- Joined
- Sep 3, 2021
- Messages
- 5,045
- Points
- 738
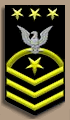
Whilst progressing the construction of the torsion box, I became more and more concerned about the torsional stability of the center box. Evergreen is a rather easy material to work with, easy to cut, easy to connect, using adhesive, but it doesn't provide much stability. I think that it's due to the geometry of the center box; the box is rather narrow and slender and due to the envisioned build sequence, I need to have one of the sides of the box open for as long as I can. This means I don't have much of a resistance against torsion. Long story short, I restarted the build of the torsion box, using brass as material for the RH web and the closing panels, upper and lower, fwd and aft.
Also some progress was made with the rotor mast; I added provision for the attachment of the rotor head/gearbox and drilled a number of holes for the feed through of the tail rotor shaft and the cross tube of the landing gear.
Iso view of torsion box and instrument panel:
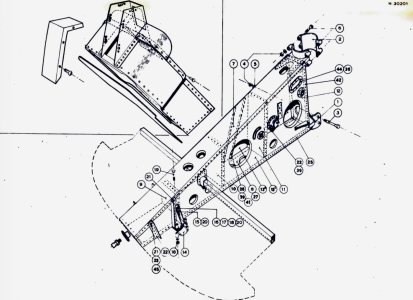
Iso view of rotor mast assembly :

My interpretation of the torsion box and the rotor mast (btw, all is CA bonded):

Also some progress was made with the rotor mast; I added provision for the attachment of the rotor head/gearbox and drilled a number of holes for the feed through of the tail rotor shaft and the cross tube of the landing gear.
Iso view of torsion box and instrument panel:
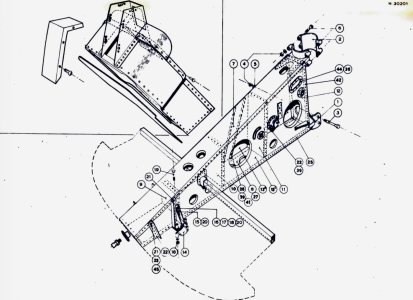
Iso view of rotor mast assembly :

My interpretation of the torsion box and the rotor mast (btw, all is CA bonded):
