Hi Paul!
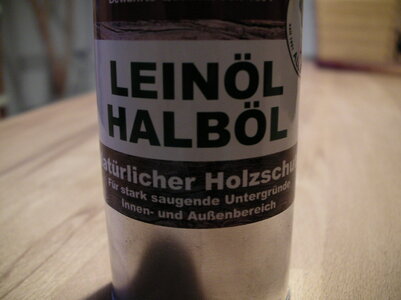
You have applied a polymerized linseed oil. It has additive to dry quickly, does not grease after drying and is dried in 36 hours. Sand the wood after the drying time very short and fine and you can glue afterwards with wood glue. I have tried such experiments myself. The adhesions hold even after years.
Paint two pieces of pear wood waste with your oil, let them dry for three days and glue them with your glue. Then try to separate the two pieces mechanically. If it is difficult, you are on the safe side.
With best regards
Thomas
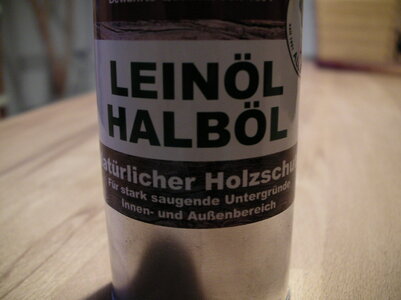
You have applied a polymerized linseed oil. It has additive to dry quickly, does not grease after drying and is dried in 36 hours. Sand the wood after the drying time very short and fine and you can glue afterwards with wood glue. I have tried such experiments myself. The adhesions hold even after years.
Paint two pieces of pear wood waste with your oil, let them dry for three days and glue them with your glue. Then try to separate the two pieces mechanically. If it is difficult, you are on the safe side.
With best regards
Thomas
Last edited: