- Joined
- Dec 1, 2016
- Messages
- 5,950
- Points
- 728
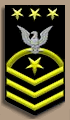
The project begins with tracing the 14 stern frames from Harold Hahn's modeling plans of the Alfred. The frames were scanned as a JPEG file and linked to CAD. Auto Cad does not import files it links to files. Hahn's original Alfred drawinga are in 1/8 scale so i am enlarging the build to 3/16 scale.
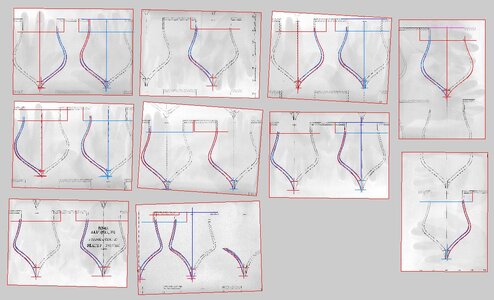
i just traced one side of each frame because i can mirror the drawing for the other side, this insures both sides are exactly the same.
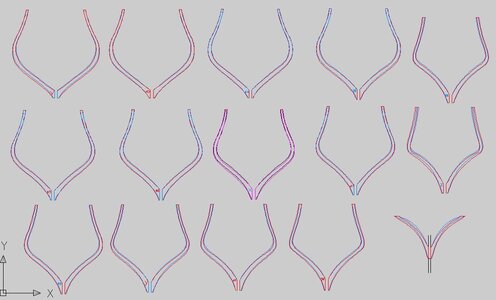
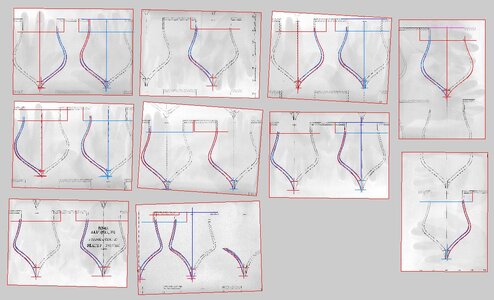
i just traced one side of each frame because i can mirror the drawing for the other side, this insures both sides are exactly the same.
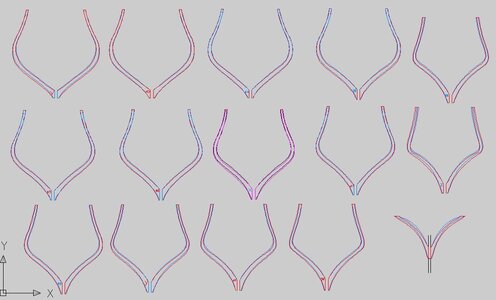