- Joined
- Dec 1, 2016
- Messages
- 6,049
- Points
- 728
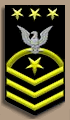
![]() |
As a way to introduce our brass coins to the community, we will raffle off a free coin during the month of August. Follow link ABOVE for instructions for entering. |
![]() |
Nicely Done Brother
the problem with most screw vices is the screw end will lift as the vice tightened. I have been through this looking for a Machinist vice the best I have found to combat the problem is a Screwless Vice. They aren't cheap but they are a must have for any serious Machinist and in this case Possibly a good choice for Hobbyist. Screwless vices don't lift your work up and the Jaws always remain Square no matter what.
this one should work well for sure unfortunately many aren't built as nice as this one appears to be.this is very true most vice jaws move up because the movable jaw just rides on the jaw base but this little gem stays put.
View attachment 58722
when you flip it over there is a plate screwed to the bottom of the jaw that rides on a channel which prevents the jaw from moving up
View attachment 58723View attachment 58724