DHL delivery from China Today!!! I'll post a few pictures from the unboxing below. Next post, I'll discuss my thoughts on making a duplicate with a bunch of Alder I have from a recent project.
First impressions:
1. Kit arrived via DHL in Eight days! It was well packed and looked pristine when I removed the exterior wrapping (photo 1).
2. There is a very large plan sheet (photo 2) is just 1/4 of the sheet. Printing is clear and precise. Translations from Chinese to English look adequate.
3. There is also a set of smaller drawings on a dozen or so sheets that show specific instructions and details (photo 3). Again, clear images and translations look adequate.
4. The wood (pictures 4 &5) looks like quality fine grain wood. It seems a slightly shade of pink than other pear wood I've worked with. We'll see how it sands and accepts stains/oils/etc. The laser etching is extremely fine and accurate and it doesn't look like the char extends too deep...more to follow as I begin detaching pieces.
5. The accessories look fine. Cannons, deadeyes and blocks look excellent (photo 6). Much of this may be substituted or swapped out (line, wire, etc) as I customize and fine tune things.
The construction cradle sheets look very accurate and substantial enough to keep things aligned.
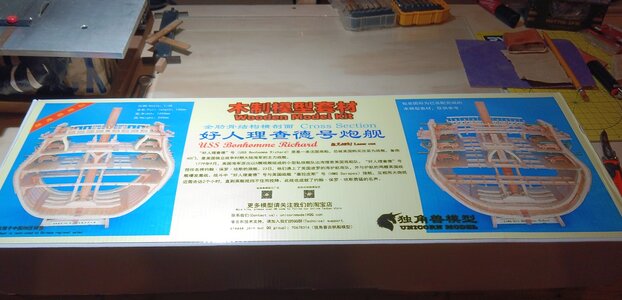
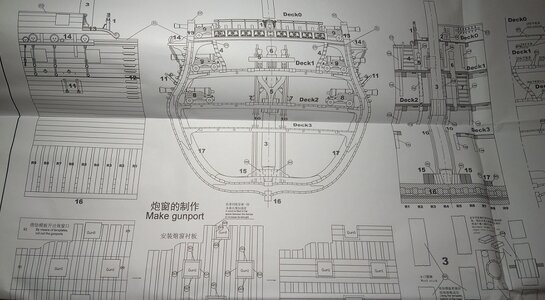
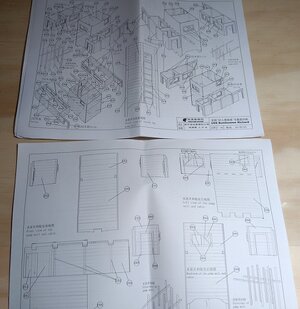
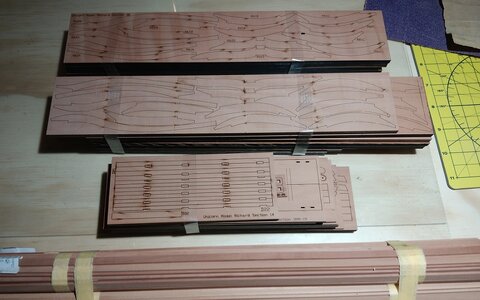
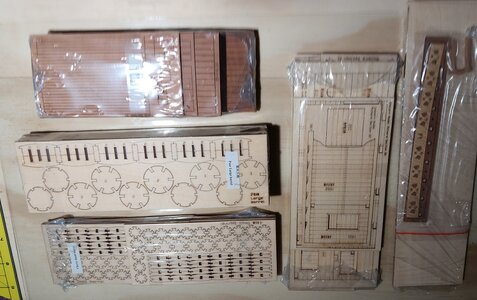
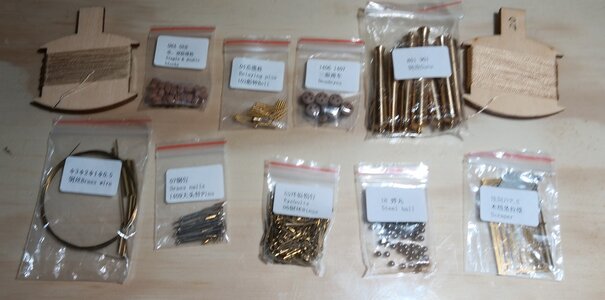
First impressions:
1. Kit arrived via DHL in Eight days! It was well packed and looked pristine when I removed the exterior wrapping (photo 1).
