8/6 to 8/11
I’m back in Vallarta for a week. Not much time for the Molino as we have a LOT to do to our condo because we had a number of renovations completed while we were gone.
The one thing that I expected to have time to do was putting a coat of satin varnish on the decks. I couldn’t do it when I was “supposed” to since I didn’t bring any paint, varnish, or stain with me when I brought the kit down here in May. Included in the handful of tools and supplies I brought down this trip were hopefully all the various paints I need for completing the ship. I’m sure I’ll decide to do something that will require some color I don’t have but I’ll cross that bridge when/if I get there.
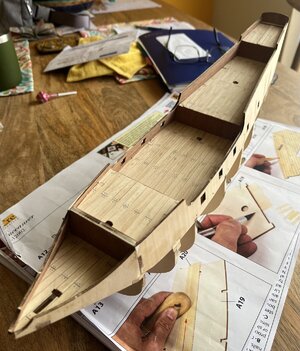
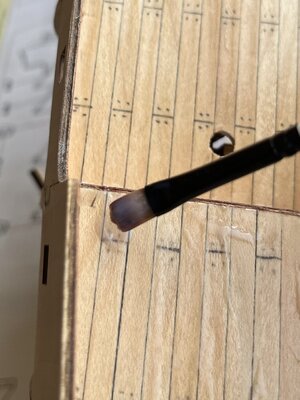
Varnishing the deck was very straightforward except that since the gunwales (I think that’s what to call them) were already in place (because i didn’t want to not work on the Molino until i came back with varnish), I decided to varnish them as well.
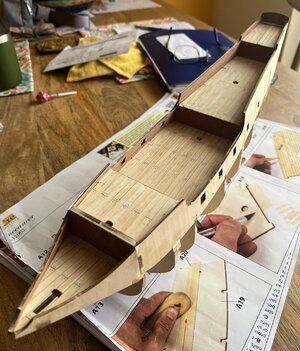
Now a bunch of sanding to fair out the bulkheads. And what better place to sand than on the sands of Banderas Bay, my workshop this week.
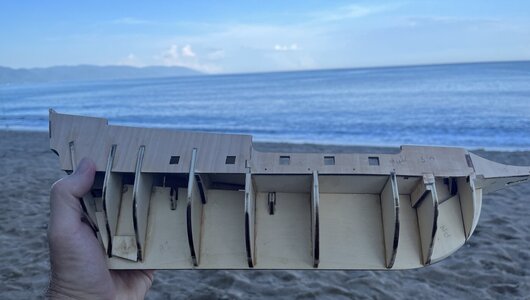
Fairing on the Molino is quite a bit different from what I did on my Bluenose as it has a very sleek profile compared to that of a galleon.

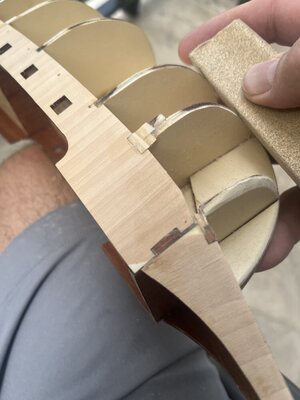
That’s it for this trip.
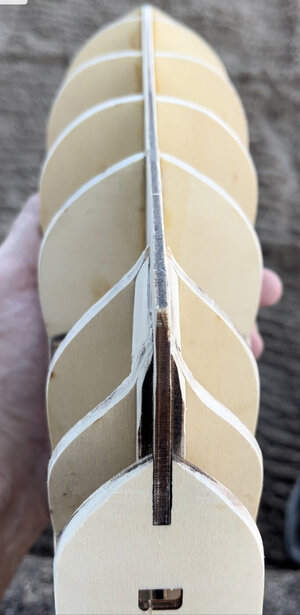
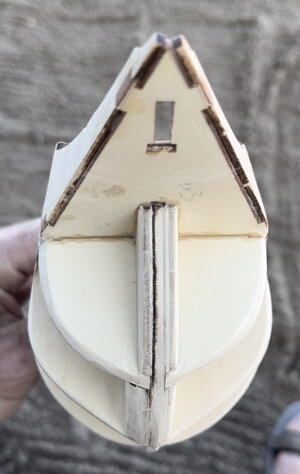
We might try to come down for another short “work” trip in September. Worst case, we’ll be back for a nice 2 month stay starting in early December.
Time for this portion: 4 hours
Total time to date: 33.5 hours
I’m back in Vallarta for a week. Not much time for the Molino as we have a LOT to do to our condo because we had a number of renovations completed while we were gone.
The one thing that I expected to have time to do was putting a coat of satin varnish on the decks. I couldn’t do it when I was “supposed” to since I didn’t bring any paint, varnish, or stain with me when I brought the kit down here in May. Included in the handful of tools and supplies I brought down this trip were hopefully all the various paints I need for completing the ship. I’m sure I’ll decide to do something that will require some color I don’t have but I’ll cross that bridge when/if I get there.
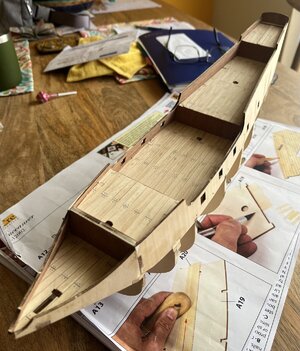
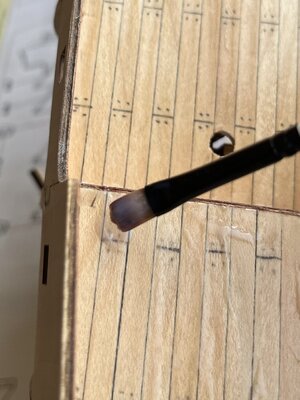
Varnishing the deck was very straightforward except that since the gunwales (I think that’s what to call them) were already in place (because i didn’t want to not work on the Molino until i came back with varnish), I decided to varnish them as well.
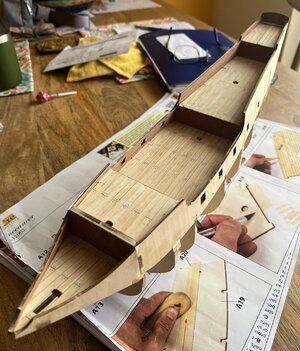
Now a bunch of sanding to fair out the bulkheads. And what better place to sand than on the sands of Banderas Bay, my workshop this week.
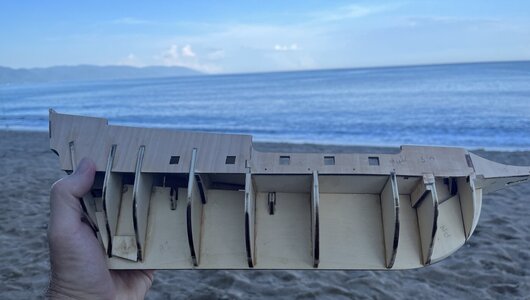
Fairing on the Molino is quite a bit different from what I did on my Bluenose as it has a very sleek profile compared to that of a galleon.

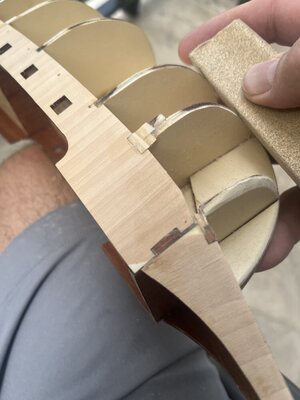
That’s it for this trip.
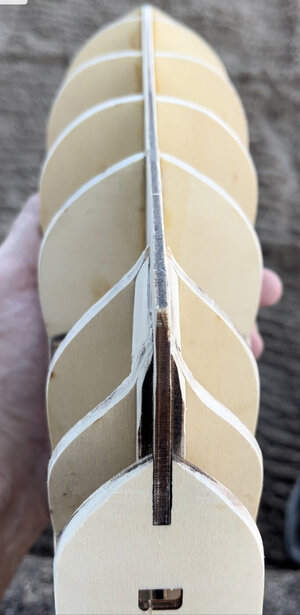
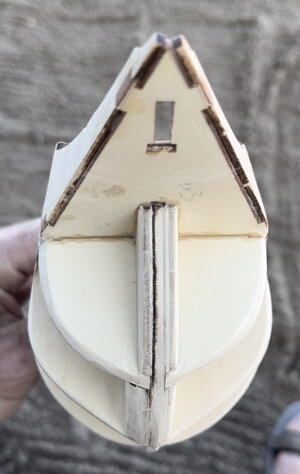
We might try to come down for another short “work” trip in September. Worst case, we’ll be back for a nice 2 month stay starting in early December.
Time for this portion: 4 hours
Total time to date: 33.5 hours
Last edited: