Today I fabricated the 2 perrot shafts. Really hard to do but I'm quite pleased with the result for 2 reasons, first I think they look pretty good and second, they work as they should. They transfert the rotary motion from the brake linkage to the brake shoes even when the wheel is steered. Here are some pictures and videos of the process.
The prototype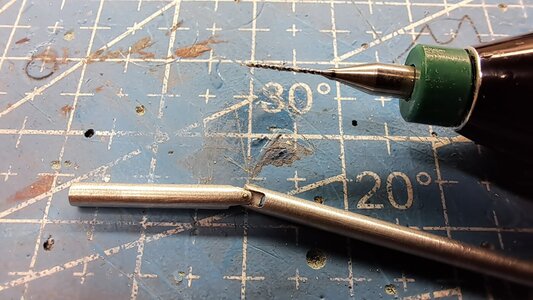
All parts cut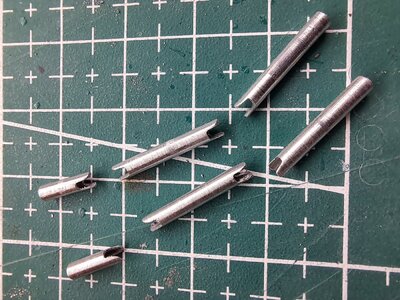
I used a small styrene rod to make the yoke and a .01 dia nickel rod for the pivot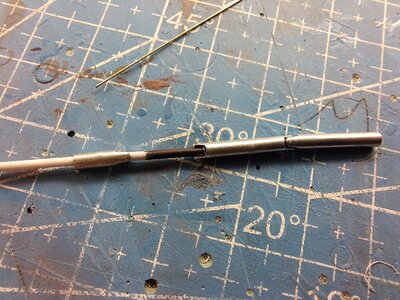
All done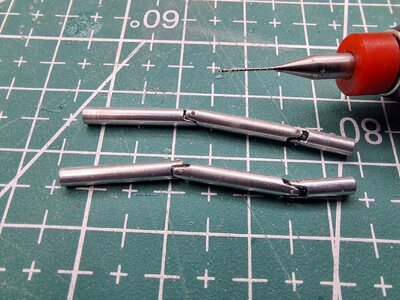
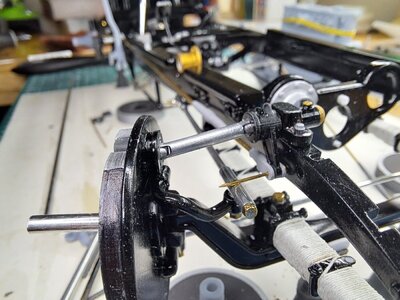
In action
View attachment 20231002_160050.mp4
View attachment 20231002_152250.mp4
I tried to make a gator to cover 1 of the 2 shafts by rolling a piece of nitrile rubber but the results are not very promissing so far. Unless I find a small (about 3/16 dia) and very thin tubing, I might leave both shafts visible.
The prototype
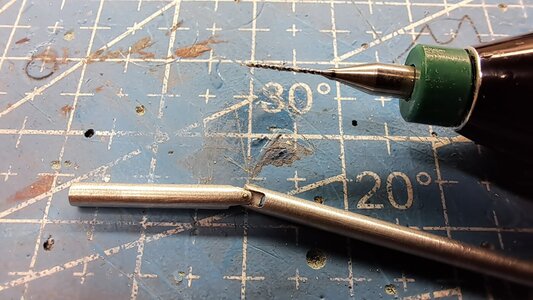
All parts cut
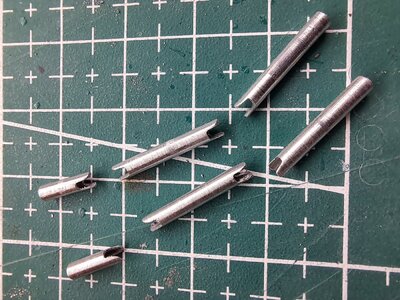
I used a small styrene rod to make the yoke and a .01 dia nickel rod for the pivot
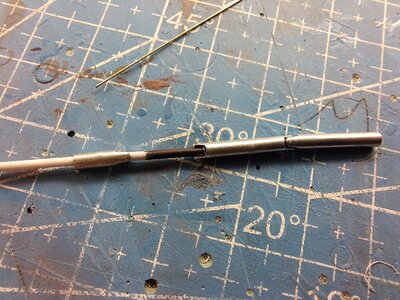
All done
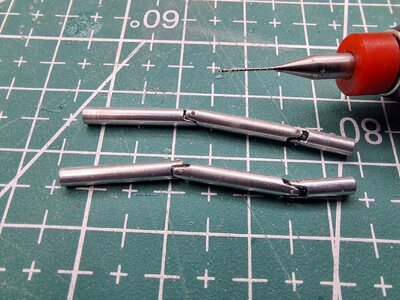
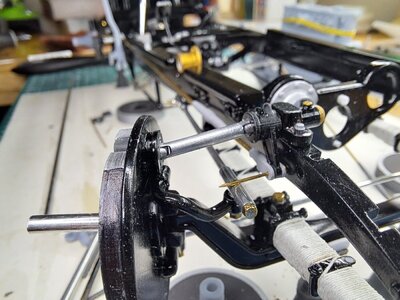
In action
View attachment 20231002_160050.mp4
View attachment 20231002_152250.mp4
I tried to make a gator to cover 1 of the 2 shafts by rolling a piece of nitrile rubber but the results are not very promissing so far. Unless I find a small (about 3/16 dia) and very thin tubing, I might leave both shafts visible.