- Joined
- Dec 1, 2016
- Messages
- 6,051
- Points
- 728
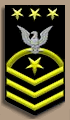
![]() |
As a way to introduce our brass coins to the community, we will raffle off a free coin during the month of August. Follow link ABOVE for instructions for entering. |
![]() |
Dave, I feel your pain. I worked with AutoCAD professionally since Version 12 (not 2012… just 12) and when I started trying 3D modeling with AutoCAD and then Fusion 360 it seemed like a didn’t just spend 30+ years engineering and drafting.![]()
Good luck with this project. I wish you great success. However, now that I’m retired I have no interest in sitting behind a desk drafting. I would much rather be in the shipyard/woodshop tinkering on models or general woodworking. Or maybe skiing… In fact I think I’ll ski today. We still have a week or so left in the season.3D design and printing is the next level in model ship building, in Fusion360 you can design the engine to actually work by using a small air pump. Now this is model engineering. I can imagine an engine room model of the Indiana with a small air pump in the display base. Flip the switch and watch the piston move in a clear printed cylinder, the shaft turn and the prop rotate.
dream on and that makes you sit in front of a computer for hours on end learning a new program. OR do all the 2D cad work and hire someone to design the 3D parts then send you STL file for printing.
Dave , thanks for the generoustyi figured i would try printing cannons i started with the smallest and if i could print it with an Ender filament printer larger sizes would be no problem
here is the result.
View attachment 458344
when you zoom in really close the finer details are distorted and it looks a bit rough
View attachment 458345
looking at a screen shot of the original cad drawing you can see the sharp detailing
View attachment 458346
i uploaded the object file for anyone wanting to test a print and see if they get better results
Dave, I have a Mars 2. If you send me your .stl file. I'll print it. Send me a message in conversations with the file or I'll give you me e-mail. Billi would like to see a resin print from the same file i posted to see the difference.
i checked Ebay and resin printers are indeed around 100$$
is there a resolution factor to consider when buying a resin printer?
Dave - Ok, here it is. Your .stl file was downloaded to my "CHITUBOX" slicer program. The program is the stock Eligoo Mars2 slicer/driver. I added program supports. So, 21mm long. Run time was 1.24 hrs. The long run time was supports and .015mm layers. The slicer layers, drives the resolution. The best camera I have is my phone. Couldn't get rid of the shadow. There are some sprew witness marks that can be cleaned up. The two pics are the same cannon. BillDave, I have a Mars 2. If you send me your .stl file. I'll print it. Send me a message in conversations with the file or I'll give you me e-mail. Bill
i posted the object file in post #50
i assume all printers will take OBJ and STL files