Thank you all for your likes and kind comments. As was the case with the chains, I’ve been experimenting and taking my first baby steps with rigging techniques.
Specifically, I’ve been learning to strop 2mm single blocks for my main deck haul-out tackles. As I mentioned in an earlier post, I will not use scale rope for these, as the line gauge is fine enough to get away with much cheaper thread, of which I have an abundant supply.
Abundance is what I have needed, here, because I have tried a number of different approaches to both minimize any space between the hook and block, while also stropping the block in a neat and tidy fashion.
I was really struggling on that front. And, that’s when I decided to consult with two of my favorite plastics builders: Michael D and Daniel Fischer. Both are outstanding at creating very correct looking rig, using ingenious technique in relatively small scales.
I need 24 of these single block tackles for the visible guns that will be rigged. I had made 9 that were variously unsatisfactory. Dan’s Victory log is particularly illustrative of small things I could do to achieve better results.
Initially, I was using two overhand knots (alternating from one side to the other), with the finest linen thread I posses, in order to strop the hooks. With a spot of CA, and the help of a simple pin jig to hold the block, I’d center the hook on the block and smooth the line into the groove until the CA set. Then, I’d use the same linen thread and an alternating overhand knot technique to seize below the block. A spot of CA seals the seizing and I nip the excess clean. This was my best result using this technique:

It’s okay, but I wasn’t really happy with it. From Daniel, I realized I could secure the hook with one overhand knot and then secure at the top of the block, as before. Now, while Dan often employs the alternating knot technique for simple seizings, he often uses fly-tying thread which, I am given to understand, flattens out as you wrap it. Dan’s simple seizings look great, and I think the flattening aspect of this type of line is the key.
So with those tips in mind, I tried again. Using a binder clip to keep the strop ends taught, I found that I could do a single overhand knot close to the block, followed by six conventional wraps to get a seizing that looked proportional:
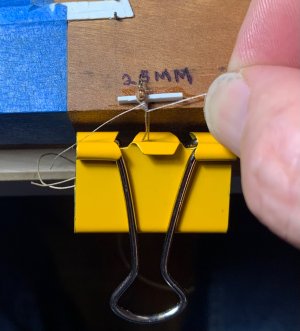
Now, I will be buying a set of alligator hands, as Dan Pariser previously suggested. I will also pick up some fly-tying line to experiment with. For the time being, though, this is both manageable and repeatable. Here is a side by side comparison:
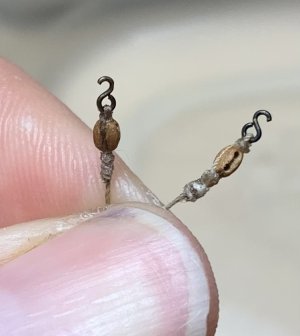
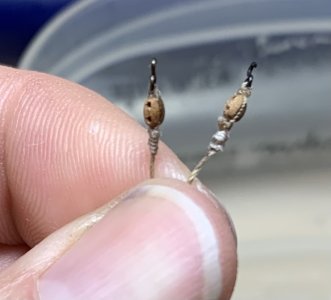
Now that I have an approach that I like, I dipped all of the previous tackles in acetone, so that I could salvage my blocks and hooks:

Any remaining glue residue brushes away with an old tooth brush.
Well, it isn’t much, but it is progress of a sort and I feel good about it. Thank you all for looking in!
Specifically, I’ve been learning to strop 2mm single blocks for my main deck haul-out tackles. As I mentioned in an earlier post, I will not use scale rope for these, as the line gauge is fine enough to get away with much cheaper thread, of which I have an abundant supply.
Abundance is what I have needed, here, because I have tried a number of different approaches to both minimize any space between the hook and block, while also stropping the block in a neat and tidy fashion.
I was really struggling on that front. And, that’s when I decided to consult with two of my favorite plastics builders: Michael D and Daniel Fischer. Both are outstanding at creating very correct looking rig, using ingenious technique in relatively small scales.
I need 24 of these single block tackles for the visible guns that will be rigged. I had made 9 that were variously unsatisfactory. Dan’s Victory log is particularly illustrative of small things I could do to achieve better results.
Initially, I was using two overhand knots (alternating from one side to the other), with the finest linen thread I posses, in order to strop the hooks. With a spot of CA, and the help of a simple pin jig to hold the block, I’d center the hook on the block and smooth the line into the groove until the CA set. Then, I’d use the same linen thread and an alternating overhand knot technique to seize below the block. A spot of CA seals the seizing and I nip the excess clean. This was my best result using this technique:

It’s okay, but I wasn’t really happy with it. From Daniel, I realized I could secure the hook with one overhand knot and then secure at the top of the block, as before. Now, while Dan often employs the alternating knot technique for simple seizings, he often uses fly-tying thread which, I am given to understand, flattens out as you wrap it. Dan’s simple seizings look great, and I think the flattening aspect of this type of line is the key.
So with those tips in mind, I tried again. Using a binder clip to keep the strop ends taught, I found that I could do a single overhand knot close to the block, followed by six conventional wraps to get a seizing that looked proportional:
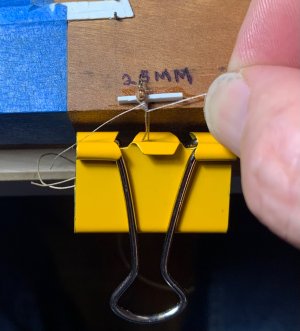
Now, I will be buying a set of alligator hands, as Dan Pariser previously suggested. I will also pick up some fly-tying line to experiment with. For the time being, though, this is both manageable and repeatable. Here is a side by side comparison:
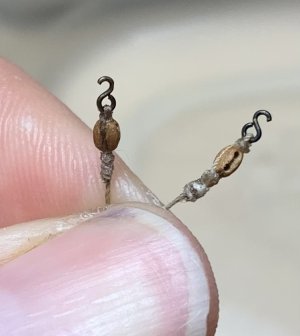
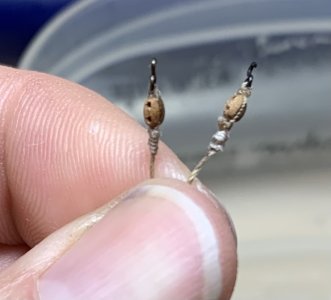
Now that I have an approach that I like, I dipped all of the previous tackles in acetone, so that I could salvage my blocks and hooks:

Any remaining glue residue brushes away with an old tooth brush.
Well, it isn’t much, but it is progress of a sort and I feel good about it. Thank you all for looking in!