Another update on the mini CNC mill build. The mill itself is made, assembled, and ready to run (photo 1). But I have been waiting, not very patiently, for parts to arrive from USA and China. The hardened steel rods which I was sent originally, were 0.03mm undersized (just over 1 thou for readers who prefer imperial, cubits or acorns), so another batch is due to arrive soon.
Meanwhile, most of the electronic bits arrived, so I have made a start on the control box. The electronic components (photo 2) consist of the box with a lockable transparent lid, a power switch, power transformer, E stop switch, multiple wires not shown, 4 stepper motor drivers, CNC controller board, breakout board, and probably more that I will remember during assembly.
The next photos are various stages to date of assembling the control box. I marked approximately where the various penetrations needed to be cut, then cramped the plastic box to a large angle plate, and milled the penetration shapes with my big CNC mill, on 3 faces of the box. Fortunately for me, the designer of the machine, Stuart Tankard, had done the exacting work of designing and locating the various shaped penetrations.
There are 3 layers of components. The power transformer occupies the lowest, then the aluminium plate sits on the large standoff bolts, then there are 2 layers of electronic PCB's on the alu plate.
Hopefully I will have this all working in another 2 or 3 workshop sessions.
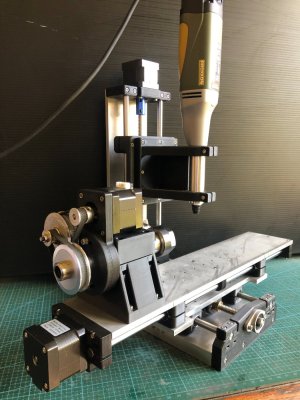
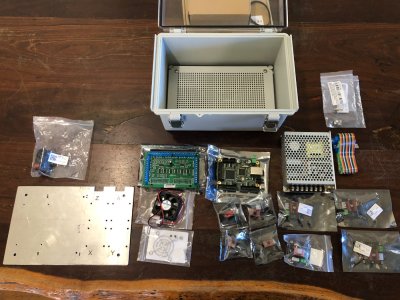
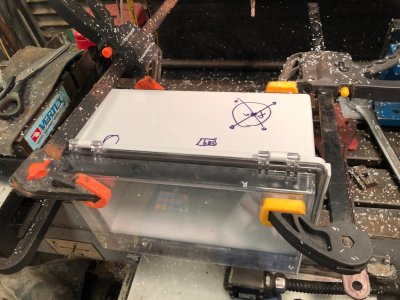
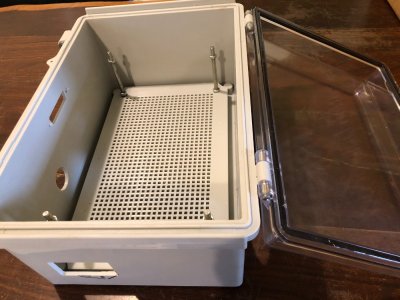
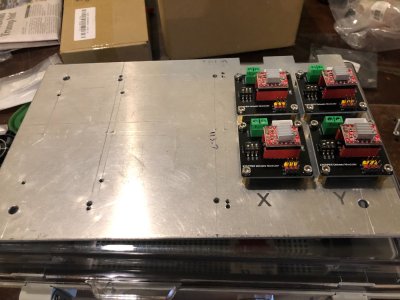
Meanwhile, most of the electronic bits arrived, so I have made a start on the control box. The electronic components (photo 2) consist of the box with a lockable transparent lid, a power switch, power transformer, E stop switch, multiple wires not shown, 4 stepper motor drivers, CNC controller board, breakout board, and probably more that I will remember during assembly.
The next photos are various stages to date of assembling the control box. I marked approximately where the various penetrations needed to be cut, then cramped the plastic box to a large angle plate, and milled the penetration shapes with my big CNC mill, on 3 faces of the box. Fortunately for me, the designer of the machine, Stuart Tankard, had done the exacting work of designing and locating the various shaped penetrations.
There are 3 layers of components. The power transformer occupies the lowest, then the aluminium plate sits on the large standoff bolts, then there are 2 layers of electronic PCB's on the alu plate.
Hopefully I will have this all working in another 2 or 3 workshop sessions.
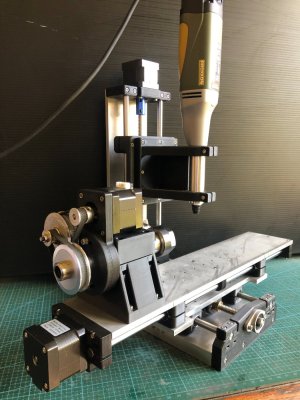
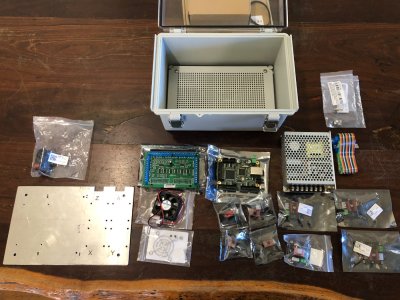
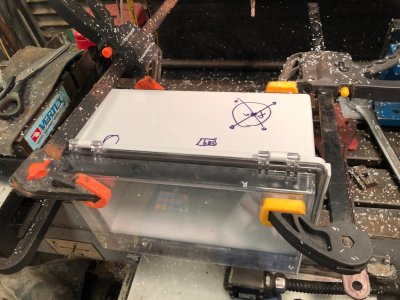
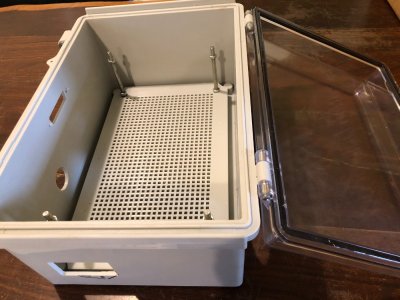
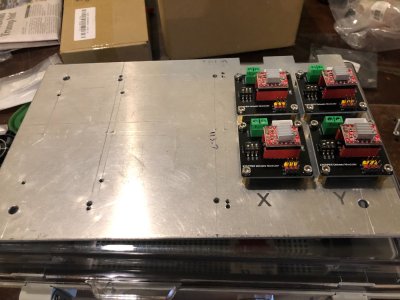