- Joined
- Sep 3, 2021
- Messages
- 5,033
- Points
- 738
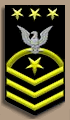
.....These are what my straight timber looks like. Seriously tho : What a brilliant example of authentic period driven modelling should be. Stunning work Maarten. Cheers Grant
Than start a Dutch build, you can do it without additional work.
I (almost) fully agree with Maarten.
Regards, Peter
...almost doesn't count as an option![]()
![]()
![]()
![]()
![]()
….. In no way I did consider building the shell first on my Balder.![]()
.... this is a serious statement and requires proof.![]()
![]()
![]()
So far all talk and no correlated action...
