HM Sloop of War Cutter Alert (1777) - Vanguard Models 1/64
Sloop? Where did I get that from? It's a cutter.
Sloop? Where did I get that from? It's a cutter.
Ahoy there, my friends and fellow modellers! Welcome to my build log of Vanguard Models' excellent kit of Alert (1777). I'm sorry that you have already missed approximately half of the build which began in the spring of 2024. In fact, for some weeks I have hesitated to start in the middle like this. However, as I have read some of the excellent and enthralling logs here, I notice that many of them begin long after the laying of the keels, yet are as interesting as those that start with the opening of the box. So here we go.
For a long time after beginning Alert I took no photographs and made no notes but I can remember some of it. The framework of nine bulkheads, a false keel and two decks almost assembled itself; it was really that good. Everything fitted tightly and the design made it all self-aligning. I was very impressed to find I had a recognizable boat shape on my desk so quickly even allowing for the trimming of the keel plate at the bearding line. There was no need to cut a rabbet at the bow because the design includes one cut entirely through. I've never seen this on another model and it proved to be a very useful aid to planking.
First planking went well. The lime (?) stripwood was flexible and bent well. My bending process is to form sideways bends with a clothing iron first and then make face bends with a specialised plank bending tool that looks like a soldering iron with a big round aluminium head. This wasn't my first adventure in planking and the first layer went on easily. I have only completed two wooden models, The Artesia Latina Le Renard and the Amati New Bedford Whaleboat but I have built a few more hulls in projects that sadly were not completed.
I used the kit-supplied pins to hold the planks in place and glued them to the bulkheads with Titebond Original, my glue of choice. (Whenever I refer to 'glue' in this log, that's what I mean. If I'm using something else, I'll make a point of identifying it properly for you.)
At the second planking stage I began to diverge from the instructions. I'd noticed that the kit makes certain compromises, the hull planking is carvel built whereas the original was clinker built; she was copper bottomed; and there's a lot of PE scrollwork and painted decoration which owes a lot to the famous paintings of the model of Alert. I see these as an artist's impression of a modeller's representations of a shipbuilder's future plans rather than an accurate picture of the vessel afloat
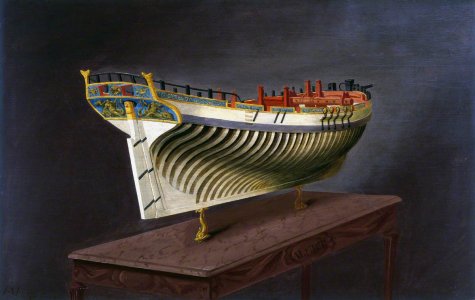
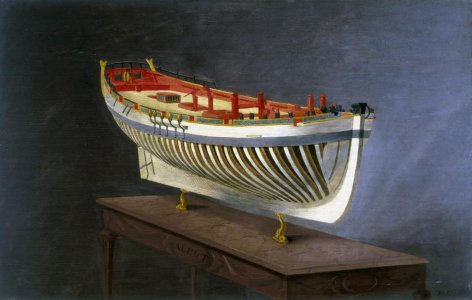
My alternate reference source is Peter Goodwin's Anatomy of the Ship - Alert and in there I discovered that the woodwork wasn't painted but treated with pine rosin, a varnish which would allow me to keep the wood visible. I like wood better than paint and if the wood is going to be visible, I thought, let's find some interesting timbers. I planked the outside of the bulwarks with walnut, deliberately choosing pieces of different colours for maximum effect. I'm not exactly subtle when it comes to aesthetics.

I thought about the clinker-built hull for ages. My Amati whaleboat was clinkered and I found it very challenging to build even with pre-cut plywood planks. I looked for a way to simulate the overlaps and found one that was reasonable easy to do and looked good enough for the narrow band of wood which would be visible above the coppering.

This is what it looked like. It's far from perfect but I was pleased enough with it to get my camera out.
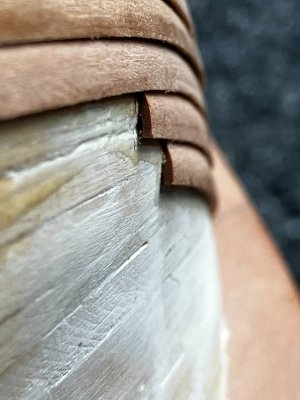
This is how I did the 'clinkering'. Each plank was sanded or scraped to a knife edge at the top and this was fitted into a small rabbet which I scraped into the underneath of the previously fitted plank. This made things nice and tidy and also helped hold the planks in place while the glue set. I didn't use clamps but simply held each plank in place with fingers for ten minutes while the glue set. I have the impression that Titebond has two resin components, one that sets fast in just a few minutes and then another one that sets hard overnight. Since I didn't want to risk dislodging the previous plank when I scraped out the little rabbets, progress was limited to a strake per day, which I was applying in three scale 20 foot lengths. I find that much easier than doing a whole strake in one piece and I think it looks better and more interesting too.
By the way, I'm using this build as a training exercise. I'm much more interested in building my skills and experience than I am in building a perfect model at this stage in my modelling career. Having fun is even more important to me.

I also enjoy telling the story of the build and the conversations that we can all have about it. I'm in my late sixties and really appreciate how marvellous it is to be able to chat with other modellers from all over the world. We have so much in common despite our different countries and cultures and with Google translate even the language barriers are (almost) gone. I want to write this story here on SOS because of this. Collectively we know a lot about our hobby and we can share our technical expertise here AND it's a friendly site with an amazingly positive attitude. Not all sites are like this, of course. I know one where the skill and knowledge is high but the friendliness is lacking, which is a great shame. I know another, which is very friendly and chatty but most of the modelling is plastic aircraft based. SOS seems to be the best of all possible places for me to write my story.
I invite readers to join in with suggestions, support, chatter and criticism. Please don't be shy; tell me when I've done something wrong or badly - I'm a new guy to the hobby and there's much for me to learn. Even tell me when I write too much, because I do ramble on if nobody raps my knuckles from time to time.

I'll continue to bring you up to date with the build in my next few posts. See you very soon.
Last edited: