Yeah, another one. There are already so many builds, of such high quality, that I'm sure you're thinking we don't need another one. But I'm hoping that my build might provide some interesting discussion, and the build will definitely be from a professional non-perfectionist viewpoint. Besides, Uwe asked me to do it. 
I won't go through opening the kit, as there are so many other threads with better coverage. I'll try to cover some things I haven't seen, or perhaps that I've done differently. Please excuse my clumsy start and initial photos; I'm taking pictures with my phone, and am not sure how they will turn out or how this will read, so today's posts are practice, and hopefully they will later improve.
The first thing I did after receiving the kit (full pear version, with interior, barrels, and carved belfrey and railing) for Christmas was to go to Staples. There is just one large sheet of plans, 34" x 48", and of course folded:
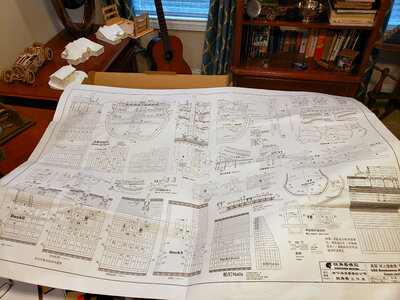
This makes it a bit hard to work with, especially without ruining the original plans, so I had Staples make 2 full-size copies ($6 each), and also a file of the image in PDF format. I cut up one of the large copies, including small details that related to each other in each separate "sheet", but most are copies of the larger cross sections and views I will be relating to. I am able to easily work with the smaller sheets, and protect them with glass or wax paper during work, so as not to have to keep making copies.
A topic of conversation here about this kit is the lack of English instructions. It appears that Unicorn has heard our pleas, as there is a fair amount of English translations currently included with the kit. If you zoom in on these plans, you will see that area titles and some notes have been translated from Chinese to English. I used Google Translate to view translations to confirm their validity (included translations in general are better than Googles) and make any notes or changes. The 30+ page instruction manual is all photos and pictures, but they have included 6-pages which list Chinese and English for each step:
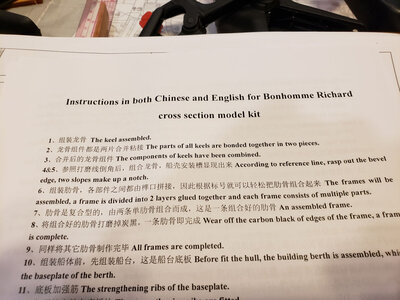
While not elaborate, they are definitely helpful. If anyone building this kit does not have the translations, please let me know and I'll post a copy that you can print.
The optional Interior Kit has instructions on 8 A4 sheets (8.25" x 11.5") and includes both Chinese and English:
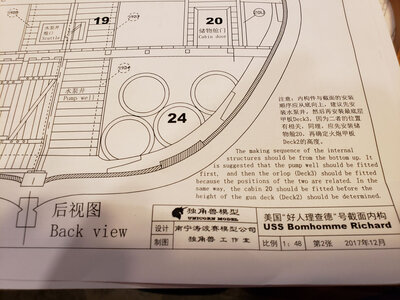
I decided to start the kit by doing a complete frame, as I knew there would be a lot more to come, and I wanted to practice, get ideas, and maybe get more ideas from you. I chose Frame 2 to start, as 1) It wasn't as visible as 1 or 9, which show at the outside, nor did it contain any cuts for gun ports (more on that later). While the quality of the stripwood is fantastic, as is the quality of the wood with the laser-cut parts, I'm not as happy with the laser-cut parts. First, they're hard to "punch" out, requiring cuts with a blade in the uncut areas. Someone mentioned using a "sturdy" blade, so I used a retractable utility knife. It didn't do badly, but I still had to cut both sides, and I found the long blade would sometimes cut into areas I didn't want. I'm going to try a shorter, thinner scalpel blade to see if it does better. One of my problems is that cataract surgery has left my "good" eye no longer able to see at close distances, so I have to switch to strong reading glasses (3.0, 4.5 and 6.0) to see close stuff. I /think/ I'm cutting right without them, then see my errors with them.
The second disappointment is that the laser cuts are not perpendicular to the surface. Although they appear much larger, I've measured them at 2-6 degrees, probably averaging midway. This results in a bad fit without sanding, a lot of sanding for a good fit, an pieces end up a bit narrower than they should be when done on both sides. Neptune, in his excellent build log, mentioned to keep the same face of the wood upright when building the frames; I suspect the angle, which he also mentions, is the reason for this. I tried switching around trying for a better fir without sanding as much, but that didn't help. These pics give you an idea of the angle (ruler is shoved in tight to a cut joint):
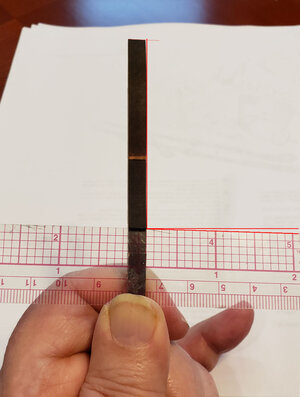
The notch where the keel fits into the lower frame (floor?) notches is tight, so it ends up at an angle too:
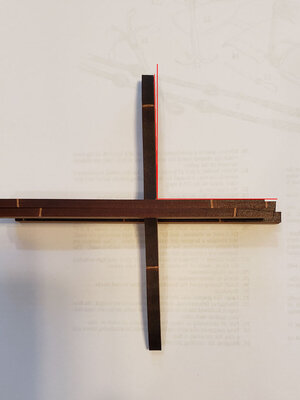
I have to file the openings somewhat larger so the frames will fit the keel when at a right angle.
As much for practice photography and testing, here are a pile of frames before sanding the joining areas:
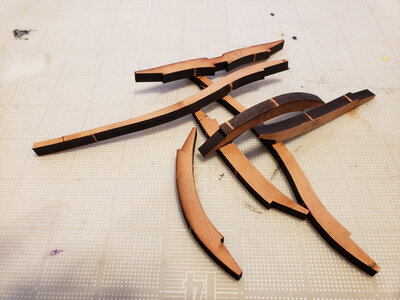
And afterwards:
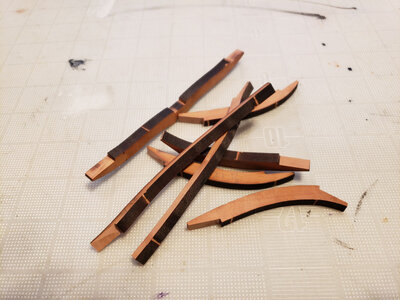
I sanded them at right angles to the outline surface, just taking off the char in this area now. It's easy to sand too much off and not notice it. This applies to the end and "notched" areas, especially. I found that when I had a mating pair about right, I could hold them an "rock" them back and forth, to see if one end was a bit too long, and if so, sand it down to fit better.
For my first frame assembly I used clothespins to secure the joints. I tried the plastic clamps, but the frame thickness was too small. Also, I tried Elmer's Glue-All, but it didn't dry fast enough to suit me, so switched to Titebond Quick & Thick, which I'm happy with so far.
