5/13 to 5/16
Small disclaimer… I’m still leaning the parts of a ship so PLEASE let me know if I’m referring to something incorrectly.
I’ve decided to plank the inner walls of the sides of the ship instead of staining them. The boards will be horizontal with vertical supports as I saw in a build log for the Golden Hind. And since the Buccaneer is a fictional ship, I’m not doing the actual ship any dis-service. I’m also renaming her “Molino” or Mill. Not the most glamorous name, but it’s the name of our condominium complex in Vallarta. I’ll research how and where to post it on the ship.
The vertical supports won’t go in until later for a variety of reasons, one of them being I want to varnish them to match the deck and I don’t have the varnish here in Mexico. I glued the planking on the bulkwards in much the same fashion as the deck was made.
In all there are 7 pieces that make up the bulkward walls, 3 along each side plus the piece on the stern. To make sure I don’t cut too much of the planks off (like I did on the decks), I’ll be taking extra time to dry fit each planked bulkward.
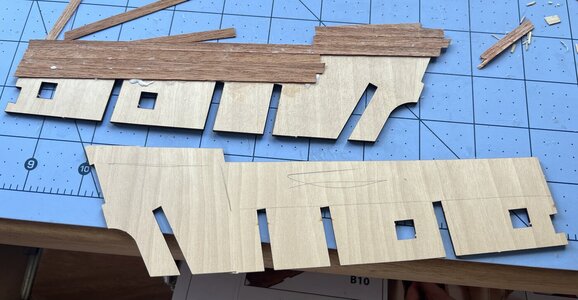
I then trimmed off the excess and sanded the edges smooth.
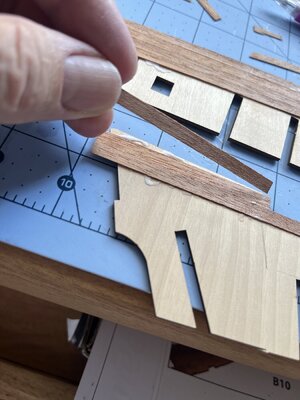
All the time dry fitting the pieces not just against the top of the hull/bulkheads, but also against any adjoining pieces. This step took a lot more time than I expected as each piece has small slots and tabs to align the bulkwards and tops of the bulkheads on the ship - and while they were fairly close to matches, they weren’t exact. Without being “exact”, the tops of the 7 bulkward walls would not match.
The 2 on the bow and thr 2 at midship needed just a little tweaking to get them where I wanted them. The ones on the stern were a different story. Each needed multiple slots opened up and even “deepened” a little bit for them to sit correctly.
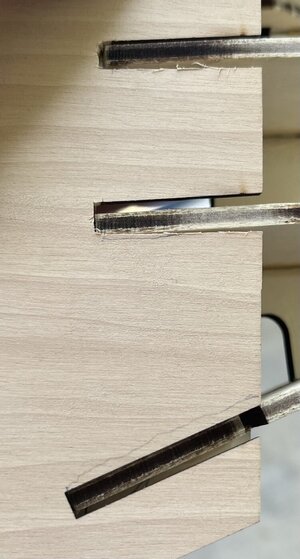
That left the last piece at the bow across the transom/poop deck. First I had to make the slots a little deeper since I added to the thickness of the tabs by planking the bulkwards. That was the east part.
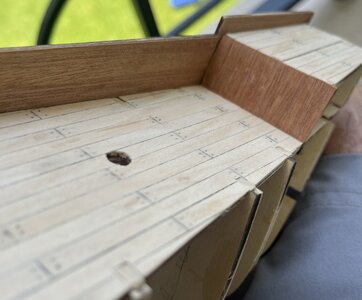
The next part was the transom/poop deck itself. Once I dry fitted these bulkwards, it became apparent that the poop deck was:
- Not level in relation to the quarter deck
- The upper front corners were too wide
To fix the level issue meant widening one of the slots that aligns the poop deck with the bulkhead and adding glue to a number of places and clamping it in place to pull down one side.
The wideness issue required some trimming and sanding to allow the bulkwards to lay down flat against the poop deck.
With all of them ready, I dry fitted all of them again and began glueing, starting with the 3 sections at the stern. In addition to glue, I used rubber bands (I don’t have any clamps big enough here in Mexico) and pins to hold the bulkwards to the bulkheads and frame while the glue set. I haven’t used CA glue on either ship yet, so I was a bit hesitant to start now. I’ll practice at some point in the near future.
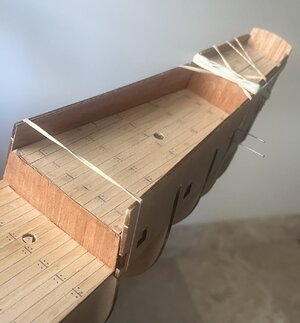
Even with all of the cutting and sanding, there is a small gap between the deck and the bulkward at the stern of the poop deck that I will need to add some boards to fill as well as one side will need a shim added to get it to align with the starboard side.
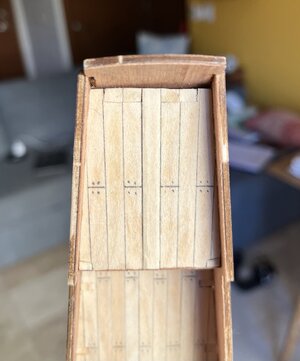
I wanted to add some scuppers to the main deck so I marked where I wanted them and drilled them. Not many (4 on each side) and not too big.
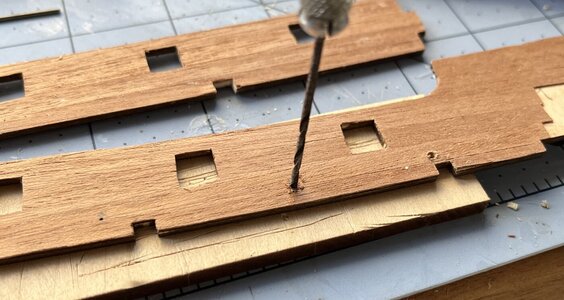
So the 3 sections towards the stern are complete with the 4 from bow to the midship still to be completed. My time in Mexico is waning so I need to use it efficiently to get to a point that I feel comfortable leaving the Molino alone in a closet for around 6 months.
Time for this portion: 7.5 hours
Total time to date: 26 hours