- Joined
- Dec 1, 2016
- Messages
- 6,049
- Points
- 728
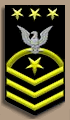
i used super glue to assemble the hull which made it easy to take apart with acetone. A couple drops and the glue gets soft and gummy.
I took each frame and painted the side with bright day glo green, next i laid them on my scanner and scanned them. Now i have an accurate template to bring back into CAD and trace them and make corrections on the inside of the frames.
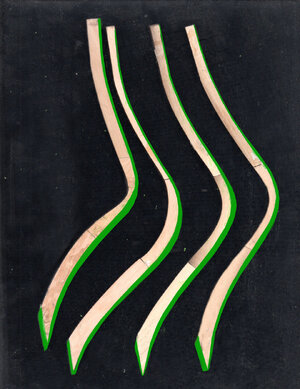
The new frame drawings were printed out with the bevel lines.
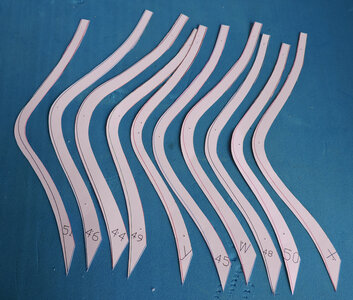
I took each frame and painted the side with bright day glo green, next i laid them on my scanner and scanned them. Now i have an accurate template to bring back into CAD and trace them and make corrections on the inside of the frames.
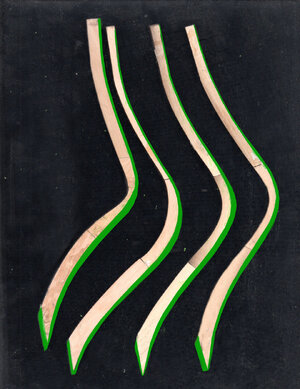
The new frame drawings were printed out with the bevel lines.
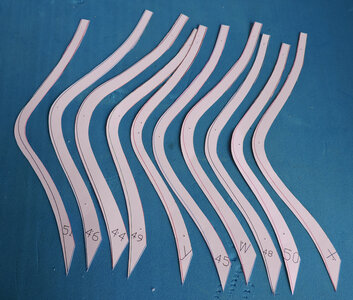