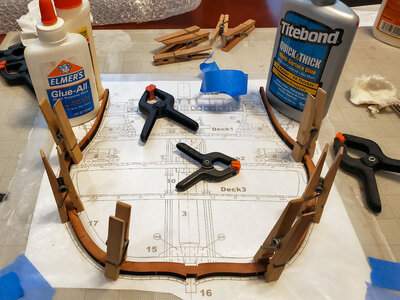
This clamping method didn't work out that well for me, though. When doing the second half, I found that the clamping force of the clothespins on the sloped scarf cause the pieces to slide and separate, and I didn't see that until picking the piece of some time later. I used water and slowly separated the pieces on that half, cleaned it up and redid it. This time I placed clothespins like this:
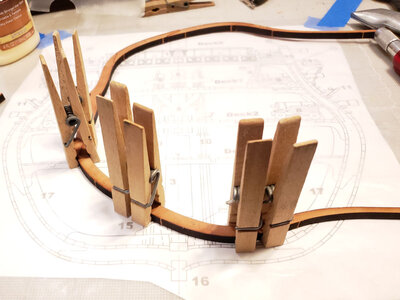
This clamped each clamping edge on part of each piece, keeping it snug, but not causing the slide. I've ordered 20 2" metal clamps which I hope to use in the future with better results.
I wasn't sure whether to build up a second half-frame (the two are fastened together) and glue it over the first, or build up the second on top of the first. In the end I chose the second method, feeling I'd keep alignment better, and I think it did:
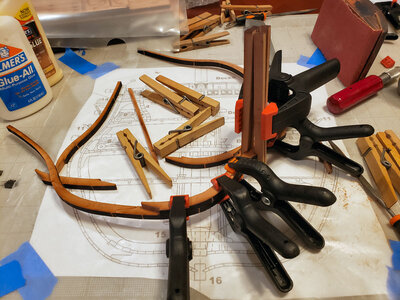
I used two of the keep pieces clamped in place to keep the two floors in alignment. Then added, and clamped, added and clamped.
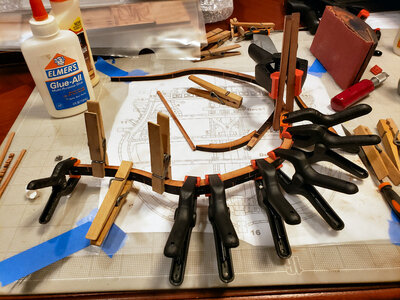
After drying overnight, I sanded the inner and outer char off. Alignment wasn't as good as I'd hoped, and the section is slightly thinner than it should be because of this. I hope my other frames, using a different clamping system, will be better. I've also glued the first four parts of the keel together with the bevels for planking. I found this easier to assemble two pieces at a time, true up, then continue.
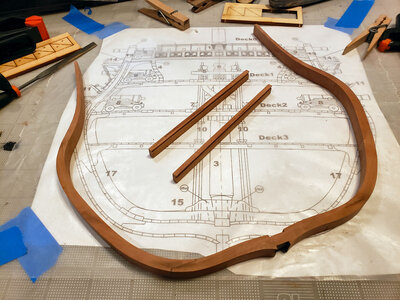
Speaking of the keel, I've come to my first question (I'm hoping I will get more from you during this thread than I will show you): Shouldn't there be a FALSE KEEL on the model? I'm not that familiar with the construction of French ships, but thought this was pretty much standard: a replaceable timber to protect the keel and its joints. I can easily add a piece to the bottom, of course, but didn't want to if it shouldn't be there.
My second question refers to the jig that is included for frame alignment:
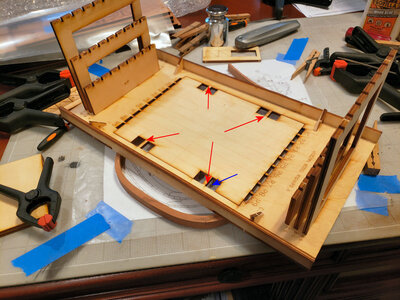
I've followed its use in the instructions, but wonder: Why is the large, mostly-rectangular section of the bottom plate left loose to move? I thought at first it was to be removed, but it isn't. The little "bridges", shown in 4 locations with the red arrows, are what attach this section to the rest of the bottom plate. Allowing it to move slightly vertically. The frames don't fit that tight, and I have NO idea why this was done this way. Does anyone know? Also, the 8 rectangular cutouts on the section, one pointed to by the blue arrow, seem to have a specific outline and maybe a purpose? Again, I have no idea.
