- Joined
- Oct 23, 2018
- Messages
- 822
- Points
- 403
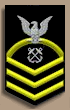
After a lot of preparation works I finally started to glue the keel parts together.
For the treenails I use the same boxwood as for the rest of my build. Without making the wood a little bit wet, the treenails are not really visible. If everything works, this will change after the hull gets his finish with oil or so on.
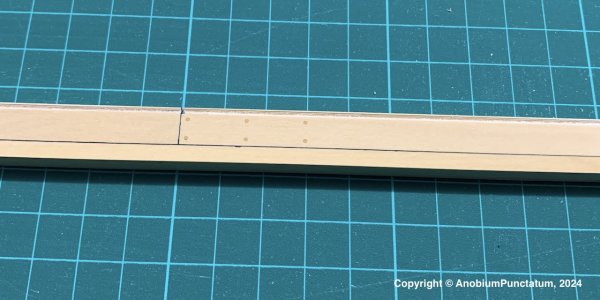
For the caulking I use a black cellulose from a hobby shop. It is really thin.
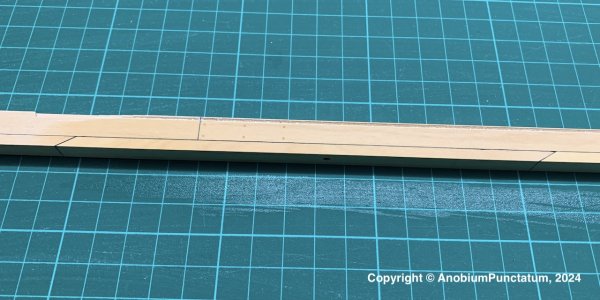
To be able to screw the model to the stand later, I milled three holes in the components.
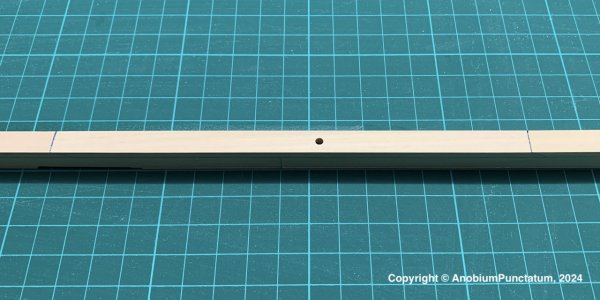
Before I could continue with the construction of the stem, a cut-out had to be milled into the upper stem. I built a small auxiliary construction for this, which was held together with some adhesive tape. This means I can use it again later.
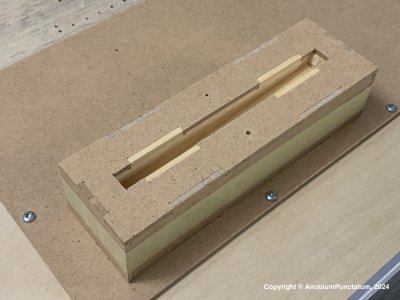
The next photo shows the jig with the component clamped in place before milling.
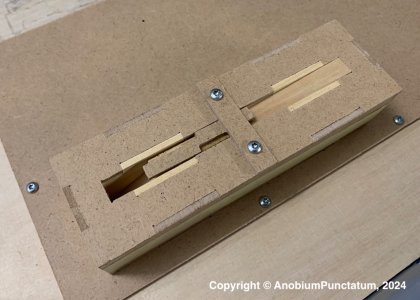
And finally the finished component.
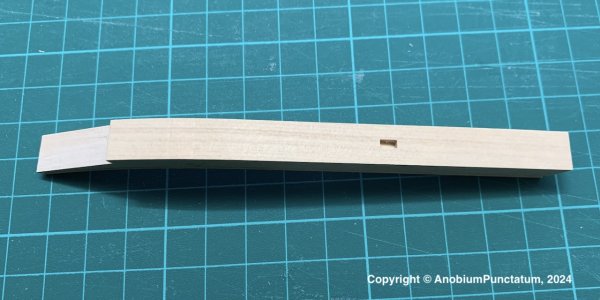
Before glueing the parts of the stem to the keel, I checked the construction in another jig. This is really helpful, because I have very little tolerances with the milled parts.
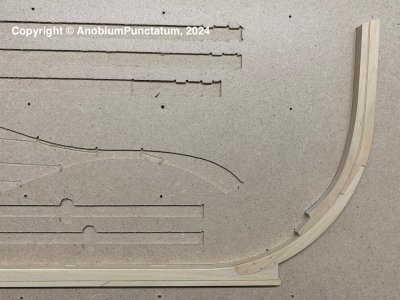
Then I glued all parts of the together. For the calking I used again the black cellulose. To mark the rabbet line between the upper apron and the stem I used brown chalk.

The components were then sanded with 100 and 180 grit sandpaper. At the same time, the taper of the construction was created, 14'' at the upper end of the upper stem 10.5'' at the leading edge of the keel. When the knee of the head is glued on, the front edge of the lower stem is tapered to 10''.
Finally, the rabbet in the area of the upper apron was completed.
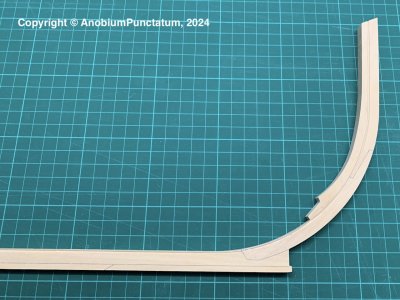
The last to pictures are showing the completed construction in the building jig.
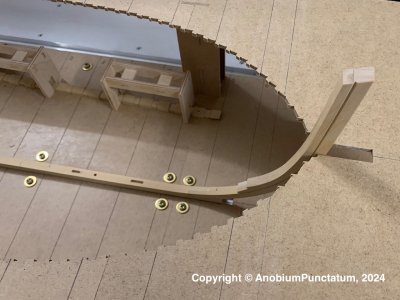
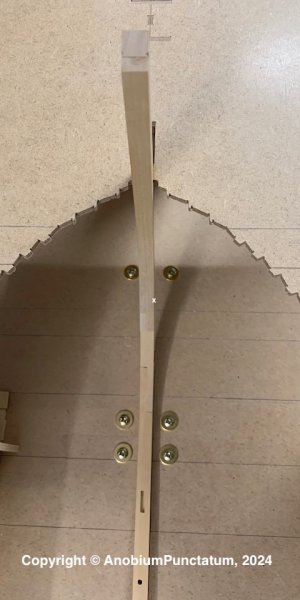
For the treenails I use the same boxwood as for the rest of my build. Without making the wood a little bit wet, the treenails are not really visible. If everything works, this will change after the hull gets his finish with oil or so on.
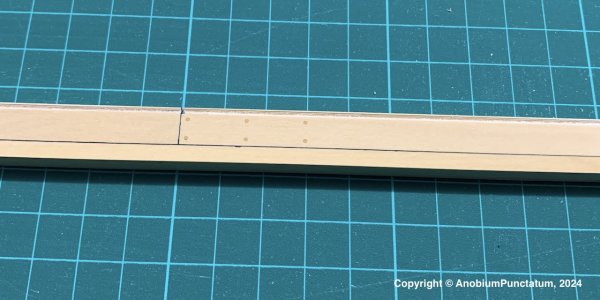
For the caulking I use a black cellulose from a hobby shop. It is really thin.
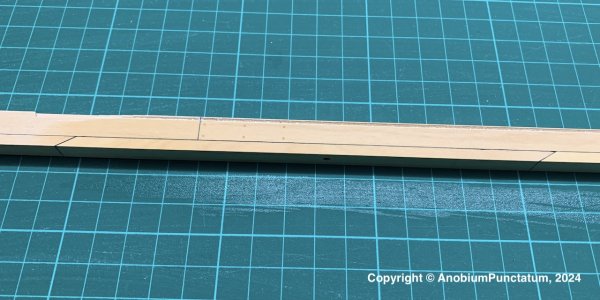
To be able to screw the model to the stand later, I milled three holes in the components.
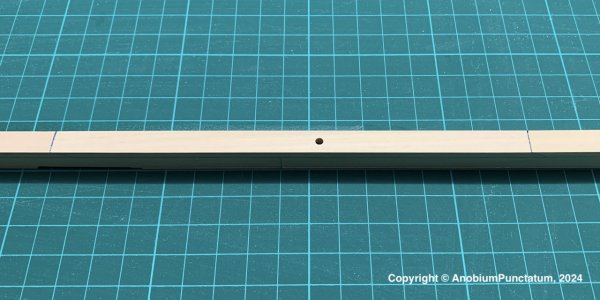
Before I could continue with the construction of the stem, a cut-out had to be milled into the upper stem. I built a small auxiliary construction for this, which was held together with some adhesive tape. This means I can use it again later.
