Hi Everyone,
I've been trying to work my way up through different skill level kits to get to, some day, be able to build my own plank-on-frame scratch model. Now there seems to be a number of nice POF kits in quality hardwood from China and I, perhaps foolishly, decided to cut the line. I had been looking at David Antscherl's book from Seawatch on Hayling Hoy from the 1760's. It was to be my first POF scratch build, some day. It seemed like a good choice, but the primer for the book I bought turned out to be "The Fully Framed" model series of 4 books plus an optional on rigging. So, out of reach for someone who has built 5 kits and struggled with a hybrid scratch/kit project for traditional building techniques on 20th work boats. Until I saw some of these POF kits.
The real issue is payoff. I have some beautiful models I built but they are mostly basswood and airbrushing. Somehow, it's not the same as a hardwood POF with frames showing. I couldn't start of with the Sovereign of the Seas but found Hayling Hoy offered by Dry Dock Models and Parts. The price was right too. I ordered my kit in cherry, perhaps my favorite wood.
drydockmodelsandparts.com
I got the kit and, as I suspected, it's not for beginners. The biggest challenge that I have gathered from these Chinese models are the instructions. This one has nice illustrations and a short couple of pages of instructions, but there is still plenty left to imagination and the broken English can be a little tough at times. But I have heard of another one of the POF kits where the instructions are nearly incomprehensible. I think this manufacturer tried to make up for a lack of proper grammar by including excellent illustrations. I'll take it.
So here it is. My expectations are sky high but my goals are low. If I can get to the fully assembled frame and have done a nice job with it, I will be happy. Anything past that is all gravy.
I've been trying to work my way up through different skill level kits to get to, some day, be able to build my own plank-on-frame scratch model. Now there seems to be a number of nice POF kits in quality hardwood from China and I, perhaps foolishly, decided to cut the line. I had been looking at David Antscherl's book from Seawatch on Hayling Hoy from the 1760's. It was to be my first POF scratch build, some day. It seemed like a good choice, but the primer for the book I bought turned out to be "The Fully Framed" model series of 4 books plus an optional on rigging. So, out of reach for someone who has built 5 kits and struggled with a hybrid scratch/kit project for traditional building techniques on 20th work boats. Until I saw some of these POF kits.
The real issue is payoff. I have some beautiful models I built but they are mostly basswood and airbrushing. Somehow, it's not the same as a hardwood POF with frames showing. I couldn't start of with the Sovereign of the Seas but found Hayling Hoy offered by Dry Dock Models and Parts. The price was right too. I ordered my kit in cherry, perhaps my favorite wood.
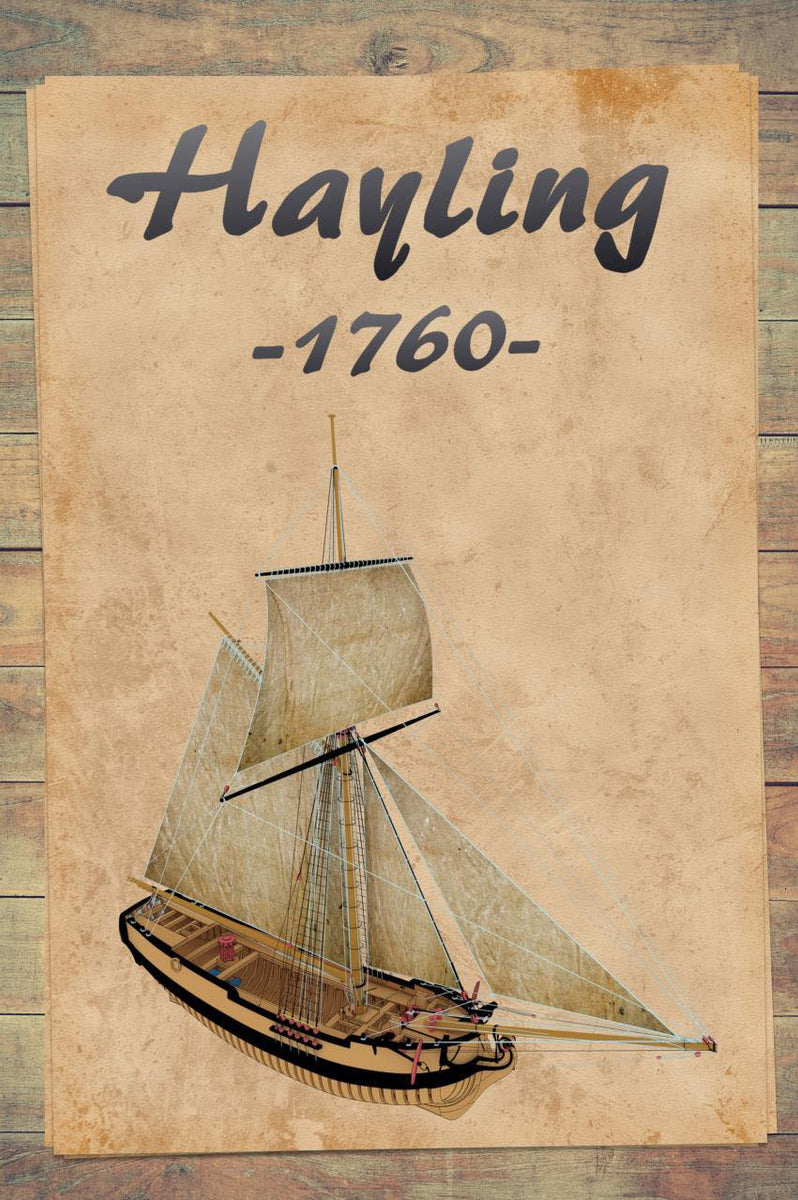
Hayling Hoy 1760 1:48 - CHERRY WOOD VERSION
Shipping is included in the total price!! Please allow 10 days to fulfill the order!! The product is shipped from China!! Dimensions Scale: 1:48 Length Overall: 675.5mm Height Overall: 653mm Width Overall: 341mm Width of Hull (only): 135mm Length of Hull (only): 488mm) Level: Intermediate to...
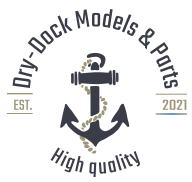
I got the kit and, as I suspected, it's not for beginners. The biggest challenge that I have gathered from these Chinese models are the instructions. This one has nice illustrations and a short couple of pages of instructions, but there is still plenty left to imagination and the broken English can be a little tough at times. But I have heard of another one of the POF kits where the instructions are nearly incomprehensible. I think this manufacturer tried to make up for a lack of proper grammar by including excellent illustrations. I'll take it.
So here it is. My expectations are sky high but my goals are low. If I can get to the fully assembled frame and have done a nice job with it, I will be happy. Anything past that is all gravy.
Last edited: