Below the translation of an article about the history of the Kolibri in Israel.
With permission of the author Avinoam Myasnikov and the much appreciated help of
@shota70.
The article was originally posted on
http://www.sky-high.co.il/
"Kolibri 4X-BEA
Story by: Avinoam Myasnikov
September 25, 2021
Article translated from Hebrew with Google translate by Johan Swart
Article originally published on
https://sky-high.co.il/
Helicopter details:
Model: H-3 Kolibri
Manufacturer: NHI (Nederlandse Helikopter Industrie). Assembled by Aviolanda, Rotterdam, Netherlands
Manufacturer number: 3006
On February 26, 1958, the helicopter was registered with the Royal Netherlands Aviation Administration by the manufacturer under the registration mark PH-YMP. On March 27, 1958, it was registered in the name of the Dutch government, Ministry of Transport, Public Works and Water Management. The Dutch registration was canceled on April 4, 1963.
PH-YMP Kolibri photographed after its assembly
(Photo: Nico Terlouw)
History of the helicopter
In February 1958, a small airline company called “Wings of Israel” was established in Israel. The driving force behind the company was the late Jeremiah (or Jerry as everyone knew him) Renov, a pilot in the US Air Force during World War II, a pilot in the Israeli Air Force during the War of Independence and an instructor at the Air Force Flight School. Jerry was very interested in helicopters as platforms for aerial spraying, and a year after founding “Wings of Israel” he traveled to the Netherlands to closely examine the Kolibri helicopter. Upon his return to Israel, he brought with him not only the first helicopter of this type (4X-BEE) but also all the plans and in fact all the components of the production line, including the helicopter molds (Production Jigs), with the intention of continuing to build the helicopter in Israel and marketing it for military and civilianpurposes.
Of the 11 helicopters built, six were transferred to Israel, of which only four were airworthy and flew in practice. These were 4X-BDE which arrived in April 1959, 4X-BDA which arrived in May 1960, 4X-BDB which arrived in August 1962 and 4X-BDC in April 1963. Two additional helicopters were brought in complete condition but were never operated.
Jerry Renov's attempts to produce the helicopter in Israel were in vain. There were several reasons for this. First, there were more successful helicopters with conventional propulsion such as the Hebel 47 and the Alouette, and second, the market for this helicopter, which was limited inperformance and weak in engine power (60 hp per engine!) was not sufficient to justify serial production. Jerry's enthusiasm for the helicopter did not cease even when it was clear to him that he would have to settle for operating the helicopter rather than producing it. In an interview he gave in March 1967 to the British aviation magazine Aeroplane, he praised the helicopter. His attempts to offer the Kolibri to Chimavir and Marom Aerial Spray companies were rejected outright. Chimavir had already committed to purchasing Djinn helicopters that had previous experience in agricultural spraying in Europe, while Marom expressed no interest in the helicopter as an agricultural spraying platform at all, mainly because of the high maintenance costs.
In the first half of the 1960s, the Kolibri fleet accounted for 5% of the agricultural spraying segment in Israel, about one hundred flight hours per year. During the agriculturally “dead” months (December and January), the helicopters operated in the service of the Israel National Fund, spraying herbicides on forest fire trails throughout the country, but after a few years, the KKL-JNF preferred to carry out this activity from the ground, and Jerry returned to concentrating their activities on agricultural spraying in the summer months. The rest of the time was spent taking aerial photographs and dragging advertising posters. In Renov's opinion, the Kolibri failed because of its high price (about $23,000 without the spraying equipment), even though he estimated the market at two hundred units, and if he had succeeded in producing them in Israel, the cost would have dropped to $15,000 per helicopter.
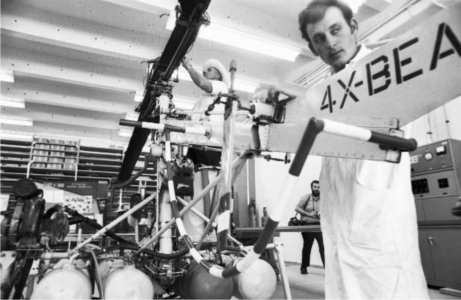
While performing maintenance work in Herzliya
(Harvard University Digital Collection)
The days, demonstrated the helicopter's performance to Col. Israel Ben-Amitai, the chief artillery officer at the time. The officers of the force were enthusiastic about its performance as a forward artillery observation helicopter, but the monopoly on operating military aircraft was in the hands of the Air Force, which already operated Alouette helicopters for this purpose, and showed no enthusiasm for adding an unusual and limited helicopter like the Kolibri to the IAF. Jerry Renov operated the last remaining Kolibri in the world (4X-BEA) for a while in the US where he had a subsidiary of "Wings of Israel", under the civil registration number N88983 registered in his name, but when the FAA (Federal Aviation Authority) refused to extend the validity of the helicopter's airworthiness certificate, they returned it to Israel, and operated it at the IAI MATA Jerusalem plant for testing purposes. The American registration was canceled on September 2, 1969.
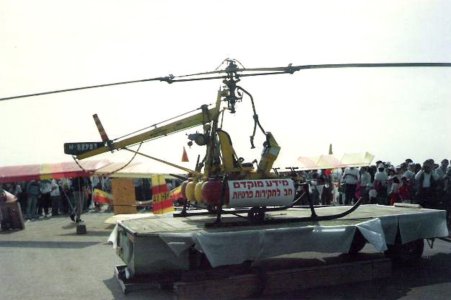
The hummingbird, still on American registration after its return from the US, on display
(Photo: Shaham Aloni)
In 1985, upon the expiration of the contract with IAI, the helicopter was transferred to the Air Force Museum in Hatzerim. The museum's commander, Yaakov Turner, accepted Jerry's request to store the helicopter in the museum, even though he was never a member of the Air Force's staff. The second surviving Hummingbird H-3 in the world is currently on loan from the Aviodrome museum (located at Lelystad Airport) to the Air- and War Museum on the island of Texel.
In the early 1990s, Jerry Renov's Hummingbird was removed from the Air Force Museum in a rather dilapidated condition. Although the Hummingbird was considered an efficient helicopter in terms of its performance in the field of agricultural spraying (it was a large consumer of fuel, 200 liters of fuel versus 200 liters of spray liquid!), it operated in the agricultural service for a very short period, less than seven consecutive years, and its operation was discontinued mainly because Jerry was an excellent pilot but a poor businessman, and was unable to operate his helicopters with the required profitability.
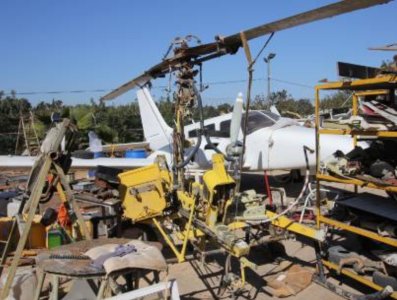
The remains of the helicopter were found at the “Avirom” company at the Herzliya airport.
At a scrapyard in Herzliya Airport, the helicopter was refurbished for display at the “Avirom” company, and it was marked with the original Dutch civil registration markings.
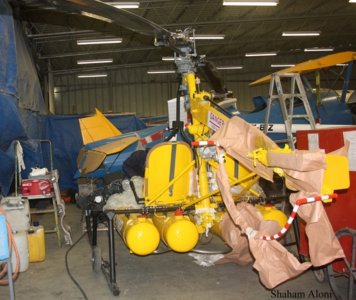
The Hummingbird after the renovation at “Avirom".
(Photos: Shaham Aloni)"