Continuing along with the bulkheads:
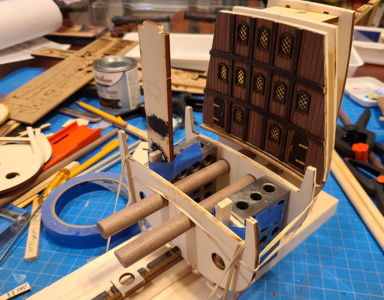
What I've been doing is to square and glue the foremost bulkhead, while inserting the alignment dowels and placing a bulkhead 2 or more positions behind it. The idea is to be sure consecutive bulkheads are properly in place to eventually allow free movement of the dowels into the assembly.
Here I've started using a little force to keep the aftmost bulkhead from raising. This is wrong, as I'll find out later.
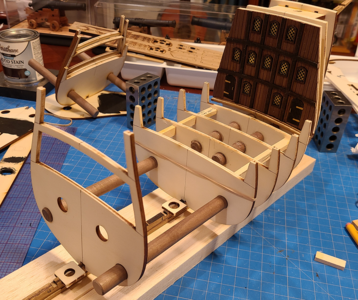
I got this far before I realized I really had a problem:
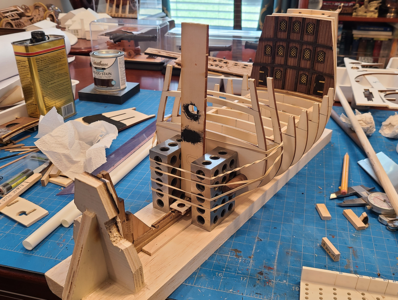
You will notice in the above picture that a band of racoons have decided to chew holes in the back brace of my "ship support". I was mad, at first, but it turned out that the holes line up fine with the rear dowels, allowing them to be inserted or removed while the frame is in the support, so I forgive them.
The problem: Without extreme care, it's easy for bulkheads after the first one to raise up very slightly. A little too much glue, not quite pushing the bulkhead down hard enough, maybe the fit isn't quite loose enough. This goes unnoticed, while you put in all the bulkheads using the foremost dowels and then several with the middle dowels. But in my case, this was raising up a little at a time without being noticed. Until I realized that there was no way the next couple bulkheads were going to slide over the dowels and still properly engage the keel. I went to bed that night resolved to bending the keel in order to make it all fit.
I woke up with a better idea: Tear all the bulkheads except for the ones that engaged the first dowel out, and do them again. Sure enough, I found glue in the bottom of most bulkheads notches where they meet the keel, indicating that I hadn't gotten them down far enough. It's easy to do: the dowels fit and everything looks good and is square, but it's rising up a little at a time.
Really, the best way to assemble this hull would be to assemble it all, all bulkheads, all dowels and keel, make sure it fits, then glue it in place. But that's difficult to do (your hands and those of at least one band of racoons are needed at the same time), and I was afraid that I'd be unable to properly glue the bulkheads to the keel without use of super glue rather than white glue, and didn't think I'd get the strength. The alternative is to build it a bulkhead at a time, but this requires extreme caution. Which maybe all other builders here already have, and it's just that I was lacking. I was also installing braces between the bulkheads to try to keep them square, and think this took my mind off of what was important.
I should mention that my problems and concerns in this area have nothing to do with the accuracy of the bulkhead and keel cuts: they are precise and excellent. In fact it is that precision that creates a problem if you're trying to assemble it improperly.
I used the traditional water method to remove all the bulkheads I could to get back to where my problem started, and made sure that the dowels maintained a nice slide fit through the holes, and yet the bulkheads were all completely down and in position on the keel. It's working much better:
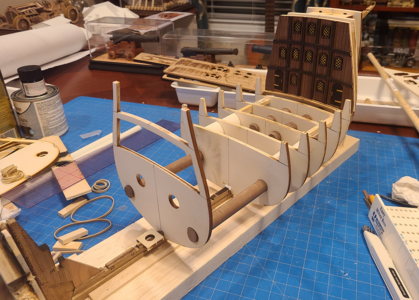
In summary, it is most important with this kit that the frame bulkheads , dowels and keel fit completely in place, which can be tricky to do at one time or maintain a little at a time. We tend to concentrate on all the bulkheads being square and vertical, but in fact that matters much less than the frame alignment does.
Also, don't glue the finished bulkhead 17 in place like I did until later on. I glued it now because I thought Olha did in her video, but in fact she just fitted it in place, adding it later. With all the filling and sanding and such that will take place soon, the chances of getting that finished area damaged, or at least really covered in dust, is high, so don't copy me here. I tried to remove it, but too much glue, so intend to cover it for protection during some of the later operations.
