A german friend is building the Le Fleuron based on the drawing set / monograph by our member Gerard @G. DELACROIX
Last spring I met Joachim and had the chance to see his model under construction.
Based on his request I was asked to open this topic, where he can start to show hie building log of his interesting model.
For now I can show the status of his model in spring
During this meeting Joachim´s Le FLEURON met my La SALAMANDRE
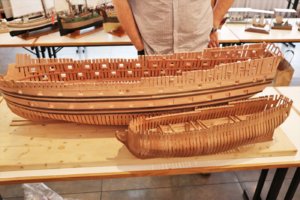
Here the planset review of the monograph:
So stay tuned - Joachim will post soon and show his model in much more details
Last spring I met Joachim and had the chance to see his model under construction.
Based on his request I was asked to open this topic, where he can start to show hie building log of his interesting model.
For now I can show the status of his model in spring
Regional Meeting of "Arbeitskreis Historischer Schiffbau" and forum "Segelschiffsmodellbau" near Frankfurt on 11th May 2019
Also some beautiful full working RC-models of sailing ships are shown...... Jörg Gebhard, alias Gebbi is building every year 4 to 6 of such vessels, at home he has appr. 90 models ready for the lake Many Thanks to Matthias that I can use his photo
shipsofscale.com
During this meeting Joachim´s Le FLEURON met my La SALAMANDRE
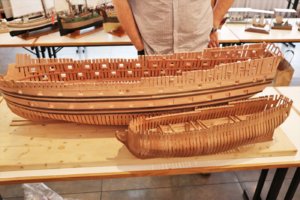
Here the planset review of the monograph:
Planset review - LE FLEURON - 64-gun Ship by Joseph & Blaise OLLIVIER" - 1729 - by Gerard Delacroix and Jean Boudriot
Planset Review: LE FLEURON 64-gun Ship by Joseph & Blaise OLLIVIER - 1729 by Gerard Delacroix and Jean Boudriot in scale 1:48 / english translation by Gilles Korent This monographie is available from ancre in different languages, which can be choosen - English / French / Italian or...
shipsofscale.com
So stay tuned - Joachim will post soon and show his model in much more details