In 2015, Lauck Street Shipyard, owned by Bob Hunt, produced about 40 kits of an Armed Virginia Sloop plank-on-frame model. Bearing the fictional name Patrick Henry, this unique and amazing 1:32 scale model is quite rare in the community. I am the proud owner of Kit #002 and was one of Bob's students for many years along with several other members of SoS. I spent about 360 hours building this kit and an happy to share my 2015 log with you here. I will try to answer specific questions if I can but please remember it has been 5 years since I built the model. To my knowledge, mine was the first production kit to be completely built. DocBlake, another SoS member also has completed the Patrick Henry. His is absolutely stunning and modified with additional details not included in the kit. You can see Doc's Patrick Henry here on SoS as well. I'm sure he will be happy to help answer build questions too. So let's get to it.
This kit comes with quality materials and excellent packaging. Offered in a variety of hardwoods, I choose the Redgum and Cherry option. I really like the way all the strip wood is organized by build topic versus type/size. This will make the build go much easier. There are 11 sheets of CNC cut parts, 22 individually labeled packages of strip wood, and a box of excellent 3D printed parts. To my knowledge, this might be the first kit to include 3D printed parts. There is also a special building jig and a display base. The CD's are packed full of documentation and build photos. 5 sheets of full sized plans and parts identifiers rounds out a box that weighs in at over 17 pounds. Here are a few pics:
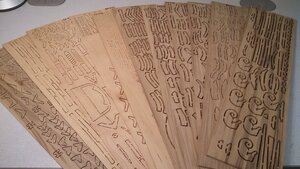
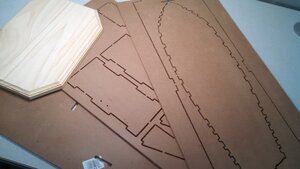
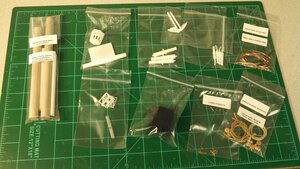
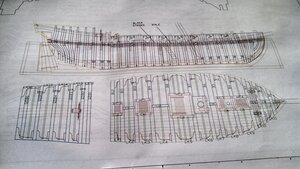
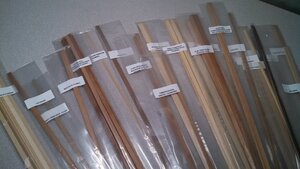
This kit comes with quality materials and excellent packaging. Offered in a variety of hardwoods, I choose the Redgum and Cherry option. I really like the way all the strip wood is organized by build topic versus type/size. This will make the build go much easier. There are 11 sheets of CNC cut parts, 22 individually labeled packages of strip wood, and a box of excellent 3D printed parts. To my knowledge, this might be the first kit to include 3D printed parts. There is also a special building jig and a display base. The CD's are packed full of documentation and build photos. 5 sheets of full sized plans and parts identifiers rounds out a box that weighs in at over 17 pounds. Here are a few pics:
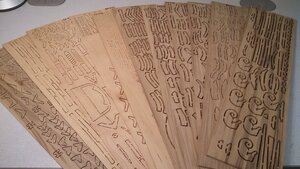
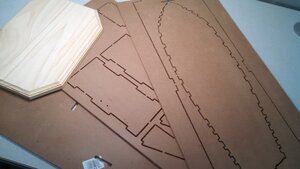
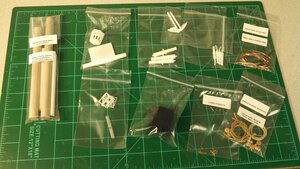
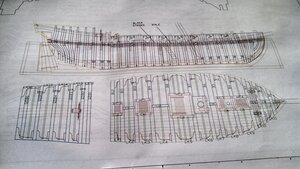
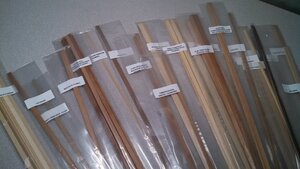