Many thanks, @Norway Knut, @JohnA John and all for the compliments and likes! 
Continue with the false keel assembly, and today we actually moving to 'Apron' (or false post). It is consists of two parts: the upper section part BL7 and lover section part BL8. To complete this assembly we will need the rising wood part BL9.
Actually, I am learning the names of those parts alone with you! It is a great way to learn various ship parts. The parts identification can be found on page 6 of the instruction manual.
Assembly doesn't require special instructions. Once you release and clean from the timber board lightly sand and glue together. *IMPORTANT: To ensure the full alignment of all glued parts, use the template (part C52)! As I mentioned earlier, in Poul's @PoulD, response, I use black pencil 'B' to simulate caulking. Here is how it looks after assembly.
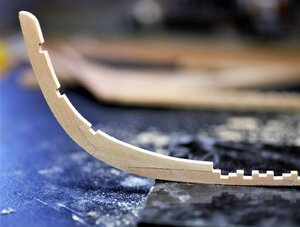

adding rising wood (part BL9)
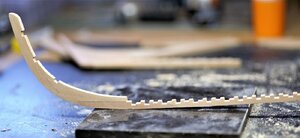
Aliment of all gluing parts can be archived by using a template (C52).

Both rising woods: false keel and apron
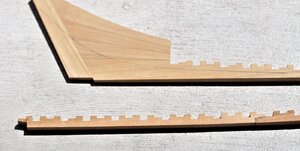
The apron a bit blurry, I am still learning photography.
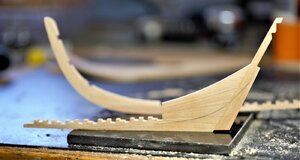
Finally, the entire assembly. The instruction suggests beveling the 'rabbet line' Will discuss this the next time.

Stay tuned, to be continued...

Continue with the false keel assembly, and today we actually moving to 'Apron' (or false post). It is consists of two parts: the upper section part BL7 and lover section part BL8. To complete this assembly we will need the rising wood part BL9.
Actually, I am learning the names of those parts alone with you! It is a great way to learn various ship parts. The parts identification can be found on page 6 of the instruction manual.
Assembly doesn't require special instructions. Once you release and clean from the timber board lightly sand and glue together. *IMPORTANT: To ensure the full alignment of all glued parts, use the template (part C52)! As I mentioned earlier, in Poul's @PoulD, response, I use black pencil 'B' to simulate caulking. Here is how it looks after assembly.
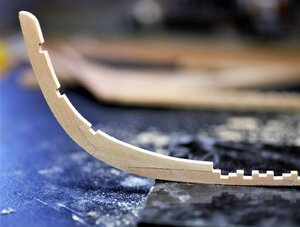

adding rising wood (part BL9)
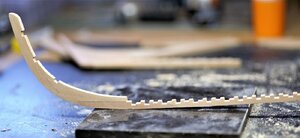
Aliment of all gluing parts can be archived by using a template (C52).

Both rising woods: false keel and apron
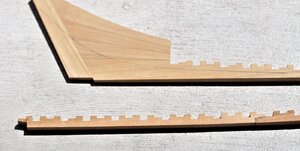
The apron a bit blurry, I am still learning photography.
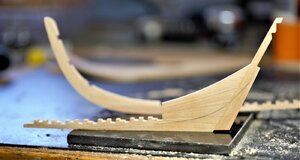
Finally, the entire assembly. The instruction suggests beveling the 'rabbet line' Will discuss this the next time.

Stay tuned, to be continued...