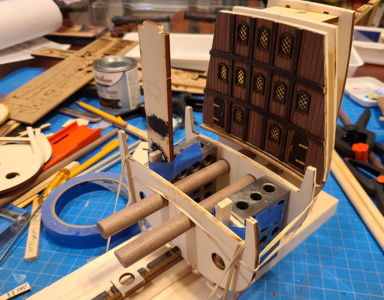
What I've been doing is to square and glue the foremost bulkhead, while inserting the alignment dowels and placing a bulkhead 2 or more positions behind it. The idea is to be sure consecutive bulkheads are properly in place to eventually allow free movement of the dowels into the assembly.
Here I've started using a little force to keep the aftmost bulkhead from raising. This is wrong, as I'll find out later.
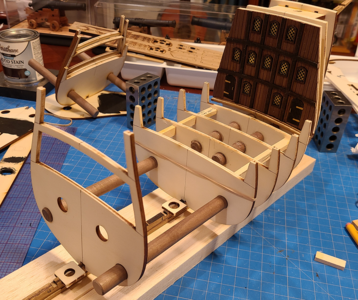
I got this far before I realized I really had a problem:
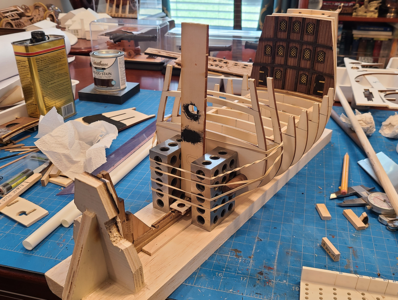
You will notice in the above picture that a band of racoons have decided to chew holes in the back brace of my "ship support". I was mad, at first, but it turned out that the holes line up fine with the rear dowels, allowing them to be inserted or removed while the frame is in the support, so I forgive them.

The problem: Without extreme care, it's easy for bulkheads after the first one to raise up very slightly. A little too much glue, not quite pushing the bulkhead down hard enough, maybe the fit isn't quite loose enough. This goes unnoticed, while you put in all the bulkheads using the foremost dowels and then several with the middle dowels. But in my case, this was raising up a little at a time without being noticed. Until I realized that there was no way the next couple bulkheads were going to slide over the dowels and still properly engage the keel. I went to bed that night resolved to bending the keel in order to make it all fit.
I woke up with a better idea: Tear all the bulkheads except for the ones that engaged the first dowel out, and do them again. Sure enough, I found glue in the bottom of most bulkheads notches where they meet the keel, indicating that I hadn't gotten them down far enough. It's easy to do: the dowels fit and everything looks good and is square, but it's rising up a little at a time.
Really, the best way to assemble this hull would be to assemble it all, all bulkheads, all dowels and keel, make sure it fits, then glue it in place. But that's difficult to do (your hands and those of at least one band of racoons are needed at the same time), and I was afraid that I'd be unable to properly glue the bulkheads to the keel without use of super glue rather than white glue, and didn't think I'd get the strength. The alternative is to build it a bulkhead at a time, but this requires extreme caution. Which maybe all other builders here already have, and it's just that I was lacking. I was also installing braces between the bulkheads to try to keep them square, and think this took my mind off of what was important.
I should mention that my problems and concerns in this area have nothing to do with the accuracy of the bulkhead and keel cuts: they are precise and excellent. In fact it is that precision that creates a problem if you're trying to assemble it improperly.
I used the traditional water method to remove all the bulkheads I could to get back to where my problem started, and made sure that the dowels maintained a nice slide fit through the holes, and yet the bulkheads were all completely down and in position on the keel. It's working much better:
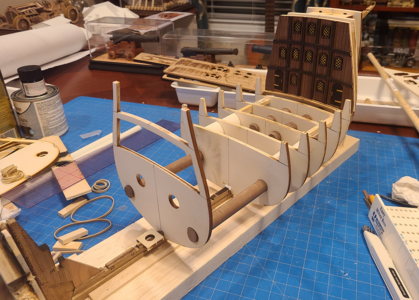
In summary, it is most important with this kit that the frame bulkheads , dowels and keel fit completely in place, which can be tricky to do at one time or maintain a little at a time. We tend to concentrate on all the bulkheads being square and vertical, but in fact that matters much less than the frame alignment does.
Also, don't glue the finished bulkhead 17 in place like I did until later on. I glued it now because I thought Olha did in her video, but in fact she just fitted it in place, adding it later. With all the filling and sanding and such that will take place soon, the chances of getting that finished area damaged, or at least really covered in dust, is high, so don't copy me here. I tried to remove it, but too much glue, so intend to cover it for protection during some of the later operations.