2. There is a very large plan sheet (photo 2) is just 1/4 of the sheet. Printing is clear and precise. Translations from Chinese to English look adequate.
3. There is also a set of smaller drawings on a dozen or so sheets that show specific instructions and details (photo 3). Again, clear images and translations look adequate.
4. The wood (pictures 4 &5) looks like quality fine grain wood. It seems a slightly shade of pink than other pear wood I've worked with. We'll see how it sands and accepts stains/oils/etc. The laser etching is extremely fine and accurate and it doesn't look like the char extends too deep...more to follow as I begin detaching pieces.
5. The accessories look fine. Cannons, deadeyes and blocks look excellent (photo 6). Much of this may be substituted or swapped out (line, wire, etc) as I customize and fine tune things.
The construction cradle sheets look very accurate and substantial enough to keep things aligned.
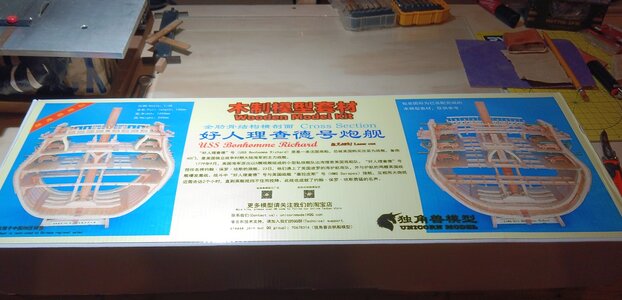
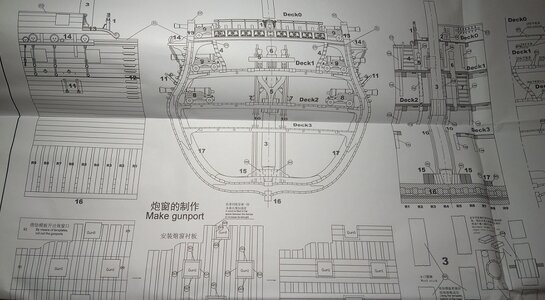
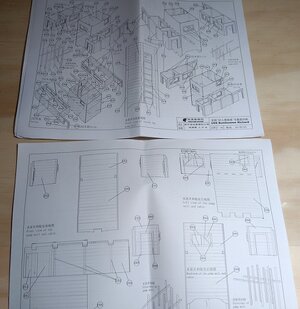
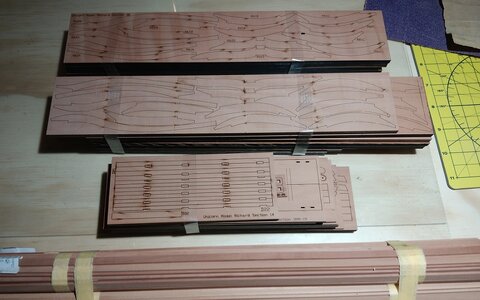
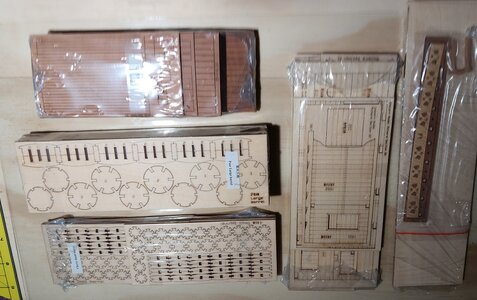
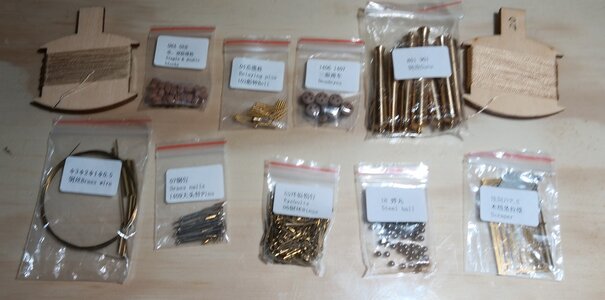