LOG CONTINUES FROM 2015
The bow hawse frames is probably the most difficult task for the whole model. My next several posts will describe the detailed process I used for shaping the hawse frames. Keep in mind, the photos will be of the left/port side. Let's start by cutting out the template for Hawse 1 and rubber cementing it to the inside/outer edge of the frame. Then, fit the frame into place on the step in the stem and slide it downward until it comes into contact with Frame 11. Make sure the frame stays square with the keel/stem. Read the captions that go along with the next several photos.
Remove material with your dremel where the orange arrow points in order to close the gap at the blue arrow
Remove a little wood at a time until the gap at the blue arrow is gone. You should be just about exactly where the reference mark on the template drawing falls
With the hawse frame in-place, use your pencil to mark the inside edge along the inner length and at the foot (see arrows)
These lines will define the inside bevel for the frame. The point at the blue arrow will be the inside bottom corner between the keel and Frame 11.
At the top of the hawse frame, mark a diagonal line from the outer edge of the template to the corner that rests in the stem-step. Mark a second line parallel to the first beginning at the inner edge/corner of the template. These two lines should be about 3/16" apart.
Now, mark a line that runs along the outside of the frame along the stem and at the foot as shown.
The combination of the paper template and the drawn lines will help you see exactly where the wood needs to be removed to obtain the desired shape. Note: It's the unshaded ares in these photos that get carved away. Now that we have that understanding, we can begin removing wood.
To begin shaping the hawse frame, I chose to start at the top as it's easier to visualize. The first objective is to shape the upper 1" of the frame so that the temporary battens will lie properly. Use your drawn reference lines as the guide - you might be surprised at how accurate they are.
Start with your #22 and carve away some of the more obvious excess wood. I usually focus on slicing away some of the corner edge.
Use your dremel to sand the frame right down to the reference lines. Do this for both sides.
Place the hawse frame back into position and you will see that the temporary battens lie very nice against the area we just shaped
Now that we have the top of the frame shaped, we will move on to carve out the inner surface. You want to shape based on the plane defined by your drawn lines and the paper template. Ultimately, this plane needs to be flat width-wise but curved to follow the inner shape of the keel/bow/stem length-wise. See the photos and descriptions below for more info:
Start by using your #22 to trim away the excess wood down the length of the frame's inner surface
Use your dremel to finalize the shaping right down to the drawn reference line and the edge of the paper template. Use the drawing on the end of the frame as your guide to determine the proper angle
Fit the frame back into place and you can see how nicely the inner shape flows. It's only roughed in here and will be cleaned up later with a solid mini-sander (do not use a soft sanding stick). Now all we have left to do is the outer surface
The outer side of the hawse frame is shaped exactly the same way using the edge of the paper template and the line we drew as a guide. Carve away some of the excess wood with your #22 and then do the final shaping with your dremel tool. Once the shaping is done you can see how nicely the hawse frame fits into its location and how its shape flows into the general outline of the ship. Keep in mind the rabbet has not yet been cut in this photo.
The second and third hawse frames are shaped using the same method as the first. Although no paper template is provided for the third hawse frame you should have no trouble determining where to draw the lines for its shaping once you have experience for the first two.
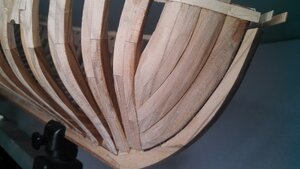