sure that the rigging will test my patience (and my eyesight!) to the limit but that stage is a long way off into the future for now. I don’t have a lot of space to display my models so it is my intention to take my time over this build, add extra detail and make more parts from scratch. I think I will also need plenty of advice on building this one!
The kit is definitely “vintage” (no laser cut parts). I know that Billing kits from this time were not of the best quality but I will be using this as a base kit for the model build so I’m quite OK with the out-of-the-box quality issues from the day. All of the frames are jig cut and some of the ply parts are die-cut. Other detailing parts are just printed onto ply sheets and need to be cut out (I will probably just use them as templates and make new parts from solid wood). The decorative mouldings and service boats are plastic as are the rigging blocks and deadeyes. The rear transom decoration is a decal. The instructions are the usual basic ones from BB with four plan drawings of layout, sails, pins and rigging.
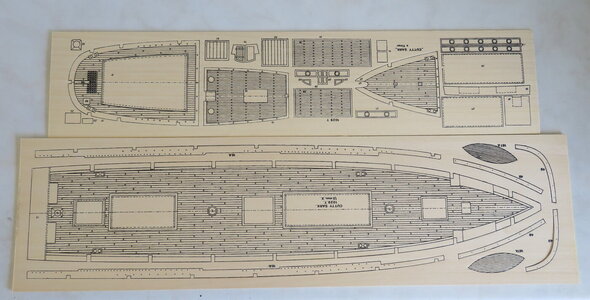
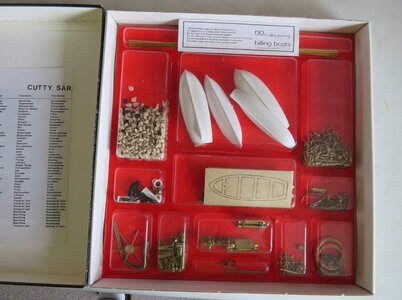
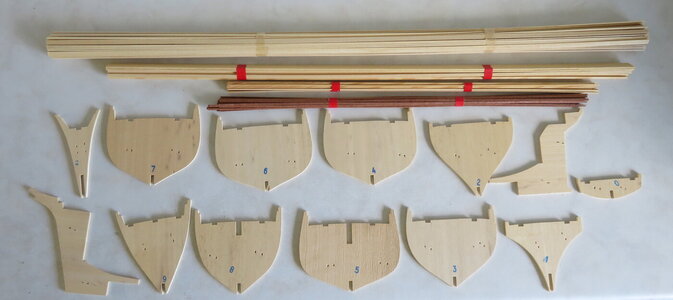
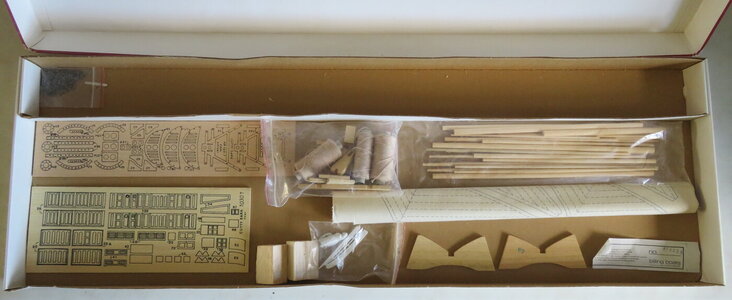
Because I paid very little for the kit I will upgrade it as I go through the build by replacing all of the plastic parts with wood/brass and making new parts where I think the model will benefit.
I have already purchased a set of photo-etched decor parts and a full set of walnut CNC rigging blocks from HisModel. The rigging blocks came in two sets, one for the standing rigging (224 pieces) and one for the running rigging (535 pieces). The blocks are of the correct type and size for this model (759 blocks to rig is however very intimidating!).
I will replace the plastic service boats with wooden ones of the correct type and scale. If anyone knows where I can find some suitable 1:75 kit replacements (or some scale plans so that I could make them myself) that would be great, please let me know through the forum.
