After posting a picture on rounding axles a member had the idea of a thread with little "how-to" items or tricks of the trade that might be of interest for both kit and scratch builders.. Hope this is of interest for one and all to contribute their little tricks.
If this subject has already been started, please let me know, I looked and could not find anything.
First up
Rounding truck axles on cannon carriages. Too many times we are relegated to having axles that are not round. To round them by hand is tedious and not consistent but I came up with a little device some years ago that is simple to make and easy to use .
Take a small piece of brass or aluminum rod and drill a hole in one end that is the diameter that is needed. Typically the width of the trucks is the same as the thickness of carriage brackets and the axle diameter is about the same as well. Once the hole is drilled, make a couple cross cuts with a hack saw which will create cutting edges in the drilled hole.
The axles were not usually square so you will feel the cutter stop when it hits the shoulder which takes a second or less in time. It may take a little cleaning up of peelings. If they are square, a little care needs to be taken not to round too far down. Marking the cutter with ink or tape as an indicator is easy and effective.
Allan
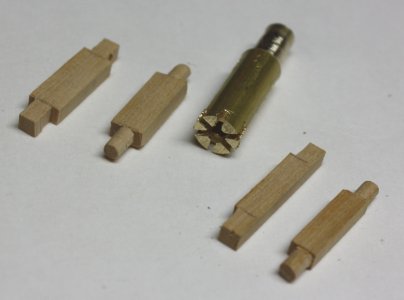
If this subject has already been started, please let me know, I looked and could not find anything.
First up
Rounding truck axles on cannon carriages. Too many times we are relegated to having axles that are not round. To round them by hand is tedious and not consistent but I came up with a little device some years ago that is simple to make and easy to use .
Take a small piece of brass or aluminum rod and drill a hole in one end that is the diameter that is needed. Typically the width of the trucks is the same as the thickness of carriage brackets and the axle diameter is about the same as well. Once the hole is drilled, make a couple cross cuts with a hack saw which will create cutting edges in the drilled hole.
The axles were not usually square so you will feel the cutter stop when it hits the shoulder which takes a second or less in time. It may take a little cleaning up of peelings. If they are square, a little care needs to be taken not to round too far down. Marking the cutter with ink or tape as an indicator is easy and effective.
Allan
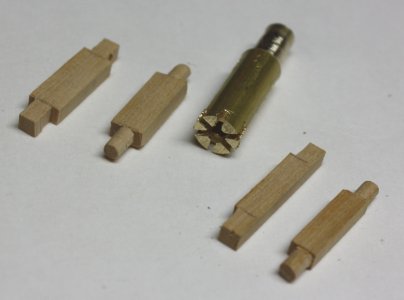
Last edited: