Because I am butt joining the frames before laminating the two halves together I struggled to find a way to hold them in place under pressure. I finally settled on this idea. The base is a thick piece of perspex (acrylic) - over 1 cm thick - and tested for flat. I can only do a bit at a time with this sheet but if it is successful I will cut another smaller sheet so that I can do a whole frame with clamps over the edge.
If the Aquadhere sticks to the perspex I'll be in trouble but I doubt that it will.
The wood is my Silver Ash which I am finding brilliant to work. I just hope I will have enough after I build my wife's table top.
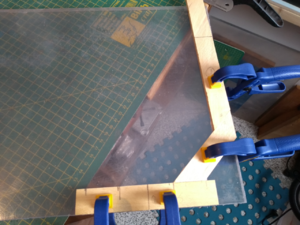
If the Aquadhere sticks to the perspex I'll be in trouble but I doubt that it will.
The wood is my Silver Ash which I am finding brilliant to work. I just hope I will have enough after I build my wife's table top.

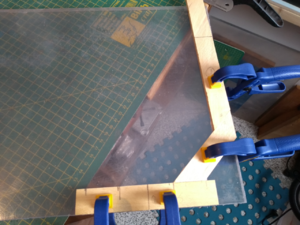