you may wonder what goes on between postings am i sitting around ignoring the project, or doing yard work and planting our veggie garden, cutting orders, cutting firewood for this winter? well just about all of the above and more.
doing a project like this is a little more complicated because there are no instructions or even a set of plans to follow.
Back in the days when i was working as a graphoc artist it was the policy to never ever delete a previous version of a project. You never know when a client comes in and says "you know what? i like the second version so lets go back to that one" or you made so many changes you can no longer back track.
This is what the Sultans master drawings looks like
in the upper right corner is the original admiralty drawing, below that are the 2 sheet drawings from the Model Expo solid hull kit, the black squares are howard Chapelle's drawings.
looking close more details begin to show up
even down to the windlass parts
each source drawing is traced in CAD
The problems that arise between the 3 drawings for example lets look just at the stern of the Chapelle drawing here all looks OK traced in red to the right is the stern traced from the kit plans
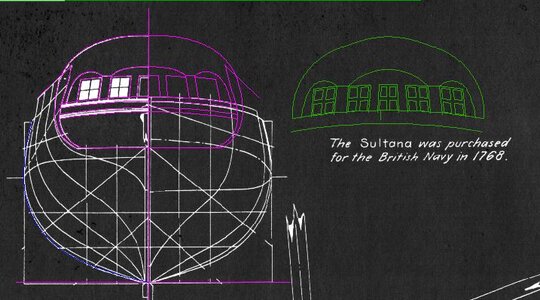
overlay the kit plans on to Chapelle's plans and they are not even close to one another
to see a better image
the red is the chapelle stern and the green is the kit overlay them and they are not even close even though all the original plans have been scaled to 1/4 inch= 1 foot.
what the final results is you end up with a 4th hybred drawing based on the above 3 drawings. Every line, every dimention or moving anything has a chain reaction and affects something else. This is also why you will see multable drawings in the master because you can back track and see what happened or what will happen if you change something.
everyday work is done on the Sultana project.