, that's my first installment. In the future, I will try to include more/better content, less pictures and more "unique" stuff. We will see. PLEASE don't hesitate to point out things I've done wrong, suggest alternate ways of doing things, etc. In short, help make me a better modeler, and this a better model.
I won't go through opening the kit, as there are so many other threads with better coverage. I'll try to cover some things I haven't seen, or perhaps that I've done differently. Please excuse my clumsy start and initial photos; I'm taking pictures with my phone, and am not sure how they will turn out or how this will read, so today's posts are practice, and hopefully they will later improve.
The first thing I did after receiving the kit (full pear version, with interior, barrels, and carved belfrey and railing) for Christmas was to go to Staples. There is just one large sheet of plans, 34" x 48", and of course folded:
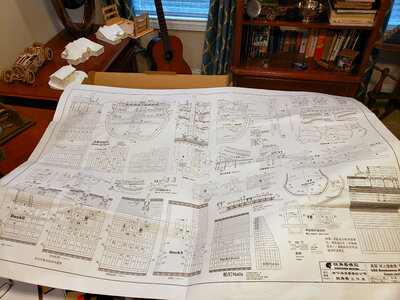
This makes it a bit hard to work with, especially without ruining the original plans, so I had Staples make 2 full-size copies ($6 each), and also a file of the image in PDF format. I cut up one of the large copies, including small details that related to each other in each separate "sheet", but most are copies of the larger cross sections and views I will be relating to. I am able to easily work with the smaller sheets, and protect them with glass or wax paper during work, so as not to have to keep making copies.
A topic of conversation here about this kit is the lack of English instructions. It appears that Unicorn has heard our pleas, as there is a fair amount of English translations currently included with the kit. If you zoom in on these plans, you will see that area titles and some notes have been translated from Chinese to English. I used Google Translate to view translations to confirm their validity (included translations in general are better than Googles) and make any notes or changes. The 30+ page instruction manual is all photos and pictures, but they have included 6-pages which list Chinese and English for each step:
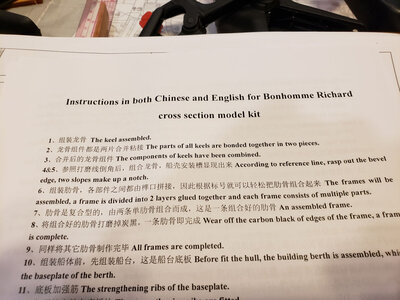
While not elaborate, they are definitely helpful. If anyone building this kit does not have the translations, please let me know and I'll post a copy that you can print.
The optional Interior Kit has instructions on 8 A4 sheets (8.25" x 11.5") and includes both Chinese and English:
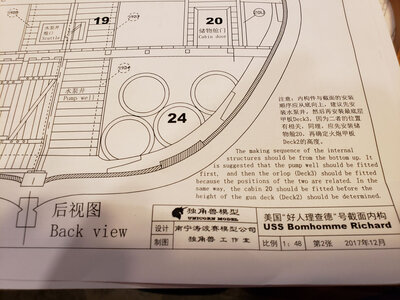
I decided to start the kit by doing a complete frame, as I knew there would be a lot more to come, and I wanted to practice, get ideas, and maybe get more ideas from you. I chose Frame 2 to start, as 1) It wasn't as visible as 1 or 9, which show at the outside, nor did it contain any cuts for gun ports (more on that later). While the quality of the stripwood is fantastic, as is the quality of the wood with the laser-cut parts, I'm not as happy with the laser-cut parts. First, they're hard to "punch" out, requiring cuts with a blade in the uncut areas. Someone mentioned using a "sturdy" blade, so I used a retractable utility knife. It didn't do badly, but I still had to cut both sides, and I found the long blade would sometimes cut into areas I didn't want. I'm going to try a shorter, thinner scalpel blade to see if it does better. One of my problems is that cataract surgery has left my "good" eye no longer able to see at close distances, so I have to switch to strong reading glasses (3.0, 4.5 and 6.0) to see close stuff. I /think/ I'm cutting right without them, then see my errors with them.
The second disappointment is that the laser cuts are not perpendicular to the surface. Although they appear much larger, I've measured them at 2-6 degrees, probably averaging midway. This results in a bad fit without sanding, a lot of sanding for a good fit, an pieces end up a bit narrower than they should be when done on both sides. Neptune, in his excellent build log, mentioned to keep the same face of the wood upright when building the frames; I suspect the angle, which he also mentions, is the reason for this. I tried switching around trying for a better fir without sanding as much, but that didn't help. These pics give you an idea of the angle (ruler is shoved in tight to a cut joint):
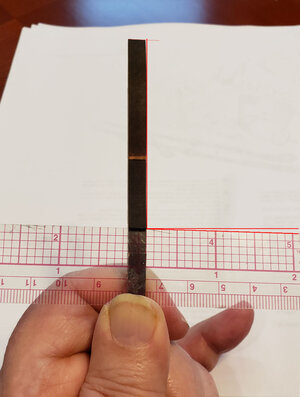
The notch where the keel fits into the lower frame (floor?) notches is tight, so it ends up at an angle too:
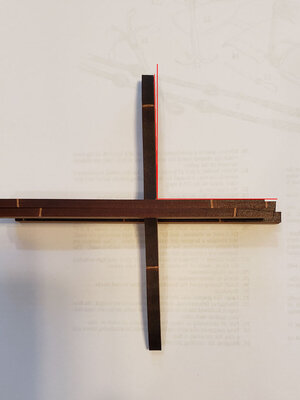
I have to file the openings somewhat larger so the frames will fit the keel when at a right angle.
As much for practice photography and testing, here are a pile of frames before sanding the joining areas:
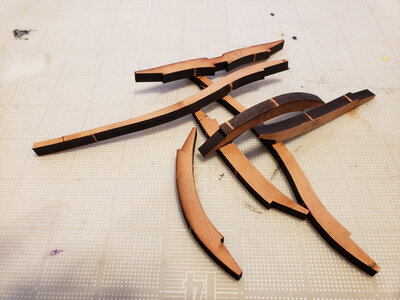
And afterwards:
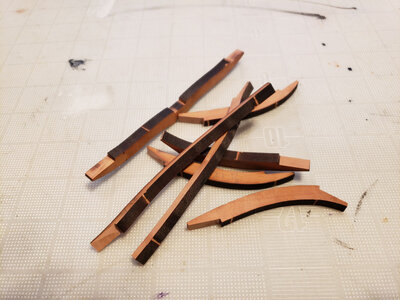
I sanded them at right angles to the outline surface, just taking off the char in this area now. It's easy to sand too much off and not notice it. This applies to the end and "notched" areas, especially. I found that when I had a mating pair about right, I could hold them an "rock" them back and forth, to see if one end was a bit too long, and if so, sand it down to fit better.
For my first frame assembly I used clothespins to secure the joints. I tried the plastic clamps, but the frame thickness was too small. Also, I tried Elmer's Glue-All, but it didn't dry fast enough to suit me, so switched to Titebond Quick & Thick, which I'm happy with so far.
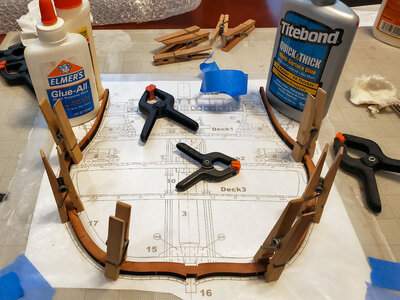
This clamping method didn't work out that well for me, though. When doing the second half, I found that the clamping force of the clothespins on the sloped scarf cause the pieces to slide and separate, and I didn't see that until picking the piece of some time later. I used water and slowly separated the pieces on that half, cleaned it up and redid it. This time I placed clothespins like this:
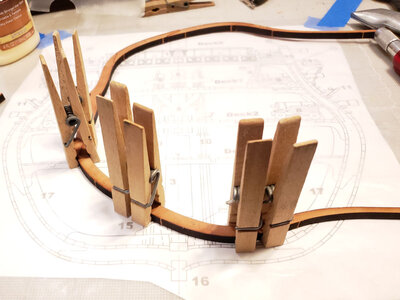
This clamped each clamping edge on part of each piece, keeping it snug, but not causing the slide. I've ordered 20 2" metal clamps which I hope to use in the future with better results.
