- Joined
- Dec 1, 2016
- Messages
- 6,049
- Points
- 728
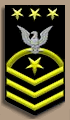
planking the next belt is complete up to the two shutter planks under the main wales
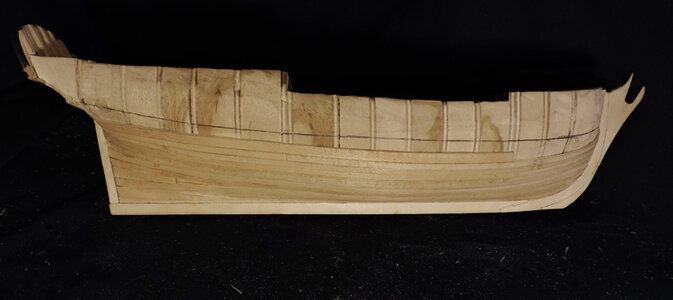
The line is the bottom of the main wale and the shutter planks run parallel to the line. from stem to stern. If the planking was planned correctly you will have room at the bow and stern for the run of the final planks. If you do not have room then something went wrong, either rip off some planks and make corrections or just leave and stop the planks short of the stem, it depends on what you want to do.
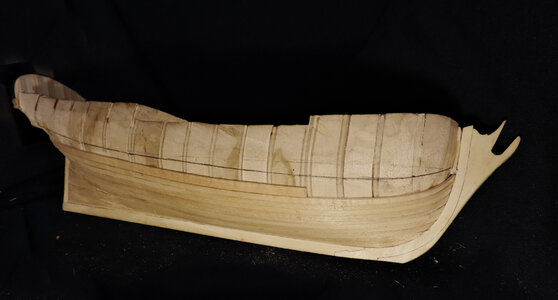
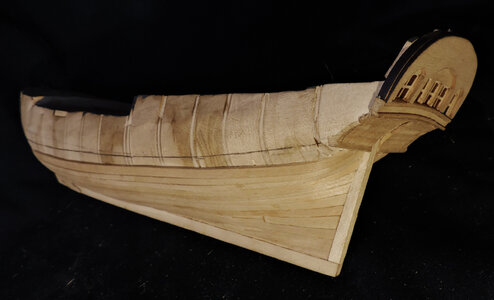
At the stern the final shape of the lower section was left undone up to this point when the last planks are put in place. You can see on the left the final shape and the on the right where the stern has not been finished.
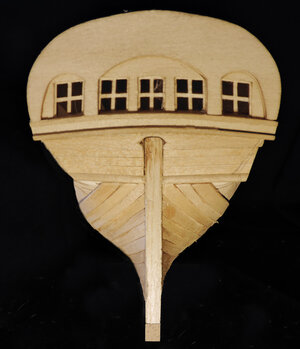
when the last planks are put in i will go over a few points on planking the lower hull before we move on to the upper works.
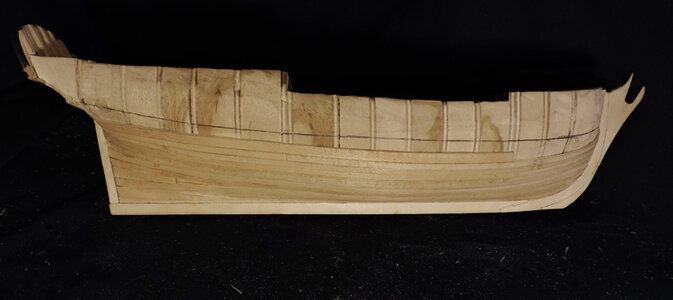
The line is the bottom of the main wale and the shutter planks run parallel to the line. from stem to stern. If the planking was planned correctly you will have room at the bow and stern for the run of the final planks. If you do not have room then something went wrong, either rip off some planks and make corrections or just leave and stop the planks short of the stem, it depends on what you want to do.
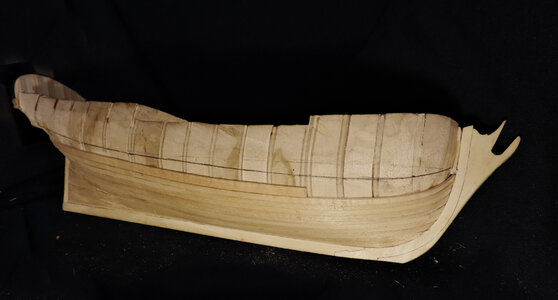
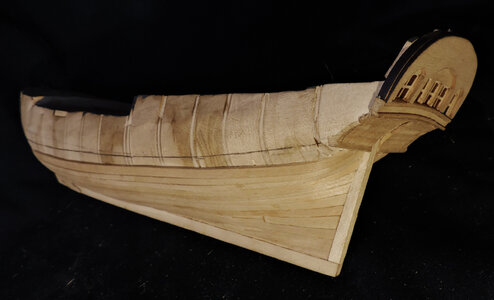
At the stern the final shape of the lower section was left undone up to this point when the last planks are put in place. You can see on the left the final shape and the on the right where the stern has not been finished.
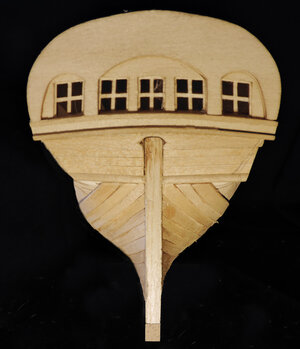
when the last planks are put in i will go over a few points on planking the lower hull before we move on to the upper works.
Last edited: