- Joined
- Dec 1, 2016
- Messages
- 6,049
- Points
- 728
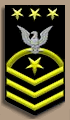
in order the maintain a 90 degree cut on all four sides i made a simple jig. One side is the length of the V shaped top of the timber and the second side is the length of the timber. These timberheads are small and the slightest difference in length will show up.
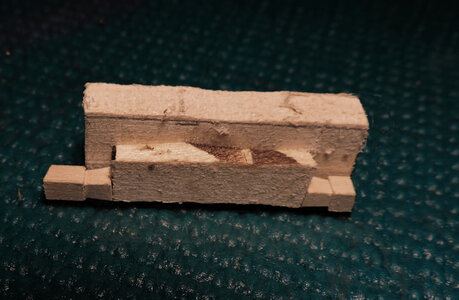
once i have the stop piece glued i added a second side making sure the ends line up.
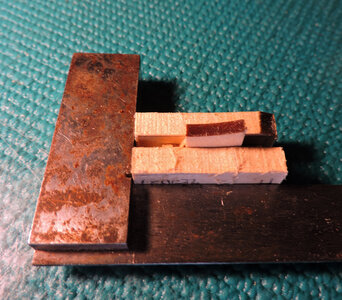
now i have a slot to slide the end of a 1/8 inch piece of wood in on for the V top and one for the length.
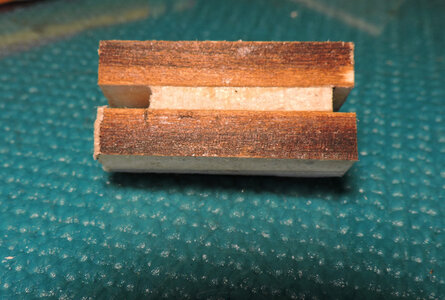
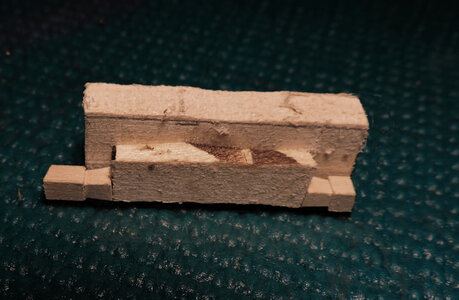
once i have the stop piece glued i added a second side making sure the ends line up.
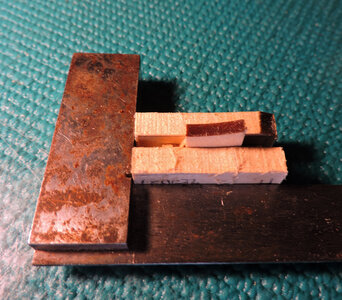
now i have a slot to slide the end of a 1/8 inch piece of wood in on for the V top and one for the length.
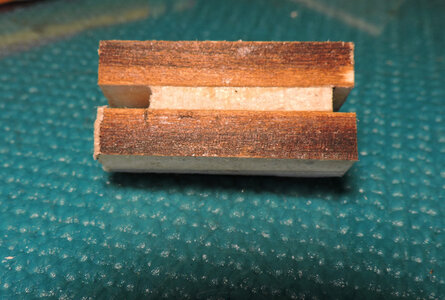