- Joined
- Dec 1, 2016
- Messages
- 6,049
- Points
- 728
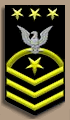
the last section of the stern to refine is planking of the counter which is the area built to overhang the stern post and the rudder goes up through.
It is the area between the two moldings
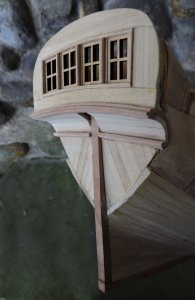
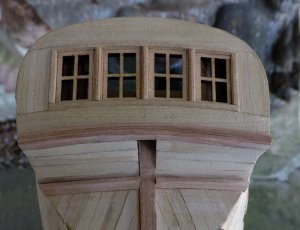
the few planks that make up the counter follow the curve of the stern which was established when the stern filler blocks were shaped. The only thing to watch is having to slightly bevel the edges so the planks will fit tight to one another as they conform to the arc of the stern.
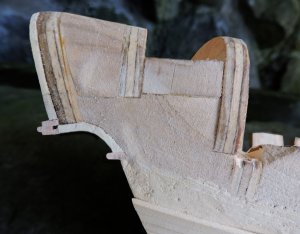
the stern is now done and time to move on to the bulwarks and gun ports
It is the area between the two moldings
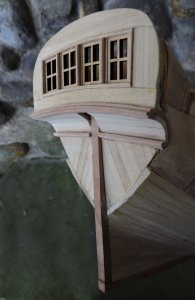
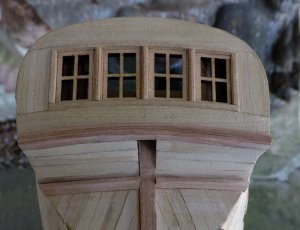
the few planks that make up the counter follow the curve of the stern which was established when the stern filler blocks were shaped. The only thing to watch is having to slightly bevel the edges so the planks will fit tight to one another as they conform to the arc of the stern.
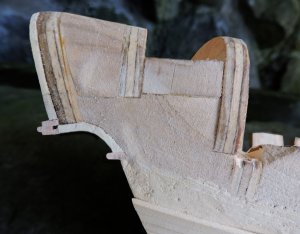
the stern is now done and time to move on to the bulwarks and gun ports