KEEL
The keel structure is glued and drying under a glass pane. It fits the lines in the plan exactly. However, you will notice that there are several gaps, most notably between the stern post and rising deadwood. The gaps are superficial, only on one side- the joint below is square and tight. The laser did not cut all the way through several keel pieces contained in sheet # 09-box 1, so I had to "sculpt" the pieces out resulting in the edges not being perfectly square. The keel pieces out of sheets #8 and # 10 were all well cut by the laser. I will fill the superficial gaps with wood putty after the keel is completely dry and has spent at least 24 hrs under weighted glass.
FRAMES
Started frame construction. Initially, I cut out the plan drawing for each frame and glued it to flat pasteboard with UHU glue. Then I glued parts "A" and "C" to the plan with UHU glue, checking for alignment by looking from different angles. I placed some pins to keep parts for moving, but this is not really necessary...
After looking at UWE's build and the discussion of when to clean up laser char, when to bevel etc., I tried a slightly different several method on each of the three frames I made today.
Frame # 5: Lightly sanded the laser char from the back of the sheet, and cleaned parting ridges. I did not sand any notches or make bevels. This will need to be done later
Frame # 4: Light laser char sanding of the inboard aspect of the frame futtocks, no beveling, using spindle sander, before assembly
Frame # 6: Light laser char sanding of inboard aspect of futtocks, no beveling. Hand sanding of the notches on the exterior aspect off the futtocks, before assembly.
I think that for the rest of the frames I will:
1) Lightly sand the inboard side of the futtocks and centerpiece, making the laser cut 90 degrees. This gets rid of the error introduced when futtock "A" or the center piece are glued to the plan. As we all know, the laser cut is not perfectly perpendicular to the table but has a very tiny angle, making the bottom of the piece a tiny bit broader than the top. By sanding the laser char and angle off, this error is eliminated.
2) Hand sand each exterior notch in each frame, for the same reason as above. Also, I think it is a lot easier to sand the notches flat and clear of laser before assembly than once the frame is assembled.
I got some very small Corradi files, pictured below, that are ideal for this....Thanks to UWE for his recommendation of these superb files!
3) Beveling should be done on a fully assembled frame. The bevel angles and size of the pieces are such that the bevels would not match up well (IMO).
4) I placed a scrap piece of wood, of the same thickness as the frame, underneath futtock "B" to keep the frames straight while the heavy plate glass is on them.
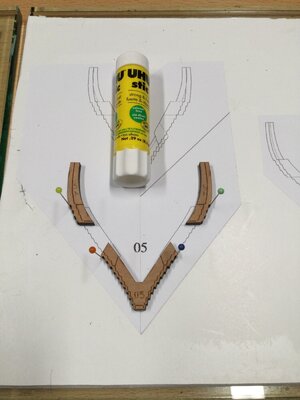
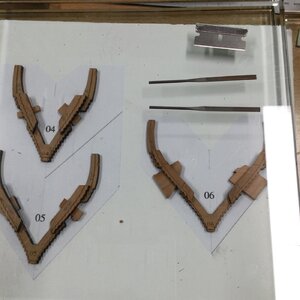