This is my first model build in decades and it's slow going. These photos are over the past month or so. These are some tools and supplies I bought.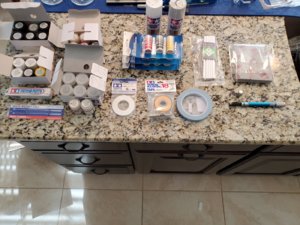
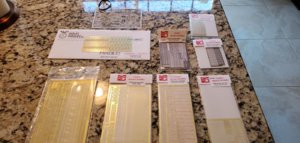
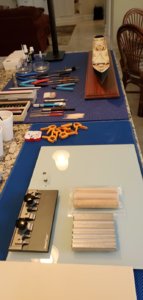
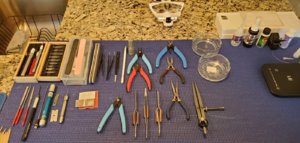
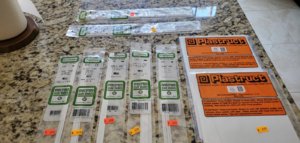
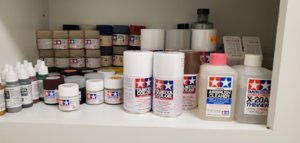
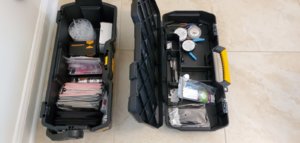
The kit number is 11320, I believe it is the newest version.
I made the base out of a 30 inch 1 x 6 of mahogany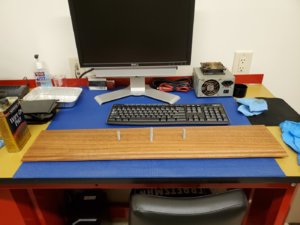
I primed the hull with Tamiya fine surface primer in grey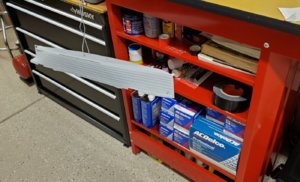
I airbrushed it with Tamiya flat black and flat white. I really wanted to put the gold stripe on it but I could not figure out how to get a 3/64 stripe masked over the raised rivets on the hull. Maybe with more experience I will be able to accomplish things like that.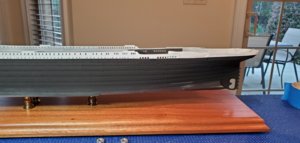
I airbrushed the bottom with Tamiya hull red. I didn't putty anything as I am just trying to get used to actually building the model simply. In future projects I hope to.
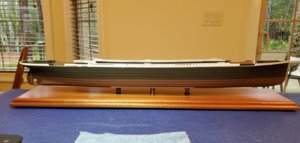
The hull kit seems out of spec. I had to grind off the casting and use toothpicks as a stop to get it all lined up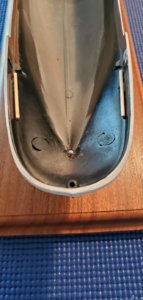
The model is also really warped, especially the main deck. I made a channel and glued steel stock to the deck to take out the flex and ease installation.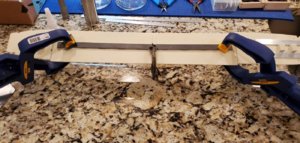
I am using Scaledecks wood deck. My first time with this also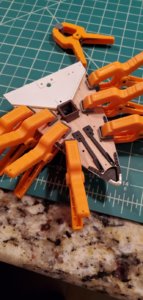
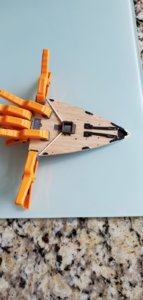
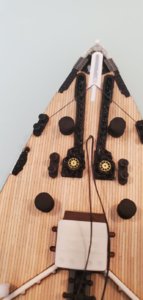
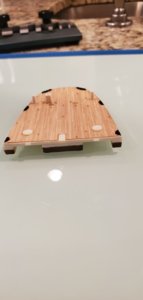
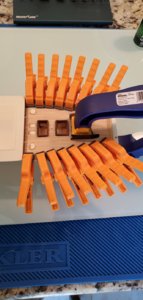
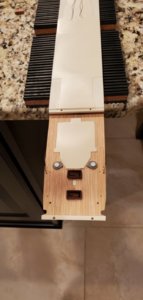
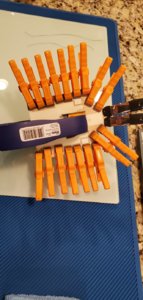
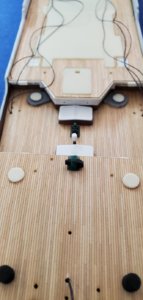
I got the first deck on permanently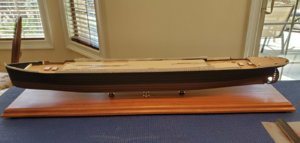
I also made my first try at photo etch. It's a real challenge for me.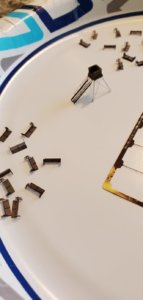
I have decided to redo the compass tower as I did not like the way it came out. This is the one I plan to use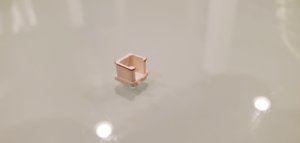
The forum says I can only attach 25 files and that's what I'm up to. I will try to continue in another post. Thanks for viewing.
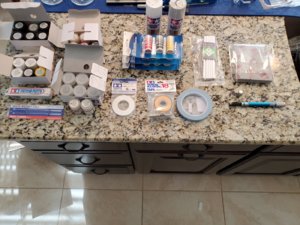
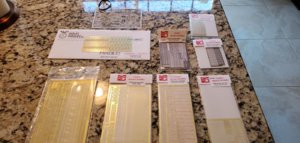
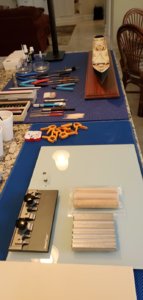
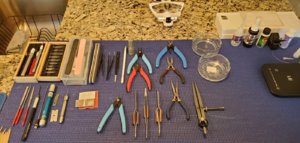
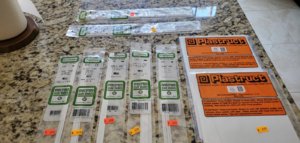
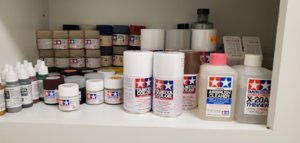
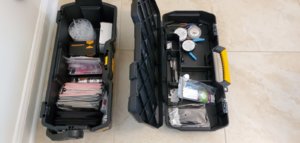
The kit number is 11320, I believe it is the newest version.

I made the base out of a 30 inch 1 x 6 of mahogany
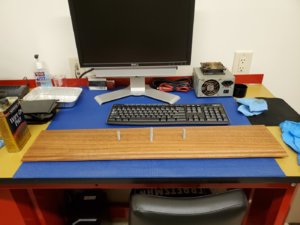
I primed the hull with Tamiya fine surface primer in grey
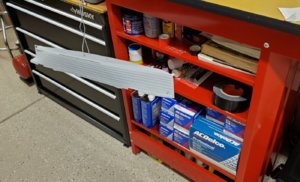
I airbrushed it with Tamiya flat black and flat white. I really wanted to put the gold stripe on it but I could not figure out how to get a 3/64 stripe masked over the raised rivets on the hull. Maybe with more experience I will be able to accomplish things like that.
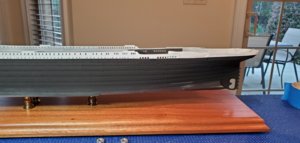
I airbrushed the bottom with Tamiya hull red. I didn't putty anything as I am just trying to get used to actually building the model simply. In future projects I hope to.
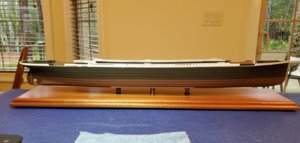
The hull kit seems out of spec. I had to grind off the casting and use toothpicks as a stop to get it all lined up
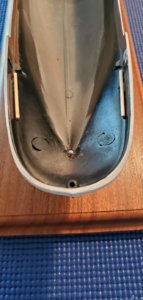
The model is also really warped, especially the main deck. I made a channel and glued steel stock to the deck to take out the flex and ease installation.
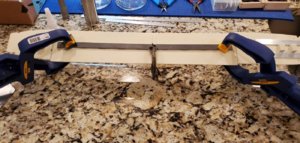
I am using Scaledecks wood deck. My first time with this also
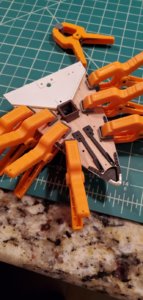
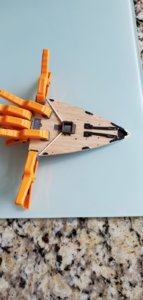
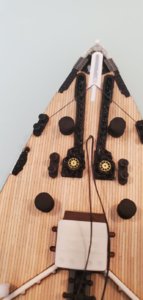
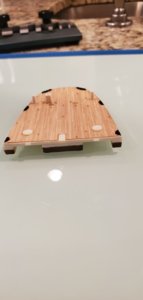
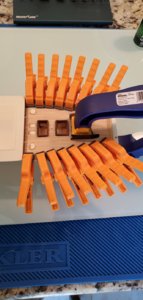
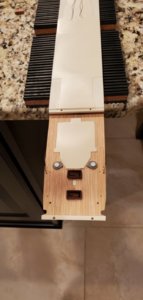
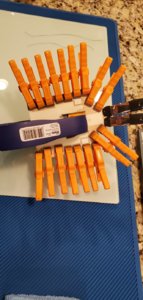
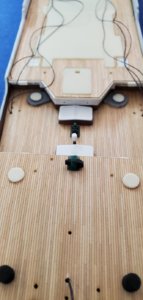
I got the first deck on permanently
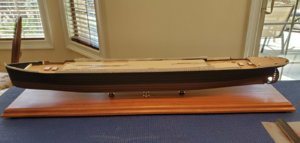
I also made my first try at photo etch. It's a real challenge for me.
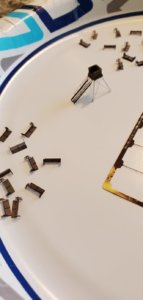
I have decided to redo the compass tower as I did not like the way it came out. This is the one I plan to use
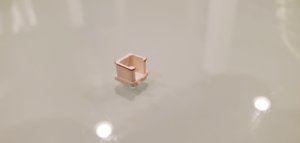
The forum says I can only attach 25 files and that's what I'm up to. I will try to continue in another post. Thanks for viewing.