The biggest concern to scratch buid a windlass is getting a tapered 8 sided barrel with all sides the same. It is much easier than you might suspect.
first start with a 3/8 square piece of stock and glue the pattern on each end. The pattern is drawn in the center of a 3/8 box so if you line up the edges of the drawing to the edge of the wood the sides of the barrel will automatically line up.
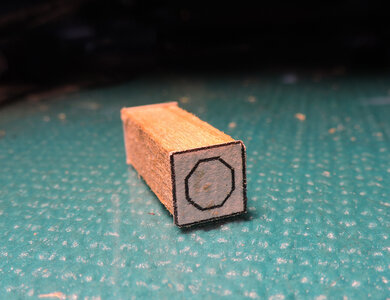
Using a vice the larger end is set flush with the top of the vice and the smaller end is set level with the edge of the drawing. i use a razor blade to set the depth, in the first photo the wood is a little high
just a slight tap to bring it down flush with the vice.
and now you are set to cut the taper
i use a razor blade and cut down the wood, Using Basswood it is soft and cuts nice and clean
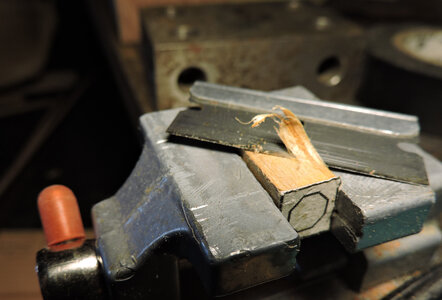
the final cuts i shave the wood at an angle. You can also use a file or sandpaper.
After cutting one side reset the wood and do all 4 sides. At this point you will have a 4 sided tapered barrel
The barrel is 8 sided so there are 4 more sides to cut