There is this statement about wood "it holds a sharp edge" in general I do not know why this is of any real concern. for engraving or ultra fine carvings like the picture in the Boxwood section yes holding a fine sharp edge is a concern. For general modeling building the focus is the process of building if you use extreme hard wood cutting and joinery is difficult. Softer woods are more "workable" and you can develop skills by first using woods you can actually cut and shape.
with a hard wood cutting this notch would be harder to do with a knife than it would be using something a little softer. you would never be able to push a razor blade into hard wood like you can do with this Basswood.
Cutting a notch for the end of a beam can be done in simple steps using a knife. You can do this in say Boxwood or hard Maple but it will take more effort you will be more likely chipping out the wood or taking light shavings. Softer wood you make the end cuts and then the back cut. Notice the slight rolled edge to the left of the notch, this is what the statement about a sharp edge is all about. BUT keep in mind you are looking very close to the work, you would not even see that rolled edge with the naked eye.
next cut is an angle cut from center to the end
next cut is same as the first just on the other side
for the final cut clamp the beam in a vice and slice off the center piece
The finished cut has edges as sharp and clean as you would ever need. Remember again you are looking really close at the notch holding this in your hand with a naked eye it is perfect. As you get better at it you can cut the notch ever so slightly small so when you fit the end of the beam into the notch the wood will compress slightly and give you a clean tight fit.
this wood is Basswood as you get better at it woods like Cherry, Poplar, pearwood, applewood and a big list of others that are a little harder than Basswood will produce excellent results.
When your told don't use this or that wood because it does not hold a sharp edge consider what you intend on using the wood for.
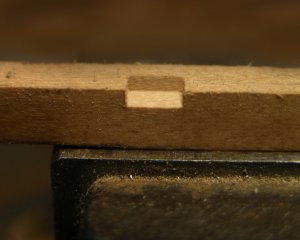