All hands on deck! We are ready for the third and final saga of making the ringbolts. In the past chapter (yesterday), we made eyebolts and rings and today we will assemble using soldering torch and silver solder.
en.wikipedia.org
From Wikipedia:
Soldering is a process in which two or more items are joined together by melting and putting a filler metal (solder) into the joint, the filler metal having a lower melting point than the adjoining metal. Unlike welding, soldering does not involve melting the workpieces. In brazing, the workpiece metal also does not melt, but the filler metal is one that melts at a higher temperature than in soldering. In the past, nearly all solders contained
lead, but environmental and health concerns have increasingly dictated the use of lead-free alloys for electronics and plumbing purposes.
Fanny that the above article didn't mention jewelry manufacturing, only electronics, and plumbing. Before we will get to the actual soldering process, a word of caution:
Make sure you fully understand you will deal with an open flame. Please remove all parts from the table which may accidentally cause a fire.
For the most part, a good understanding of the various temperature of the torch flame is the key. Take a look at my sketch #2: Flame has multiple 'hot points' the large (outer) and the inner (cone). We will use the inner flame specifically the sharpest point of the cone as it has the hottest temperature.
Knowing the melting point of the solder and the way you will flow it - called The Art of Soldering
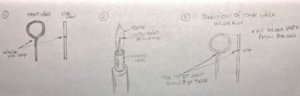
Let's talk about the tools we will need: a butane torch, there are many on the market and plenty to choose from. The silver solder paste. Few words about solder: it comes as 'easy', 'medium', and 'hard'. Jewelers use all 3 as often times it requires to solder 3 different parts in a very small place. So the first part will be soldered with 'hard' as it will require high temperature to melt. The second part will be soldered with the 'medium' because it will require less temperature to melt as hard, and will not destroy the first part. The third will be soldered with 'easy', it will require less temperature than both 'hard' and 'medium'. For those types of solders, we use flux. It helps the solder to flow. Also, there is a soldering paste, it is premixed solder and flux together, a brilliant staff. It also comes as 'hard', 'medium' and 'easy'. We will be using 'easy' for our exercise.
Let's solder the eyebolt first. We'll need this part soldered before the ring assembly. I use the 'Thirdhand' tool to hold the part in a tweezer.
put flame away from the main eye (ring), only on joint
concentrate only on a gap - this is what needs to solder.
Remember the solder will flow only where the hottest temperature will be!
Use as little solder as you can. The smallest the gap the less solder you will require.
Move the torch to control the temperature. Once you see solder melting put the torches 'cone' flame in the gap, kinda telling the solder 'go there'!
Some photos of the soldered eyebolt in Macro. I guess, they get better. What do you think?
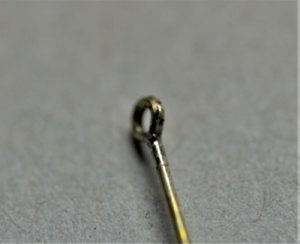
Now we are ready to solder the ring. But first, we need to assemble. The same absolutely process as for the steel. I just realized that I have not photocopied this process for the steel part. I have to fix this mistake and present images of this process.
Now, we are ready to solder the ring. I have a bad and a piece of good news: what news should I start with? Alright, the bad news is.... somehow I lost recorded video process of soldering a ring. But the good news, I made a new video recording today. Many thanks for my Admiral Irina. This video showing the entire process of soldering both parts. All bullet points are the same as for the first soldering.
make sure to close the ring as tight, as possible (minimize joint gap)
use as little solder paste as you can, you will need an only a tiny bit
put the solder paste behind the rings joint, Why? Exactly...you are correct...when we will heat the joint, melted solder will flow where the hottest temperature will be front of the joint, it will only feel the gap, make it nice and clean
Use the 'cone' flame and control the temperature. Heat only the joint.

Take a look at the entire process. I hope it shows the key points.
Some macro images.
Pretty cool, right?

It is not that difficult! The next step is to clean all the oxidized parts and prepare to blacken. First, I cut the desired size. As Janos
@janos, I use a vinegar bath for about 30 minutes. Then, clean with water and use the 'Brass black' solution to make it look like a stele. This is how the ringbolts look after the bath.
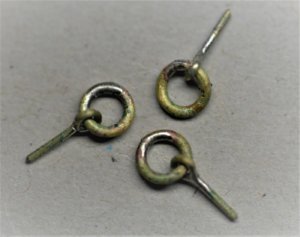
Now it is 'Black Brass' bath. The concentration (how much to dilute with water) you have to experiment. I do 50/50 and it is still debatable. What works for one doesn't work for another. Another dilemma is how much time you should give for a bath? I have no definite answer. I use a few minutes, and then put them in cold water. Maybe that is why I have poor results? Your input will be beneficial.
After water evaporates, the final stage is to make brass ringbolts looks like steel. I have a polishing wheel made of felt, I rub lightly until the best result archived. The results deserve a full view and my Macro shooting - applaud
To complete this tutorial, I installed those rings on Pearwood just to show how they looking. On the right, is ringbolts made from steel, on the left made from brass wire. You are the judge. What do you like most?
bonus photo: ringbolt on the Costello boxwood
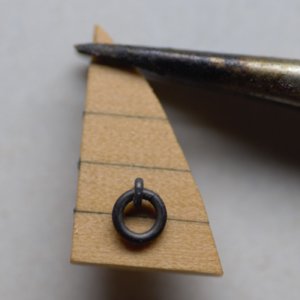
...and with this, the tutorial comes to the end. I really hope this will helps you with your modeling. Thank you All for your support and attention.
Happy Modeling!