- Joined
- Jun 17, 2021
- Messages
- 3,023
- Points
- 588
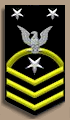
Fastest thumbs up in the west!
Thanks Doc!

Thanks Doc!
![]() |
As a way to introduce our brass coins to the community, we will raffle off a free coin during the month of August. Follow link ABOVE for instructions for entering. |
![]() |
Well done yourself on Harriet Lane!Well done, Pete!
Thank you, my friend!Well done yourself on Harriet Lane!
Well played, Peter!The white metal mast cap for the mizzen mast was missing from the kit. Frankly the ones supplied are pretty crappy, as are the ones available from aftermarket sources. So, I decided to make my own from boxwood. I like it so much better than what was supplied, I may redo the ones from the kit in boxwood as well. I started from scratch milling the piece from a slice of a much-treasured boxwood board. Only the boxwood has sufficient density, with practically 0 graininess to stand up to such fine detail without falling apart. But some judicious work with a slotting blade on the mini circular saw, careful work with the drill press, pinvice and a razor saw and voila! A nice mast cap after a full day's work. Boxwood works slowlyView attachment 500947View attachment 500948View attachment 500949View attachment 500949View attachment 500950View attachment 500951View attachment 500952View attachment 500953View attachment 500954View attachment 500955View attachment 500956View attachment 500957View attachment 500958View attachment 500959View attachment 500960View attachment 500961w by hand and frequent pauses to breathe, re-focus and calm down are required. Trimming the mast with the razor saw. and careful layout, as well as squaring a hole with a square cross section mini rasp were particularly challenging. Despite the time involved, I may do the other caps the same way. I like the one I made so much better than the cast metal ones that came with the kit. Those of you with3-D printers, Cad milling machines, etc., go for it. I have to use whatever I've got, the retro, analog way.
Pete! Love it! Your work with "stone age" tools is always impressive!The white metal mast cap for the mizzen mast was missing from the kit. Frankly the ones supplied are pretty crappy, as are the ones available from aftermarket sources. So, I decided to make my own from boxwood. I like it so much better than what was supplied, I may redo the ones from the kit in boxwood as well. I started from scratch milling the piece from a slice of a much-treasured boxwood board. Only the boxwood has sufficient density, with practically 0 graininess to stand up to such fine detail without falling apart. But some judicious work with a slotting blade on the mini circular saw, careful work with the drill press, pinvice and a razor saw and voila! A nice mast cap after a full day's work. Boxwood works slowlyView attachment 500947View attachment 500948View attachment 500949View attachment 500949View attachment 500950View attachment 500951View attachment 500952View attachment 500953View attachment 500954View attachment 500955View attachment 500956View attachment 500957View attachment 500958View attachment 500959View attachment 500960View attachment 500961w by hand and frequent pauses to breathe, re-focus and calm down are required. Trimming the mast with the razor saw. and careful layout, as well as squaring a hole with a square cross section mini rasp were particularly challenging. Despite the time involved, I may do the other caps the same way. I like the one I made so much better than the cast metal ones that came with the kit. Those of you with3-D printers, Cad milling machines, etc., go for it. I have to use whatever I've got, the retro, analog way.