Fore Platform Bulkheads.
Although TFFM says similar to aft, plan and Vardas seem to show a continuous wall rather than above and below a “lip”. Perhaps because there the bulkhead above the platform is incomplete or its’ beam sits below this lip
In any case, rather than separate upper and lower segments (and different wood) the aft bulkhead of the fore platforms is made as the walls. It also is separated from the fore platform to allow room for the uprights of the Bitts.
There is a central gap (without a door).
Door only to aftmost room-access to others via scuttles.
Note also no pillar to #5 lower deck beam.
Stanchions are 2.12 mm square.-some are already located where recesses already made in the platform planking.
(the rabbeting suggested as a possibility will be omitted)
Rooms on the port side looking foreward are Blockroom,Coal hole and Boatswain’s store room.
Middle bulkhead-extends across from side to side. Against and supported by the #4 pillar.
Similarly, the fore bulkhead, has no gap or door.
Finally, a fore/aft wall from this bulkhead the stem. This runs off-center to port to allow for the fore mast.
This is a bit fiddly as it must be cut to allow for the Breast Hooks.
( The Ring Bitt uprights are partially made now to allow fitting of the gap in the planking and shaping of their “feet”. These are 6.9mm square and a generous 11cm long- separated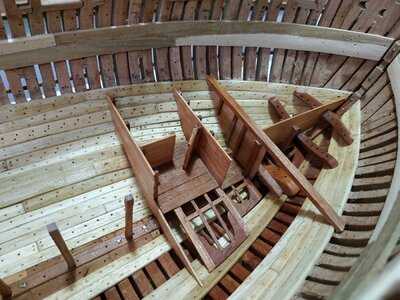
at 23.85mm gap. The fore aspect, below level of the upper deck , narrows to 5.50mmThis was done by milling as shown. The wood is black hornbeam - a contrast to avoid painting!)
Although TFFM says similar to aft, plan and Vardas seem to show a continuous wall rather than above and below a “lip”. Perhaps because there the bulkhead above the platform is incomplete or its’ beam sits below this lip
In any case, rather than separate upper and lower segments (and different wood) the aft bulkhead of the fore platforms is made as the walls. It also is separated from the fore platform to allow room for the uprights of the Bitts.
There is a central gap (without a door).
Door only to aftmost room-access to others via scuttles.
Note also no pillar to #5 lower deck beam.
Stanchions are 2.12 mm square.-some are already located where recesses already made in the platform planking.
(the rabbeting suggested as a possibility will be omitted)
Rooms on the port side looking foreward are Blockroom,Coal hole and Boatswain’s store room.
Middle bulkhead-extends across from side to side. Against and supported by the #4 pillar.
Similarly, the fore bulkhead, has no gap or door.
Finally, a fore/aft wall from this bulkhead the stem. This runs off-center to port to allow for the fore mast.
This is a bit fiddly as it must be cut to allow for the Breast Hooks.
( The Ring Bitt uprights are partially made now to allow fitting of the gap in the planking and shaping of their “feet”. These are 6.9mm square and a generous 11cm long- separated
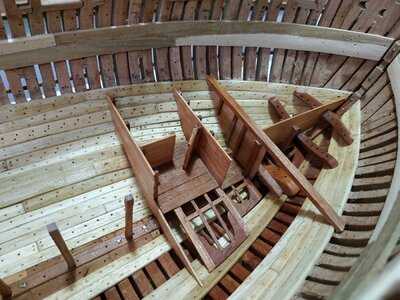
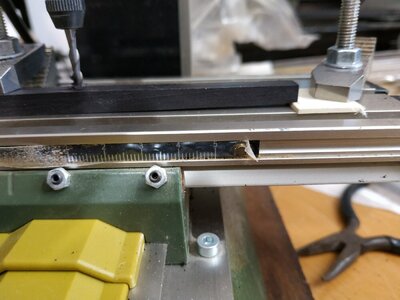