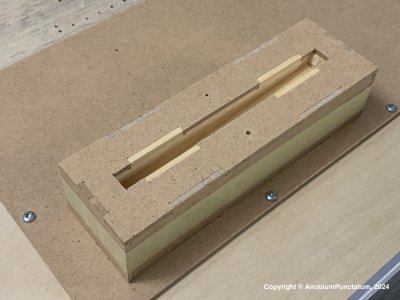
The next photo shows the jig with the component clamped in place before milling.
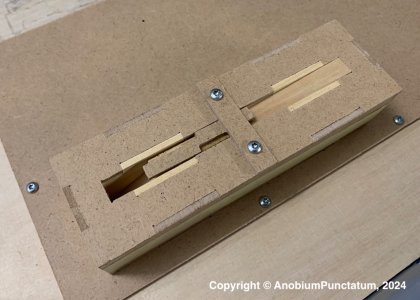
And finally the finished component.
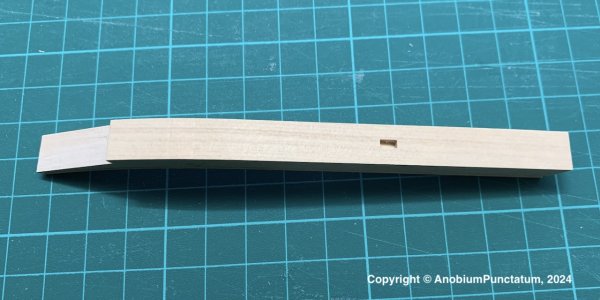
Before glueing the parts of the stem to the keel, I checked the construction in another jig. This is really helpful, because I have very little tolerances with the milled parts.
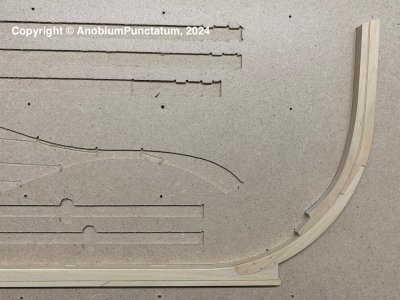
Then I glued all parts of the together. For the calking I used again the black cellulose. To mark the rabbet line between the upper apron and the stem I used brown chalk.

The components were then sanded with 100 and 180 grit sandpaper. At the same time, the taper of the construction was created, 14'' at the upper end of the upper stem 10.5'' at the leading edge of the keel. When the knee of the head is glued on, the front edge of the lower stem is tapered to 10''.
Finally, the rabbet in the area of the upper apron was completed.
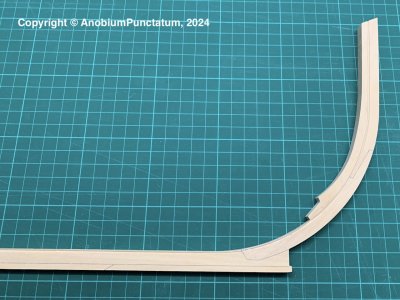
The last to pictures are showing the completed construction in the building jig.
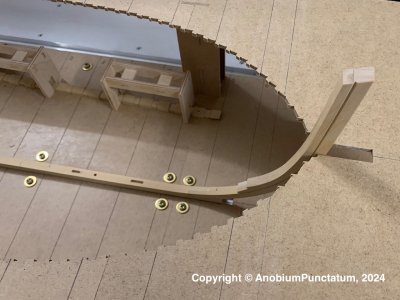
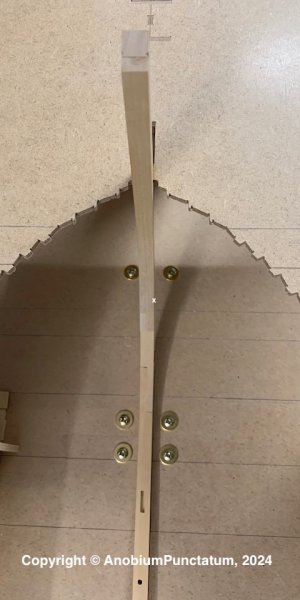