Hello all. First I want to thank everyone who has had a look at the log and for all the wonderful comments that I have received. It is really heartening that so many of you also find the historical background interesting - that is exactly the reason why I was attracted to this subject in the first place. So with the hull having had 24 hours to "rest" and for the glue to cure properly, it was time to move forward.
The instructions now called for some of the floor planking to be done – between Bulkheads #4 and #5 at the stern and bulkheads #11 and #12 towards the bow. These will respectively form the cooking area or kitchen and the storage compartments for ropes and other miscellaneous items. Obviously, the rationale behind planking these floor-sections at this point is to aid in some form of structural rigidity to the hull assembly which, at this point, is flimsy to say the least.
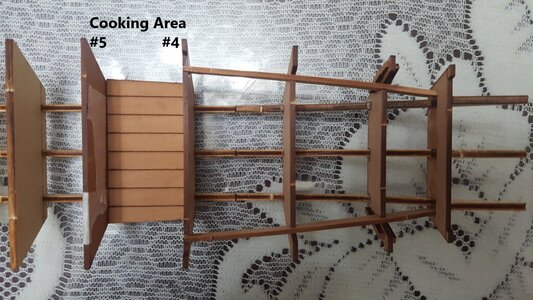
Floor planking for the cooking area (between Bulkheads #4 and #5.
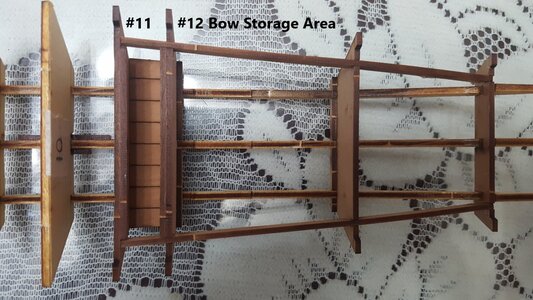
Floor planking done for the storage area between Bulkheads #11 and #12,
Interestingly, the model resembles exactly the way that the original Sampans were constructed - three bulkheads (forming four compartments), two half-bulkheads and four frames.
With that done came the crucial part of the whole hull construction – and it may indeed be the crucial part of the whole build – the bow and stern torsion bars. These bars (3mm x 4mm) have to be bent both laterally (sideways) and vertically (downwards) to slot into no fewer than 4 (for each bar) predetermined cut-out slots. Ominously (but purposely), they are also approximately 2mm too short. These bars create the tension that “forces” the Sampan hull into its distinct upswept curvature at the stern and bow. Get this wrong (only slightly) and you will end up with uneven tension, warping the whole hull assembly.
At this point the hull-assembly sits completely flat on the table and viewed from the side, basically looks like this (please forgive the amateurish drawings.)
As it stands now the shape can best be described as a “wedge”. We need to get the hull into a shape so that it looks like on the picture below.
So now comes the difficult part. Yes, with plenty of soaking in water and then using my plank bender I could potentially pre-shape those torsion bars more or less into a workable position and with copious amounts of filing and sanding, I could get it to fit pretty decently into those slots. But … then they would serve no purpose other than a cosmetic one and they would simply be filling up the slots.
No … the whole idea is that they should be “forced into those slots and into the two apertures of the rearmost bulkhead so that they could twist and strain the hull into position. However, just how much strain and stress were required? How do I “balance” the torsion between port and starboard sides? And … assuming that I got it right at the stern, this whole exercise has to be repeated at the bow end. Having fun yet?
Well to cut a long story short and as my dear friend
@pingu57 Peter said on the Dutch Modelbouwforum, I finally got it done with “water, vuur, en een hakbijl” (water, fire and an axe).
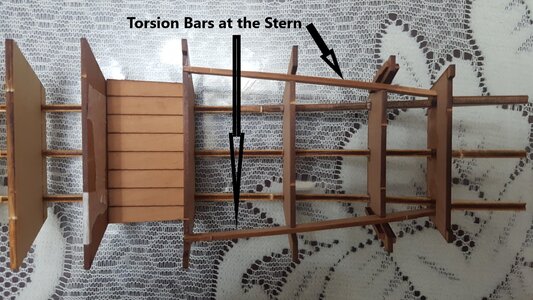
Torsion bars installed at the stern. These two were a real mission to get into position.
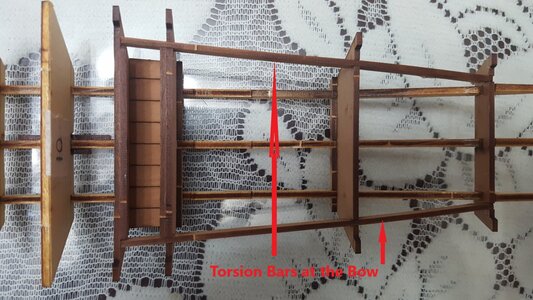
Torsion bars at the bow installed.
After the torsion bars were installed, I was happy to see that there was no warping of the hull, but I still had no idea whether my upswept curves at the stern and bow “swept up” enough or too much. That would only be possible to tell once the next stages of assembly have been completed.
Thank you very much for all your comments and for following or for just taking a look or giving a thumbs-up. It is all sincerely appreciated - and if there are critical comments, please do not be shy of posting them either!
Till next time! - Heinrich