- Joined
- Jun 29, 2024
- Messages
- 1,121
- Points
- 393
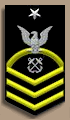
A weakness of all wooden structures that were required to move, like ships, was the need to fasten pieces together to form the whole. Until WW II there was really no glue that was available for use in a marine environment. The famous British Mosquito Bombers were one of the first examples where waterproof glue was used to build a truely monoquique(sp) structure. Shipbuilders in the Clipper Ship era had to resort to mechanical fasteners to join together the thousands of pieces of lumber to build a ship.
The primary stresses in a ship’s hull are longitudinal from flexing of a hull in a seaway; the stresses that cause hogging and sagging. Despite common belief, the vessel’s frames do nothing to resist the loads that cause these stresses. They maintain the hull’s shape, stiffen planking from collisions with docks, and provide a strong member for the mechanical fasteners securing the planking. The caulking between planks can help to resist these longitudinal bending loads. Wooden treenails were surprisingly efficient mechanical fasteners if used correctly. The idea was to make them swell in the hole to make a tight joint.
Once in service, a ship moving through waves would experience cyclical hogging and sagging stresses. These would cause at first microscopic sliding movements between different strakes of planking. Think of sitting on a stack of planks supported by a pair of sawhorses. As the ship aged these movements increased as these stresses damaged caulking and treenails Since these vessels had less buoyancy at the bow and stern, the hull hogged.
The triangle is a shape that is key to resisting this sliding effect between adjacent strakes of planking. That’s why bridge trusses are triangular. That’s also why the triangular pattern of the cris-crossed iron bracing was used to reduce hogging in long hulls.
Your model is not going to be subject to these cyclical bending loads. You also have available effective adhesives to permanently glue strength members together. Your model will, therefore, be more lightly loaded and better able to withstand those loads that do exist than the real ship.
Roger
The primary stresses in a ship’s hull are longitudinal from flexing of a hull in a seaway; the stresses that cause hogging and sagging. Despite common belief, the vessel’s frames do nothing to resist the loads that cause these stresses. They maintain the hull’s shape, stiffen planking from collisions with docks, and provide a strong member for the mechanical fasteners securing the planking. The caulking between planks can help to resist these longitudinal bending loads. Wooden treenails were surprisingly efficient mechanical fasteners if used correctly. The idea was to make them swell in the hole to make a tight joint.
Once in service, a ship moving through waves would experience cyclical hogging and sagging stresses. These would cause at first microscopic sliding movements between different strakes of planking. Think of sitting on a stack of planks supported by a pair of sawhorses. As the ship aged these movements increased as these stresses damaged caulking and treenails Since these vessels had less buoyancy at the bow and stern, the hull hogged.
The triangle is a shape that is key to resisting this sliding effect between adjacent strakes of planking. That’s why bridge trusses are triangular. That’s also why the triangular pattern of the cris-crossed iron bracing was used to reduce hogging in long hulls.
Your model is not going to be subject to these cyclical bending loads. You also have available effective adhesives to permanently glue strength members together. Your model will, therefore, be more lightly loaded and better able to withstand those loads that do exist than the real ship.
Roger
Last edited: