- Joined
- Sep 10, 2024
- Messages
- 571
- Points
- 308
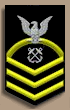
Frames (cont'd)
Work continues on the Oseberg's frames. Once the main frames had dried, it was time to clean up the fit between the thwart and the frames. Reversing the thwart helped by reverse-matching the char bevel, but it wasn't as close a fit as I would like. The zig-zaggy joint between the two made the job challenging. Taking off just a little too much in one spot opened up a gap in another. Just be careful and with needle files, use a light touch with lots of test fitting. The thwarts were then taped on to keep them with their respective frame. Then I beveled the notches that receive the strakes to the guidelines engraved on the ribs. The closer you get to the stems, the steeper the bevel and the more you have to slant that bevel upwards. There are also notches (covered up with tape here) where a stringer passes through for the full length of the hull on each side. I made sure the stringer fit with the thwart on.

On the smaller frames, I used a knife to cut in the upwards facing angle and then files and sanding sticks to bevel the edges. There will no doubt be some adjustment needed as I fit the strakes.

The only single frame is the center one. Its thwart has a doubler glued on with a circular notch facing astern to support the mast. There is a paper template supplied to locate the notch and to taper the doubler.
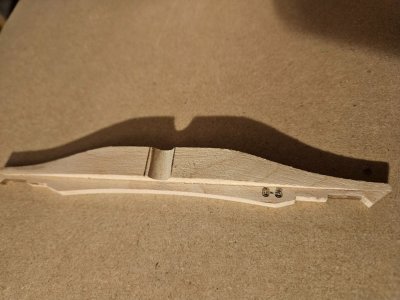
The next step is to fit the frames to their respective slots in the keel. Holding the thwart in place, I block-sanded the faces of the frames and thwarts. The keel is symmetrical, but I marked the ends for bow and stern. As I adjusted the notches in both the keel and the frame, I marked each frame and it's respective thwart with (B)ow and (S)tern.
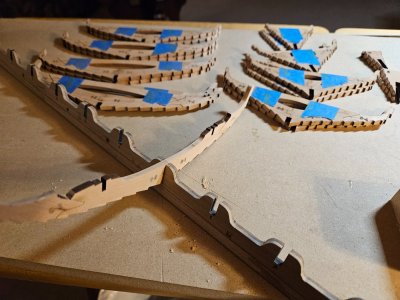
Once each frame was fitted to its respective slot in the keel, it was time to test the fit in the jig. I marked up the jig for bow and stern as well as the frame numbers. The only notches in the jig that needed widening were for the keel along the bottom. I also beveled the bottoms of the long notches where the stems rest. The stringers are visible in the next photos.
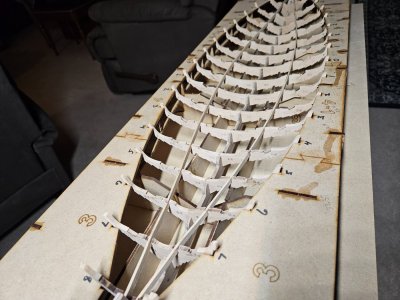
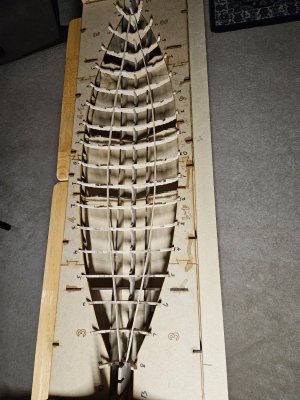
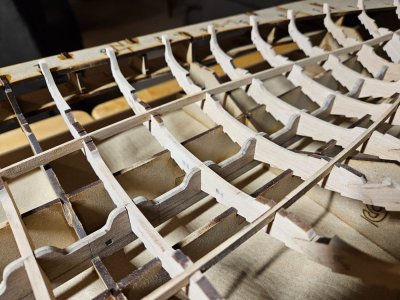
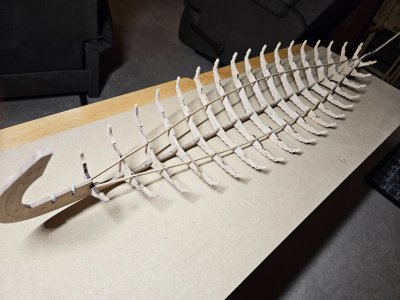
The next step will be go take everything apart and glue the frames to the keel in the jig. Not tonight.
Work continues on the Oseberg's frames. Once the main frames had dried, it was time to clean up the fit between the thwart and the frames. Reversing the thwart helped by reverse-matching the char bevel, but it wasn't as close a fit as I would like. The zig-zaggy joint between the two made the job challenging. Taking off just a little too much in one spot opened up a gap in another. Just be careful and with needle files, use a light touch with lots of test fitting. The thwarts were then taped on to keep them with their respective frame. Then I beveled the notches that receive the strakes to the guidelines engraved on the ribs. The closer you get to the stems, the steeper the bevel and the more you have to slant that bevel upwards. There are also notches (covered up with tape here) where a stringer passes through for the full length of the hull on each side. I made sure the stringer fit with the thwart on.

On the smaller frames, I used a knife to cut in the upwards facing angle and then files and sanding sticks to bevel the edges. There will no doubt be some adjustment needed as I fit the strakes.

The only single frame is the center one. Its thwart has a doubler glued on with a circular notch facing astern to support the mast. There is a paper template supplied to locate the notch and to taper the doubler.
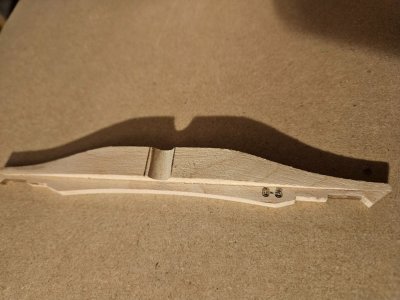
The next step is to fit the frames to their respective slots in the keel. Holding the thwart in place, I block-sanded the faces of the frames and thwarts. The keel is symmetrical, but I marked the ends for bow and stern. As I adjusted the notches in both the keel and the frame, I marked each frame and it's respective thwart with (B)ow and (S)tern.
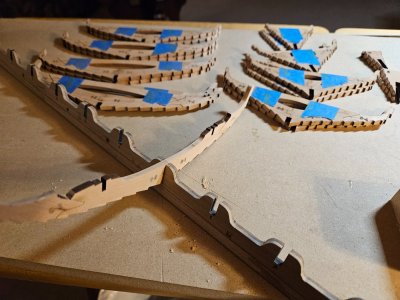
Once each frame was fitted to its respective slot in the keel, it was time to test the fit in the jig. I marked up the jig for bow and stern as well as the frame numbers. The only notches in the jig that needed widening were for the keel along the bottom. I also beveled the bottoms of the long notches where the stems rest. The stringers are visible in the next photos.
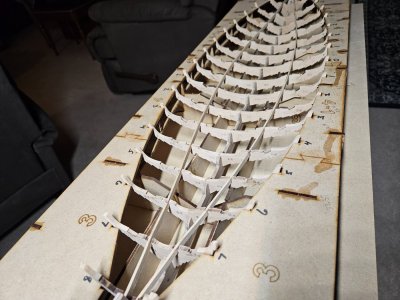
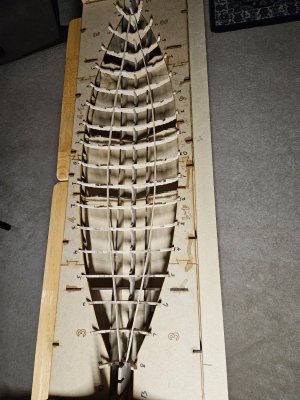
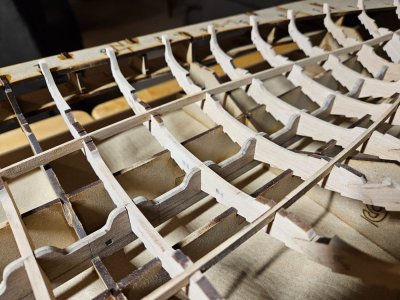
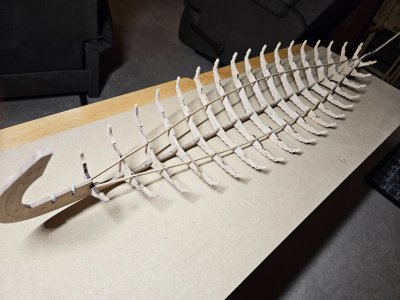
The next step will be go take everything apart and glue the frames to the keel in the jig. Not tonight.
