Hi Jim,
You are doing a great job with your Royal Yacht.
I have built a couple of models from Woodyjoe and I have always enjoyed the quality of their kits.
Regarding the quality of the wood, Woodyjoe is generally using 'Hinoki", which is a luxurious Japanese cypress.
Hinoki was used in Japan for its solidity over the time to build temples, but also traditional ships during the Edo period (1600-1868) as the wood doesn't' rot. Some temples like the Horyu-ji in Nara which was built 1200 years ago were made of Hinoki wood.
It is still used these days in Japan as a material for the interior (floor, walls), but also traditional bathtubs, furniture...
Its natural lemon scent is also highly appreciated in Japan for its effects as it can help to relax, release stress, reduce tiredness, and stimulate the mind.
The only problem with Hinoki is the colour, it is very white.
One Japanese modeller I met during a model exhibition ( I live in Osaka) recommended me to use Castor Oil to give a more 'golden colour' to the wood.
I used it on my Higaki Kaisen ship in order to give it a nicer colour close to the real ship and was very happy with the result.
You can have a look at the result on the attached picture.
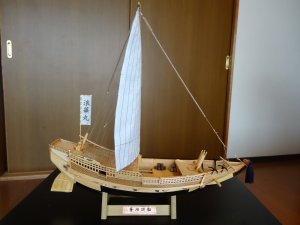
All the best with your build, I will follow it with interest.
Cheers
Marc
You are doing a great job with your Royal Yacht.
I have built a couple of models from Woodyjoe and I have always enjoyed the quality of their kits.
Regarding the quality of the wood, Woodyjoe is generally using 'Hinoki", which is a luxurious Japanese cypress.
Hinoki was used in Japan for its solidity over the time to build temples, but also traditional ships during the Edo period (1600-1868) as the wood doesn't' rot. Some temples like the Horyu-ji in Nara which was built 1200 years ago were made of Hinoki wood.
It is still used these days in Japan as a material for the interior (floor, walls), but also traditional bathtubs, furniture...
Its natural lemon scent is also highly appreciated in Japan for its effects as it can help to relax, release stress, reduce tiredness, and stimulate the mind.
The only problem with Hinoki is the colour, it is very white.
One Japanese modeller I met during a model exhibition ( I live in Osaka) recommended me to use Castor Oil to give a more 'golden colour' to the wood.
I used it on my Higaki Kaisen ship in order to give it a nicer colour close to the real ship and was very happy with the result.
You can have a look at the result on the attached picture.
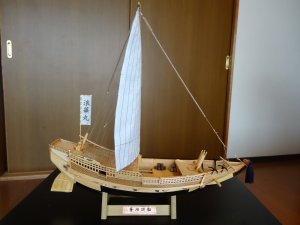
All the best with your build, I will follow it with interest.
Cheers
Marc