Despite the skepticism surrounding 3D-printed parts—some consider them inauthentic and not canonical since they're not made of wood or metal—I hold a slightly different opinion. If printed parts look good and are well-painted, does it really matter what lies beneath the paint? If this process can simplify or speed up production, why not take advantage of it? I've always been intrigued by new possibilities, especially those that help me overcome my laziness. After all, modeling one part and replicating it multiple times is far more efficient than crafting each piece individually.
I’m building HMS Victory, and in this thread, I plan to compile links to the posts in my build diary that touch on 3D modeling, printing, and creating finished parts from printed blanks. This includes error handling, software setup and parameters, life hacks, and, of course, practical examples of production. Along the way, I’ve created a kind of counter to track the parts I’ve made using 3D printing. So, let’s dive in!
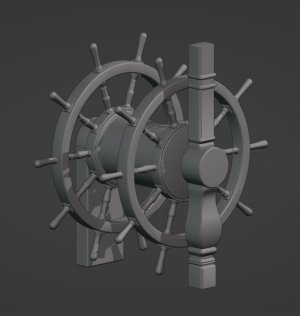
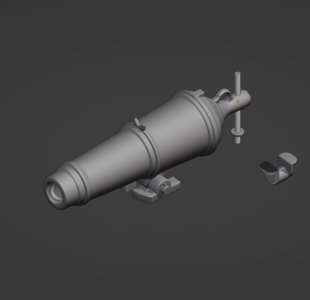
This is the introductory section (prologue), where I discuss errors such as:
1. Issues with scaling,
2. Correct positioning and supports,
3. Eliminating visible print layers, post-processing, and painting, etc.
>>> Link to the post "Errors in 3D" <<<

I’m building HMS Victory, and in this thread, I plan to compile links to the posts in my build diary that touch on 3D modeling, printing, and creating finished parts from printed blanks. This includes error handling, software setup and parameters, life hacks, and, of course, practical examples of production. Along the way, I’ve created a kind of counter to track the parts I’ve made using 3D printing. So, let’s dive in!
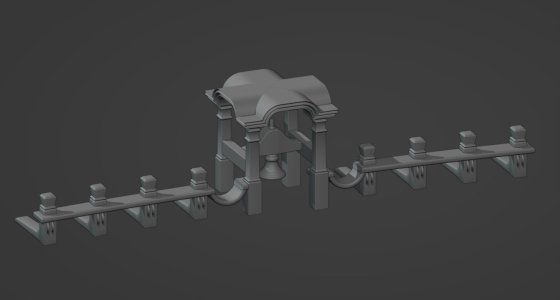
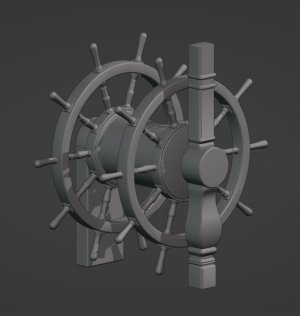
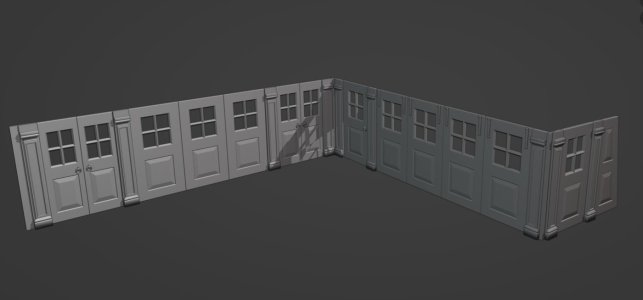
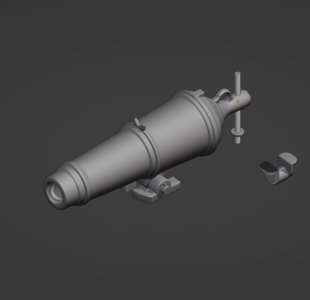
This is the introductory section (prologue), where I discuss errors such as:
1. Issues with scaling,
2. Correct positioning and supports,
3. Eliminating visible print layers, post-processing, and painting, etc.
>>> Link to the post "Errors in 3D" <<<
