This is a view looking through the second port-side lower deck gunport. The foremast can be seen to the left, the large object dominating the image is the riding-bitt to which the anchor cables are secured while the ship is under way. The thick cable at the top is the messenger. This is an endless circular rope which runs from the bow then aft to the mizzen mast then back to the bow. When it is not in use (like in this image) it is hung up onto the deck-beams, when in use it would be released from the deck-beams and laid out onto the deck. The lower thick cable is one of the anchor cables. Two stoppers can be seen, one is lying on the deck to the left, the other is standing upright in front of the riding-bitt. Both have come lose throughout the centuries they should be lashed onto the anchor cable, securing it to prevent an anchor from dropping to ocean floor (dragging its cable behind) and getting lost should an anchor come lose in heavy weather or in battle.
This is a starboard side view through a lower deck gun-port, looking at the mainmast. The messenger can also be seen here, hung up onto the deck-beams.
This is how the messenger works. At "3" the messenger is passed several times around the capstan while at the bow (far right) it passes two rollers. When rotating the capstan the messenger follows the rotation, tight on the starboard side (bottom) and lose on the port (top). The anchor-cable can be seen being hauled in at "1". Just as it passes through the hawse-hole it is lashed sideways onto the messenger with "nippers" and is pulled inwards. once the first nipper reaches the cable-locker it is removed and lashed to the cable again at the hawse-hole, thus moving it from the last in line to the first. This is an endless process until the anchor is raised and stowed.
Here's one of my stoppers. The model would require two of these on the port- and five on the starboard- side.
Which stopper-knot the Dutch used in the seventeenth century is not known but it looks a great deal like the Mattew-Walker so I decided to use that one.
Here the anchor-cable is secured to the deck by a stopper. At least two of the were required for each cable, three for larger anchors.
This picture was taken last week, work on the messenger is progressing well. Contemporary sources call the wrappings "Mouses" - not mice! As all contemporary illustrations show the messenger made of two long cables I decided to do this too, so these two cables are lashed together with eye-splices.
A close-up view of a mouse
The process of splicing an eye
The finished and served eye-splice
Here two messenger eye-splices are lashed together.
And here the finished messenger ready for tarring
The following images show the messenger on my model hung up onto the deck-beams.
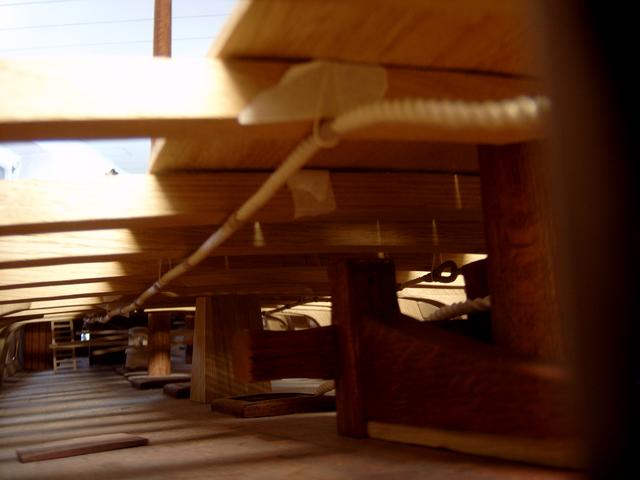
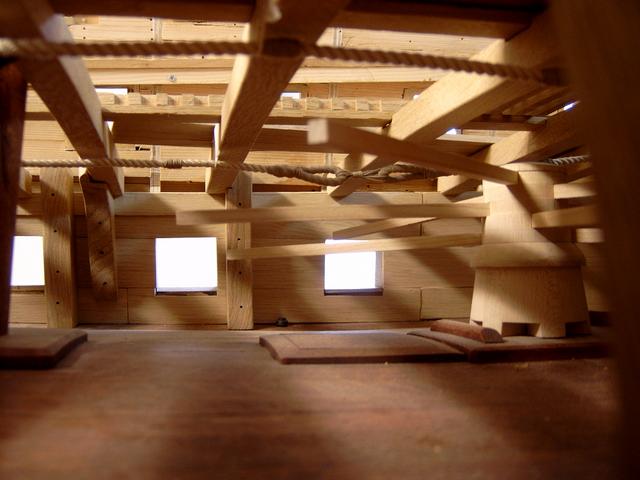
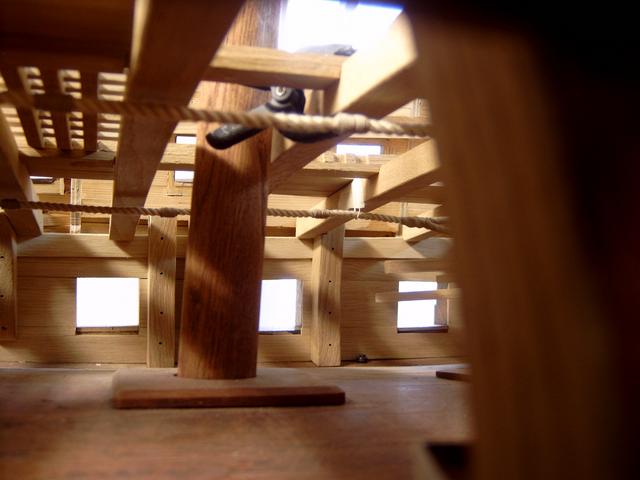
Peter