Exactly one month ago I started this model of a 'pinas' of 134 feet long.
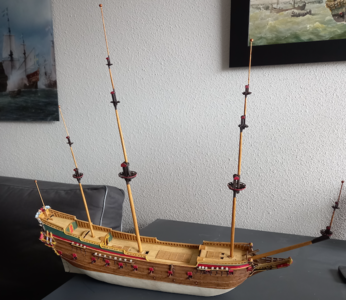
There is a story connected to this ship. I built it five times, the first one starting in 1980, the last one a month ago. It is the ship that is described in all its details by the Amsterdam lord mayor, diplomat, lawyer, cartographer and collector Nicolaes Witsen (1641-1717) in his famous book 'Aeloude en Hedendaegsche Scheepsbouw en Bestier' (Old and Modern Shipbuilding and Managing) from 1671. He was the first in Holland to describe the trade of shipbuilding in Holland and his book still is the most important source for 17th century Dutch maritime matters. His choice for this particular ship of which he wrote down over 40 pages of dimensions of all sorts was not incidental. He deliberately chose a ship of medium size (38 meters was an average length in those days) and with a double function: not only was the ship the main means of transport for people and cargo of its days, it was also a platform for a considerable amount of ordnance (24 guns). Thus Witsen combined the characteristics of both a trader and a man-of-war stating that, provided the reader did understand this construction, he was able to build any ship. That is a significant statement, because therefore this ship of his choice is not just a random vessel, is a key for understanding the system of shipbuilding of the era. The type name 'pinas' has become obsolete and disappeared from our language, but the type itself became an icon of Dutch 17th century shipping, with its gracious lines, tasteful decorations, bellowing sails, flapping flags and intimidating guns.
However, Witsen was not exactly a trained teacher. The reading of his book is a frustrating task, because apart from the fact that he constantly mixes up things which often causes confusion, many ship's parts names have disappeared over the years. No wonder that it took me three years to make working drawings based on his texts and sketches and another three years to build a construction model in pear wood in 1/50 scale, with every part in place, even if covered with planking in a later stage.
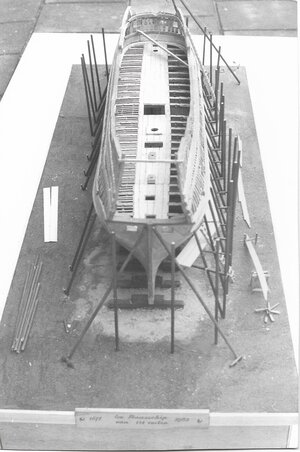
The model was purchased by the local shipping museum in my hometown Groningen, so I built a second model for 'use' in my home on a 1/100 scale. This model was sold to a private collector a few years later. Life was expensive with three upgrowing children...
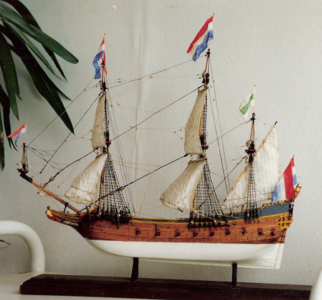
A presentation in 1988 on a congress for maritime archaeologists about the two different shipbuilding methods described in Witsen's book and by a second Dutch author on the subject, Van Yk, opened the door to a job at the Rijksmuseum in Amsterdam, taking care of the maritime collection there. In the mean time Witsen's re-arranged old text was published in 1994 in the book I wrote about the project, 'Nicolaes Witsens Scheeps-bouw-konst Open Gestelt'. An English translation was published in 2012: 'Nicolaes Witsen and Dutch Shipbuilding in the Golden Age.' Very few people's lives have been influenced in such a total manner by a 17th century patrician and the ship he described.
After my retirement in 2012 I met Rene Hendrickx, my Belgium companion with whom I built the ship for the third time, but this time virtually, in the free downloadable shipbuilding program Delftship. Less than a year ago the program was adapted for public internet use as an educational tool for archaeologists and historians by the company Tijdlab, subsidized by the Dutch Rijksdienst voor Cultureel Erfgoed (Cultural Heritage Agency of the Netherlands). The site is interesting for model builders as well and can be found at: https://witsenscheepsbouw.nl, where also the original drawings for the model can be downloaded for free.