I wasn't sure whether to build up a second half-frame (the two are fastened together) and glue it over the first, or build up the second on top of the first. In the end I chose the second method, feeling I'd keep alignment better, and I think it did:
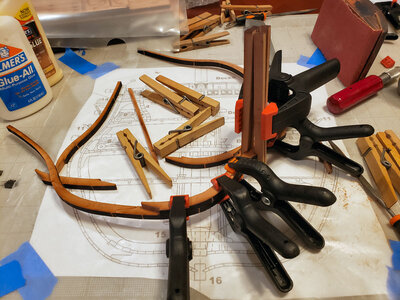
I used two of the keep pieces clamped in place to keep the two floors in alignment. Then added, and clamped, added and clamped.
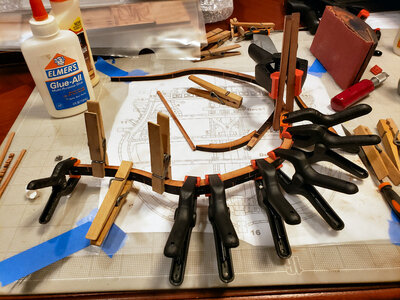
After drying overnight, I sanded the inner and outer char off. Alignment wasn't as good as I'd hoped, and the section is slightly thinner than it should be because of this. I hope my other frames, using a different clamping system, will be better. I've also glued the first four parts of the keel together with the bevels for planking. I found this easier to assemble two pieces at a time, true up, then continue.
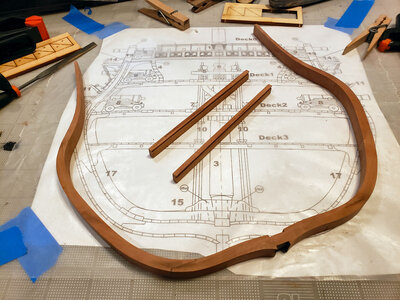
Speaking of the keel, I've come to my first question (I'm hoping I will get more from you during this thread than I will show you): Shouldn't there be a FALSE KEEL on the model? I'm not that familiar with the construction of French ships, but thought this was pretty much standard: a replaceable timber to protect the keel and its joints. I can easily add a piece to the bottom, of course, but didn't want to if it shouldn't be there.
My second question refers to the jig that is included for frame alignment:
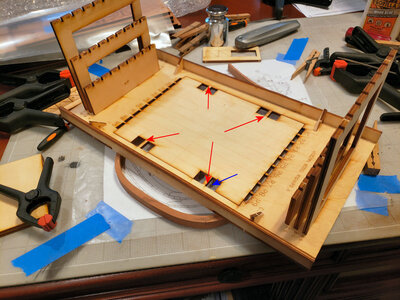
I've followed its use in the instructions, but wonder: Why is the large, mostly-rectangular section of the bottom plate left loose to move? I thought at first it was to be removed, but it isn't. The little "bridges", shown in 4 locations with the red arrows, are what attach this section to the rest of the bottom plate. Allowing it to move slightly vertically. The frames don't fit that tight, and I have NO idea why this was done this way. Does anyone know? Also, the 8 rectangular cutouts on the section, one pointed to by the blue arrow, seem to have a specific outline and maybe a purpose? Again, I have no idea.

Last edited: