I've been experimenting with methods for assembly of the 24 large barrels that are included with the optional interior for the kit. Before building them, however, I fIrstwanted to decide if I wanted to use them. I've checked their actual size against the size of scale barrels. The largest barrel used on this, and most ships of the era, was the Tun, normally used for storing water. A surprise to me, these were usually loaded at the bottom of the cargo and supported and partially surrounded by stone ballast. They were NOT loaded and unloaded to be used or outfitted, they stayed in place, and were filled with a hose and pump, and were emptied the same way. Anyhow, the Tun, according to Boudriot's book on The Seventy Four, was 1.49 meters high and 1.096 meters in diameter. In 1/48 scale, that means the model tun should be 31mm high and 23mm in diameter. The barrels included with this kit turn out to be 33.4mm high and 25.2mm in diameter. or about 8-10% too large.
My first thought was to have my son make 3D printed barrels instead. I would copy Boudriot's loading diagram, with both tun and other sizes of barrels. And if I had the 3D printer and could make them myself, I'd have done that. But that would take on the order of 80 larger barrels, and well over 100 smaller barrels, and as much as he complained when he made the 50 or so barrels for my HMS Victory cross section, I decided not to do that. So, since we're talking about barrels less than 10% too large, and there are
always modifications from exact scale in scale models, and since these barrels look SO good, I decided to go with the 24 large ones included, and a yet-to-be-determined number of the small ones (wish they'd included medium size instead of those that are so small).
As those who have built or looked at the kit, each large barrel consists of 11 laser-cut structural pieces, 2 "planked" laser-cut finish pieces in pear (or whatever your kit is made with), and 20 planks. The 11 structure parts don't fit together nearly as tightly as they should, IMHO, so while assembling them is easy, it's a bit messy, with white glue dripping out here and there. After they're assembled, make sure everything is pushed in tightly, the ends are square and in place, and above all, make sure the ends are square with the ribs. It's easy to assemble them and set them down to dry, and not realize that the barrel is tiling to one size, or even assembled in a spiral sort of manner.
Next I put on the finished ends. I tried gluing them in place with white glue, to give me time to get them centered, but quickly found that didn't work: The 0.4mm (0.020") thick wood expands on the "wet" side of the glue, and while you're looking elsewhere, it turns into an arc, with only its center touching the barrel ends. I found it best to use a gel superglue (I used Titebond Instant Bond Wood Adhesive, Gel).
After that has dried, you get to glue on 20 separate wood strips for staves, each properly shaped, into place, curved to the contour of the barrel. While the staves break easily from their laser-cut sheet, I found it necessary to trim the sides of each in 4 places, where they are held to the wood when laser-cutting, also removing additional slivers of wood (which easily puncture a finger - I'm a porcupine now). But once shaped, how best to glue these 20 pieces and hold them in position, finishing the 24 barrels (792 separate parts) in a reasonable time. I tried a number of methods:
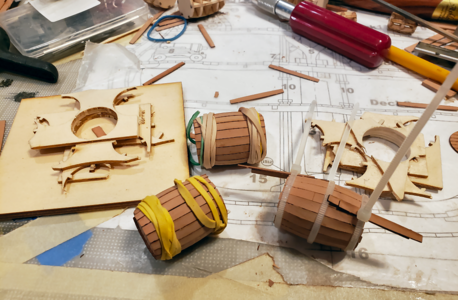
My first thought was to use the openings that the barrel forms were cut from to hold the staves in place while gluing.
First, I tried just holding the staves in place, while gluing in the proper position, and that was a nightmare.
At upper left, I took several pieces from the various size barrel baffles, glued them together and sanded them to a taper. The small piece of pear scrap in the bottom was to provide a stop for the end of the barrel and allow the staves to overlap slightly. My procedure was to place the barrel structure in the opening, place a bit of glue on a stave, and stick it in between the structure and the "form", to get one side glued in place. Turns out it wasn't failsafe in locating the staves (or I couldn't see them properly), and when removed after dry, I still had to put glue on the other side of the staves, then hold them all in place, which I did with rubber bands.
I then made another form (upper right in the above pic), which I thought if I glued the center of each stave in place, I could place this form over the end, one or both at a time, rotating and bring the staves in contact with the ends. That was a nightmare as well, and just ended up with sticky staves covering my worktop, floor and fingers.
And of course, I experimented with rubber bands and tape, etc. in trying to keep the staves in position. What a mess!
My final result used tie-wraps, those nylon straps that lock in place, and have to be cut loose. For me, that worked out best, so I'll outline my procedure in adding the staves to the barrels here:
I start with the barrel structure with the finished ends and cross-brace already in place. Again, use superglue for attaching the thin ends; water-based glue warps them. I also attached the cross-braces and left them a bit long, as I intend to sand the ends just a bit.
Apply glue to part of the outside of the barrel. I found I was able to apply it to half of the barrel, enough to attach 20 staves. More was too messy, and less wasn't necessary. When applying the glue, it is VERY IMPORTANT to cover the outer ribs (to properly fix them once curved) and the center rib (to keep it in place in the meantime).
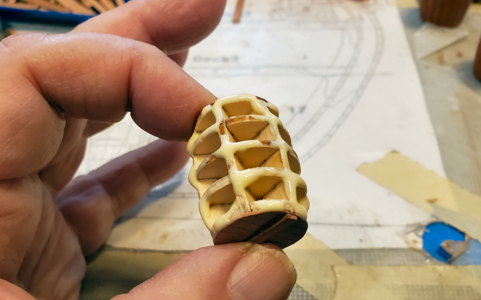
As to glue type, I tried Titebond Quick & Thick, but it dries to quickly to do this. I then went to Elmer's Glue-All, but felt it getting a bit dry on the last stave too. I then ordered Titebond Extend Wood Glue, which has a longer working time. It's a bit runny, but worked better for me. Most of the extra glue you see above stays on the inside and doesn't really make a mess.
Start at a vertical brace, and begin place staves in place. Glue keeps them in place well, just don't touch them after placed. I placed each stave close to its neighbor, but you don't need to push them tight. Fairly loose fit comes out right to 20 staves.
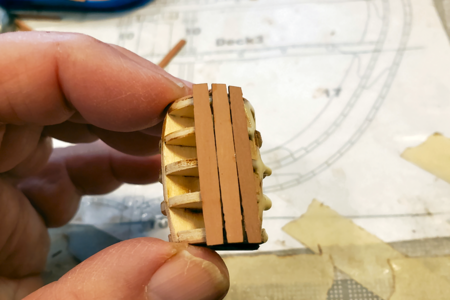
At first, I started keeping the cleaner side of the staves (the side away from the laser burning which can cause more discoloration), but ended up putting them in at random. This is not furniture, after all, and variations are expected
After finishing a glued section, apply more glue and continue.

After applying all the staves, you are holding a fully assembled barrel:
I then place a lightweight, 6" long zip-tie around the middle, and tighten it securely. Make sure the staves are at right angle, don't overlap or leave spaces. I can usually accept small variations, as I can always put that side down.
I then place two more zip ties on, near the center, but not as tightly:
Shift the outer ties toward the outside, closing the gaps on the staves, and tighten as you go. You can rotate the ties somewhat to help snug the staves in place. Some want to stick out, rotate to have the smooth are cover them:
Where staves are not held tight, small pieces of scrap can be placed to help keep them in place:
8 barrels now with staves, drying:
After dry, remove the zip ties (they slide off, and can't be used again). Should any staves stick up, I super glue them and use an accelerator to freeze them in place. Here are 3 finished barrels:
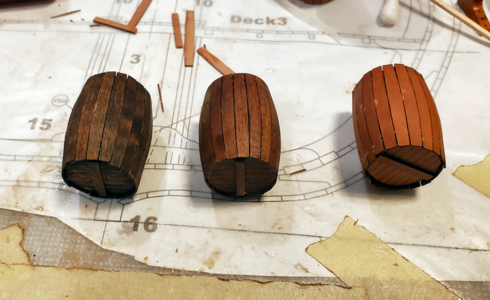
The one on the right only has Danish oil on it. I wanted more contrast for them in the hold, so the one of the left has Minwax Dark Walnut stain. I found that using Danish Oil first, then staining over, gave a nice shade and moderated the blotching some, so I'm going that way.
Hope this helps.