- Joined
- Dec 1, 2016
- Messages
- 6,028
- Points
- 728
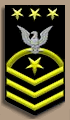
i actually have one of these i bought it at a farm sale for $20.00 i will tell you it is one heavy machine
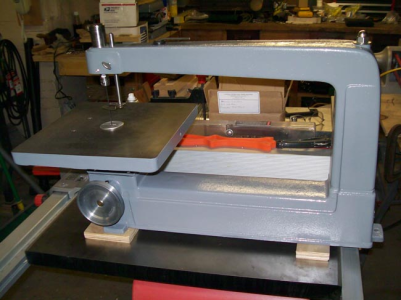
interesting you mentioned the kerf i find it an important factor in choosing a saw. It comes down to table saw vs bandsaw
the circular blade has a thin kerf of .083 to .093
if you are ripping down planking that is 1/8 x 1/16, you're losing more wood than you are saving. If you bought Pearwood at $25.00 a board foot to rip into hull planking, you are using less than 1/2 the wood the rest is saw dust.
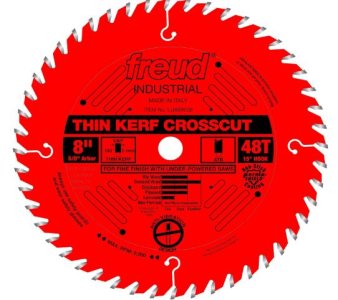
A bandsaw blade has a much thinner kerf of .020 to .025 so you will get more planks out of that piece of expensive Pearwood.
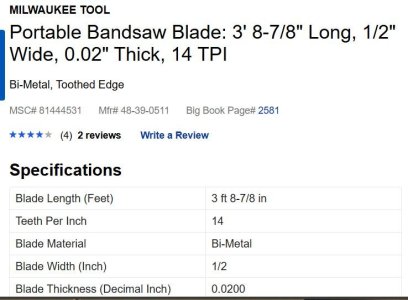
a PDF file testing thin kerf blades on a table saw
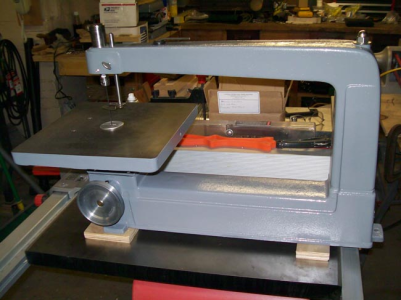
interesting you mentioned the kerf i find it an important factor in choosing a saw. It comes down to table saw vs bandsaw
the circular blade has a thin kerf of .083 to .093
if you are ripping down planking that is 1/8 x 1/16, you're losing more wood than you are saving. If you bought Pearwood at $25.00 a board foot to rip into hull planking, you are using less than 1/2 the wood the rest is saw dust.
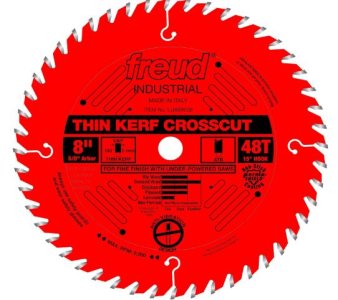
A bandsaw blade has a much thinner kerf of .020 to .025 so you will get more planks out of that piece of expensive Pearwood.
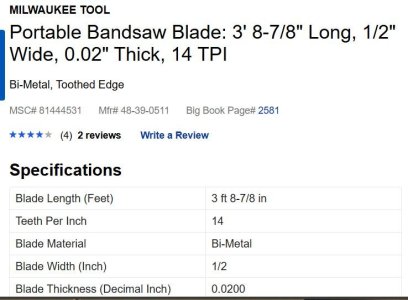
a PDF file testing thin kerf blades on a table saw
Attachments
Last edited: