moving on to step 2 of building the hull.
At this stage there are a few way you can proceed one is to start planking the hull with a single layer of planks, the issue with this is because the bulkheads are spaced far apart a single layer of planking tends to sit flat between the bulkheads because there is nothing supporting the shape of the hull. Many kits provide a double layer of thinner planking. This works well the first layer gives you the general shape of the hull and by using some sort of wood filler in the low areas the hull is refined to its final shape. A possible disadvantage to the double planking is the planks are half the thickness and the thinner the plank the more straingth is lost and the planks tend to break. A common way of getting the shape of the hull is to fill in between the bulkheads.
Model builders sometimes do not realize a ships hull has frames spaced close together and in some cases almost a solid wall of timbering for the planking to sit against.
With the Sultana model i am going with filling in between the bulkheads. As far as what to use as a filler you can use a dense foam board called sign board this cuts and works very easy. Make sure the glue your using won't melt the foam board and sticks the planks to the foam board. Another issue is the foam board sands very easy and the plywood bulkheads are much harder resulting in a ridge that stick up above the softer foam board.
Another suggestion is making a trip to your local Arts and Craft store or a home improvement store or wood dealer or go on line and get yourself some softer wood like Basswood, Soft Pine, Cedar or Balsa wood.
i am using Basswood i had around the shop and the first thing i did was fill in between the 4 solid square sections.
i did not use a piece to fill in the entire area between the bulkheads i cut the Basswood into a crescent shape that filled in the outer area of the bulkheads leaving the center section of the hull hollow.
another point is to make the filler pieces high enough above the deck line. This is important because a waterway will be placed along the hull and the ends of the deck planking will have a solid area to sit on.
when cutting out the filler block between two bulkheads trace the bulkhead in front when working at the stern and trace the bulkhead behind when filling in the forward section. Looking at this filler piece from the stern it is way beyond the bulkhead
looking at the same filler piece from the bow it is close to the shape of the bulkhead
the next step i shaped the 4 filler pieces close to the bulkheads
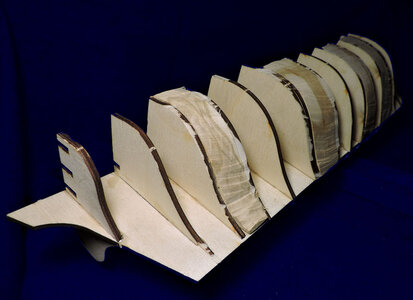
there is no need to use a single block of wood these are just filler and can be made up of smaller scrap pieces or even thinner sheets of wood laminated together.