Hi Ted
I made a mistake, the aurora was created by a samurai-like man with his hair tied back.
I invite him to SOS.
Now, since there are no cutouts in the hull jigs C13 and C14, I decided not to glue D1 to D3, C13, and C14.
There is no problem if you tie it with a packing string.
The jigs made by the bow frame group were excellent.
It was easier to glue the bow frame and rib1# together before attaching to the keel.
The bow frame group will not enter unless the protrusion of the red arrow of C14 is cut off.
I checked the rib height again and glued the keel and ribs from the front.
Temporarily fixed the top of the frame before sanding.
It is convenient that the strap for packing can be used for adhesive fixation.
I was sweaty and did the sanding by hand.
(Work in the garden when there is a lot of wood waste.)
I glued the keelson.
When the rear frame is made, No. 1 is finished.
The red arrows cut out the jig.
2A-13 and 3F-5 can be attached.
I would like to attach 3A-3 that comes with No. 3 for positioning and strength.
The orange line is the dividing line.
I used a template to check the position of the Deck clamp etc.
This is a template that is very helpful because it is easy to make errors here, but you need to be careful because the position of B in No. 1 is likely to be mistaken about 2 mm below.
The cutting line when dividing the bottom of the lower main wale into upper and lower parts with a thin saw is on the deck clamp of the green line.
If I cut, I plan to cut just above the Deck clamp.
After cutting, I plan to stick the wale on the upper part of the hull to a little below the cut line.
It seems that cutting will be difficult if Mortar pit beam is attached before cutting.
I plan to use the thick plates in the ship if I can process the materials from the kit and use them.
The cut of the outer plate of the CAF model is a problem, but with my technical skills, the width of the outer plate of the kit varies a lot and the curve is a little unnatural, so I don't think it will fit well. I plan to purchase the outer plate separately.
My favorite hull panels have few grains and stains, and the width of the hull panels other than the bow should be even on the top and bottom, and only the bow should be slightly curved.
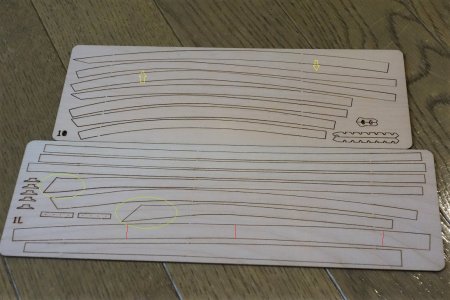
The assembly instructions for No. 3 do not include an explanation of the upper/lower division nor a diagram of the division.
The upper and lower division of the hull seems difficult to me, and I feel that it is 30%.