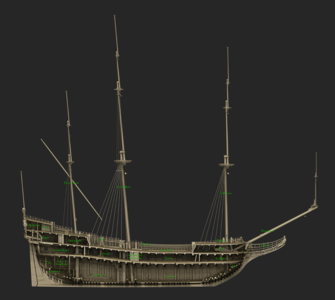
In 2014 I discovered model shipbuilding in card and for its quick results I liked it so much that I decided to build Witsen's pinas in paper and card as an experiment at a 1/77 scale. Earlier this year the model was donated to the Archaeological Museum 'Huis van Hilde' in Castricum, Holland, together with six more models of Dutch traders from the 17th century to illustrate the exhibition of wreck findings that show the large area of Dutch trading contacts of those days.
So again I had to say goodbye to the ship and it did not take long to admit to myself that I missed it dearly.
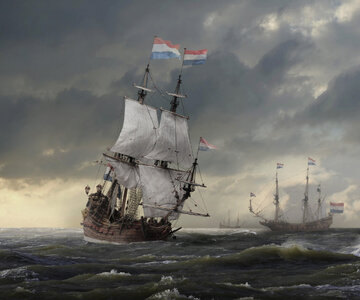
The result was that I started building my fifth pinas model exactly a month ago. The build was a breeze so far. Everything worked out fine. Perhaps you are interested in the process. In the coming time I will show you various stages and the rigging will follow soon, so stay tuned!
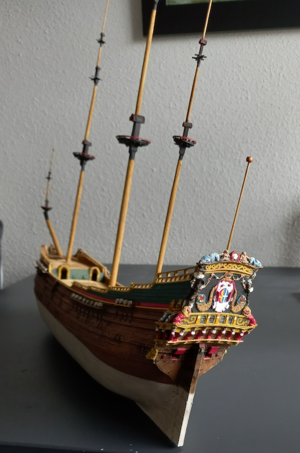
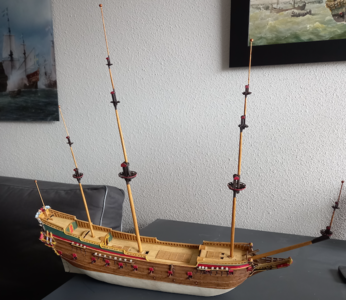
There is a story connected to this ship. I built it five times, the first one starting in 1980, the last one a month ago. It is the ship that is described in all its details by the Amsterdam lord mayor, diplomat, lawyer, cartographer and collector Nicolaes Witsen (1641-1717) in his famous book 'Aeloude en Hedendaegsche Scheepsbouw en Bestier' (Old and Modern Shipbuilding and Managing) from 1671. He was the first in Holland to describe the trade of shipbuilding in Holland and his book still is the most important source for 17th century Dutch maritime matters. His choice for this particular ship of which he wrote down over 40 pages of dimensions of all sorts was not incidental. He deliberately chose a ship of medium size (38 meters was an average length in those days) and with a double function: not only was the ship the main means of transport for people and cargo of its days, it was also a platform for a considerable amount of ordnance (24 guns). Thus Witsen combined the characteristics of both a trader and a man-of-war stating that, provided the reader did understand this construction, he was able to build any ship. That is a significant statement, because therefore this ship of his choice is not just a random vessel, is a key for understanding the system of shipbuilding of the era. The type name 'pinas' has become obsolete and disappeared from our language, but the type itself became an icon of Dutch 17th century shipping, with its gracious lines, tasteful decorations, bellowing sails, flapping flags and intimidating guns.
However, Witsen was not exactly a trained teacher. The reading of his book is a frustrating task, because apart from the fact that he constantly mixes up things which often causes confusion, many ship's parts names have disappeared over the years. No wonder that it took me three years to make working drawings based on his texts and sketches and another three years to build a construction model in pear wood in 1/50 scale, with every part in place, even if covered with planking in a later stage.
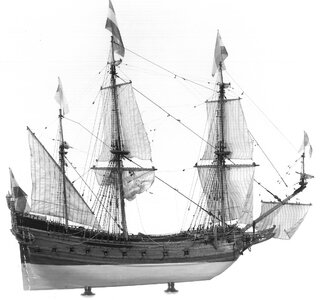
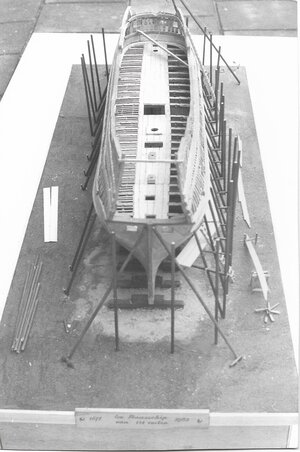
The model was purchased by the local shipping museum in my hometown Groningen, so I built a second model for 'use' in my home on a 1/100 scale. This model was sold to a private collector a few years later. Life was expensive with three upgrowing children...