I will also replace the rigging thread with some decent rope when I reach that point (I think I will purchase rather than try to make my own).
The BB kit has no hull plates included and the lower hull is suggested to be painted (I think even the latest version of this kit does not offer plates as an option). I would like to sheath the hull because the real ship was sheathed and I will consider options for that upgrade when I reach that point.
To help with the build and rigging I have bought a set of G.F. Campbell’s plans (General Layout, Rigging and Sail Plan) from the Royal Museums Greenwich. I also found Olha’s book review “Cutty Sark, The Ship and the Model/Longridge. C Nepean'' on her YouTube Channel < CS ref book > and I was able to locate a good used copy of the book in the UK. I do not intend to go the “whole hog” on the model by super-detailing it, my intention is to improve it to a level that I am happy with (whatever that is?).
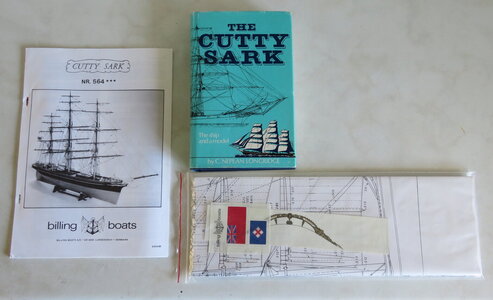
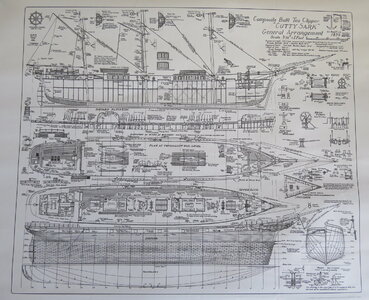
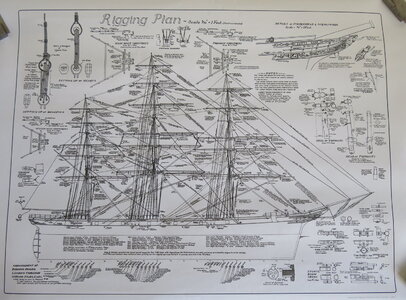
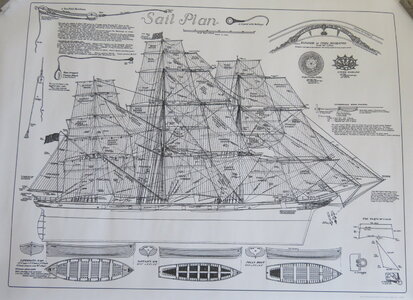
I will take a long holiday soon and I have some home improvement projects to do when I return, so it will be a while before I can get started on the framing (probably late autumn). Now that the pandemic is over (I hope!) I have many other things to do, so I will have less time to spend on the ship hobby. I will mainly work on this model during the winter weather months and I will intersperse the work between projects. I am expecting that I will be working on this one for quite some time to come (?years?!) but I am in no hurry.
I will give an update once I have kicked-off the framing.
Part 1 - Start of a Long Voyage
Choice of Kit - an Odd (or Familiar) Story?
The windjammers/clippers from the mid to late 19th century have always fascinated me for their sleek hull lines and sheer amount of sail. The Cutty Sark is a classic model to build of this type and there are a number of kits to choose from. I looked at some reviews and builds of Cutty Sark kits on the SOS forums and other web sites. Robertd’s recent build of the Sergal/Mantua kit < R'Ds CS > came out very nicely. I was intending to buy that kit later this year but I spotted an estate clearance auction listing for an “old” model boat kit of the Cutty Sark. It turned out to be Billing Boats BB564 complete with the separate fittings kit that had been purchased as a “project” but never started. I left a silly low commission bid and to my surprise won the auction. When I received it I found that it was still in its original shipping box and wrapping paper and had only been opened for inspection. The kit itself is in near mint condition, just some slight damage to the box where the sealing tape had been. The fittings box ( that you had to purchase separately back then) was unopened.

Judging from the postage labels the kit was bought in the mid 80’s and has spent the past 37+ years languishing at the back of a cupboard (it makes me wonder just how many model kits have been bought with good intentions but are now just collecting dust?).
I think that it is time for this Cutty Sark to see the light of day and spread her sails (probably not the Stuns’ls!).
Gathering My Thoughts on a Build Plan
Although it is not my first choice of kit it will be a good challenge (but I may also regret this one). It will also be the biggest model I have attempted. The completed model is 1.1m (43”) long and the desk I use for my hobby work is 1.4m wide so I am going to struggle (I also have no idea where I will put it when it’s done!). I am also sure that the rigging will test my patience (and my eyesight!) to the limit but that stage is a long way off into the future for now. I don’t have a lot of space to display my models so it is my intention to take my time over this build, add extra detail and make more parts from scratch. I think I will also need plenty of advice on building this one!
The kit is definitely “vintage” (no laser cut parts). I know that Billing kits from this time were not of the best quality but I will be using this as a base kit for the model build so I’m quite OK with the out-of-the-box quality issues from the day. All of the frames are jig cut and some of the ply parts are die-cut. Other detailing parts are just printed onto ply sheets and need to be cut out (I will probably just use them as templates and make new parts from solid wood). The decorative mouldings and service boats are plastic as are the rigging blocks and deadeyes. The rear transom decoration is a decal. The instructions are the usual basic ones from BB with four plan drawings of layout, sails, pins and rigging.
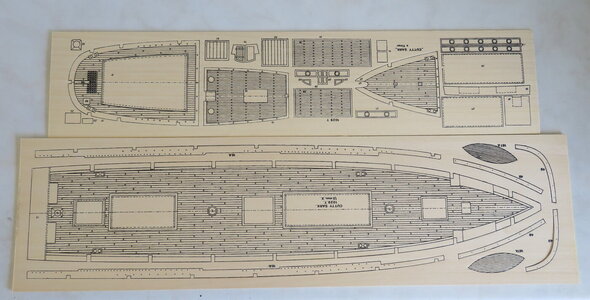
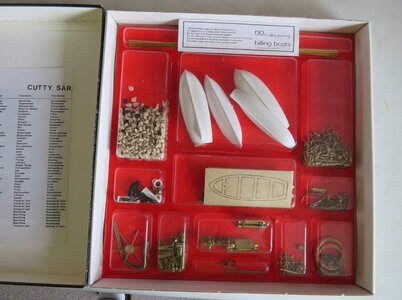
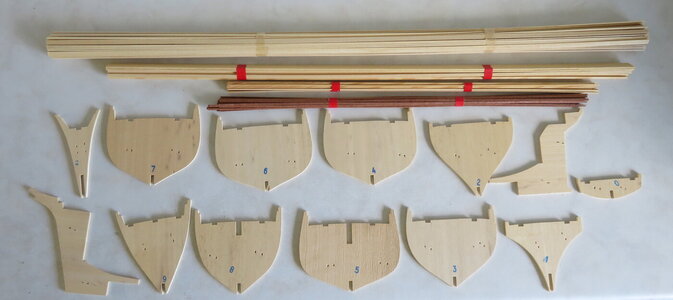
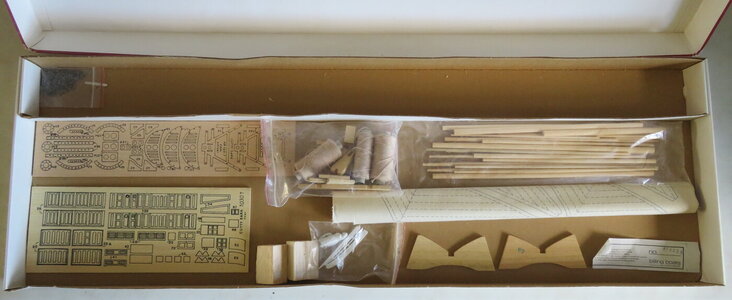
Because I paid very little for the kit I will upgrade it as I go through the build by replacing all of the plastic parts with wood/brass and making new parts where I think the model will benefit.
I have already purchased a set of photo-etched decor parts and a full set of walnut CNC rigging blocks from HisModel. The rigging blocks came in two sets, one for the standing rigging (224 pieces) and one for the running rigging (535 pieces). The blocks are of the correct type and size for this model (759 blocks to rig is however very intimidating!).
I will replace the plastic service boats with wooden ones of the correct type and scale. If anyone knows where I can find some suitable 1:75 kit replacements (or some scale plans so that I could make them myself) that would be great, please let me know through the forum.
I will also replace the rigging thread with some decent rope when I reach that point (I think I will purchase rather than try to make my own).
The BB kit has no hull plates included and the lower hull is suggested to be painted (I think even the latest version of this kit does not offer plates as an option). I would like to sheath the hull because the real ship was sheathed and I will consider options for that upgrade when I reach that point.
To help with the build and rigging I have bought a set of G.F. Campbell’s plans (General Layout, Rigging and Sail Plan) from the Royal Museums Greenwich. I also found Olha’s book review “Cutty Sark, The Ship and the Model/Longridge. C Nepean'' on her YouTube Channel < CS ref book > and I was able to locate a good used copy of the book in the UK. I do not intend to go the “whole hog” on the model by super-detailing it, my intention is to improve it to a level that I am happy with (whatever that is?).
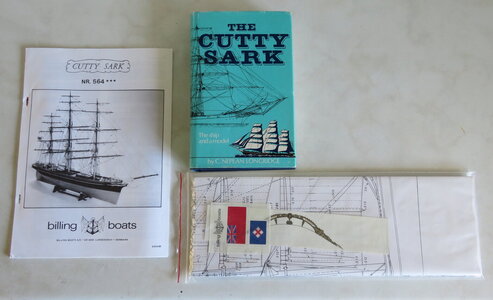
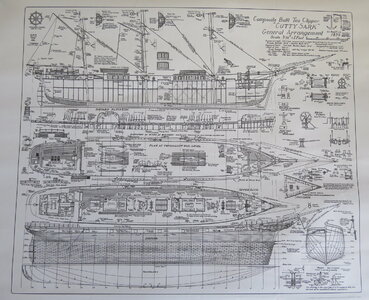
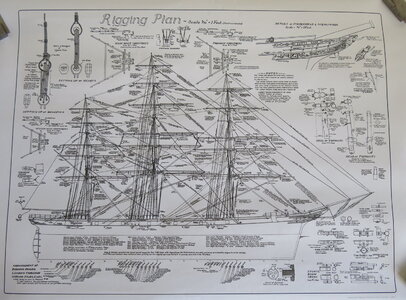
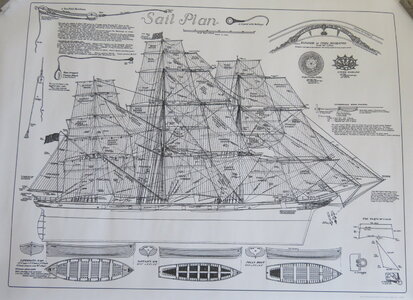
I will take a long holiday soon and I have some home improvement projects to do when I return, so it will be a while before I can get started on the framing (probably late autumn). Now that the pandemic is over (I hope!) I have many other things to do, so I will have less time to spend on the ship hobby. I will mainly work on this model during the winter weather months and I will intersperse the work between projects. I am expecting that I will be working on this one for quite some time to come (?years?!) but I am in no hurry.
I will give an update once I have kicked-off the framing.