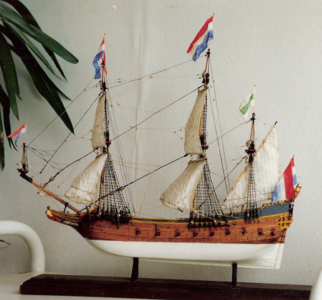
A presentation in 1988 on a congress for maritime archaeologists about the two different shipbuilding methods described in Witsen's book and by a second Dutch author on the subject, Van Yk, opened the door to a job at the Rijksmuseum in Amsterdam, taking care of the maritime collection there. In the mean time Witsen's re-arranged old text was published in 1994 in the book I wrote about the project, 'Nicolaes Witsens Scheeps-bouw-konst Open Gestelt'. An English translation was published in 2012: 'Nicolaes Witsen and Dutch Shipbuilding in the Golden Age.' Very few people's lives have been influenced in such a total manner by a 17th century patrician and the ship he described.
After my retirement in 2012 I met Rene Hendrickx, my Belgium companion with whom I built the ship for the third time, but this time virtually, in the free downloadable shipbuilding program Delftship. Less than a year ago the program was adapted for public internet use as an educational tool for archaeologists and historians by the company Tijdlab, subsidized by the Dutch Rijksdienst voor Cultureel Erfgoed (Cultural Heritage Agency of the Netherlands). The site is interesting for model builders as well and can be found at: https://witsenscheepsbouw.nl, where also the original drawings for the model can be downloaded for free.
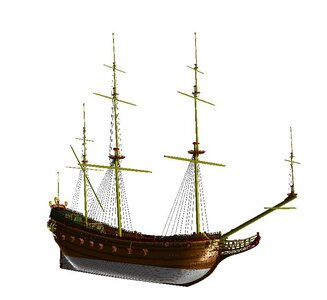
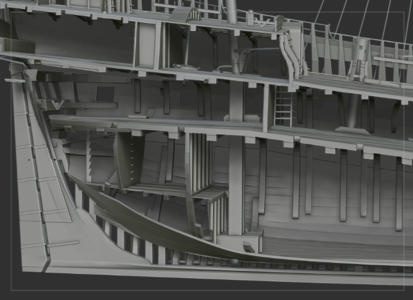
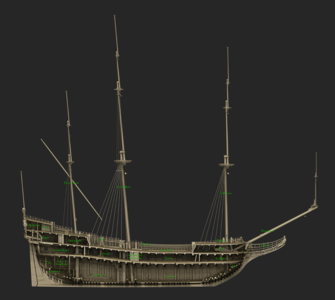
In 2014 I discovered model shipbuilding in card and for its quick results I liked it so much that I decided to build Witsen's pinas in paper and card as an experiment at a 1/77 scale. Earlier this year the model was donated to the Archaeological Museum 'Huis van Hilde' in Castricum, Holland, together with six more models of Dutch traders from the 17th century to illustrate the exhibition of wreck findings that show the large area of Dutch trading contacts of those days.
So again I had to say goodbye to the ship and it did not take long to admit to myself that I missed it dearly.
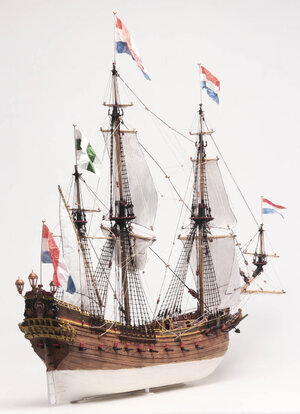
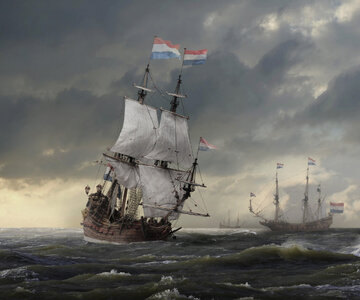
The result was that I started building my fifth pinas model exactly a month ago. The build was a breeze so far. Everything worked out fine. Perhaps you are interested in the process. In the coming time I will show you various stages and the rigging will follow soon, so stay tuned!
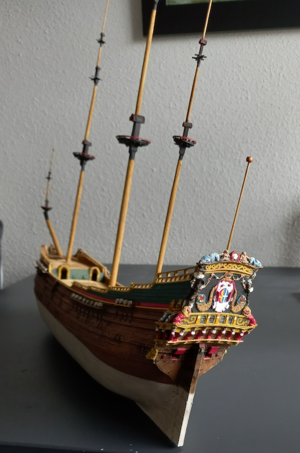
Last edited: