- Joined
- Mar 1, 2023
- Messages
- 107
- Points
- 213
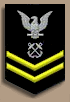
Fellow modellers
This is my diary of building La Salamandre 1752 using a kit purchased from CAF.
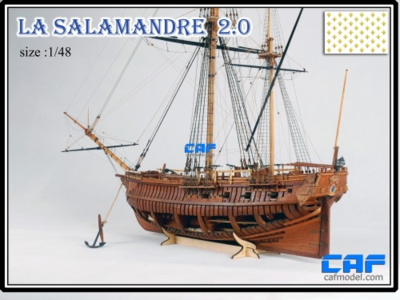
La Salamandre may not as popular as some other ships, but there are enough examples being built on forums so I am not completely by myself. I like the idea of a partially planked hull showing the frames and below decks, as well as the fact that she is rigged. There are some great examples being built from this kit - Koreets, Uwek, ADC, BigMike and Tedboat - and I will be happy if mine turns out half as well.
I don’t intend to do a review of the kit as this topic seems to be well covered by Uwek and others. I am pleased with the quality of the parts, but obviously assembling them is the challenge. The instructions are basic, but at least they provide a sequence for building. Hopefully, I can work out how each step should be undertaken to achieve the necessary results. Tom at CAF is a pleasure to deal with.
To help, I have a copy of the Boudroit and Berti monograph, as well as Frolich’s The Art of Ship Modelling which has a section devoted to this ship. I also have a small collection of other nautical books bought over the years, including Marquardt’s Eighteenth Century Rigs and Rigging, Harland’s Seamanship, as well as a number on traditional wooden boat building and rigging.
I am using a few basic hand tools. I don’t have any power tools, although I might change my tune when it comes to bolts and treenails. At present, my “workshop” is the end of the kitchen table.
I don’t expect this will be a quick build by any means, but I hope you will find it interesting.
Salty
This is my diary of building La Salamandre 1752 using a kit purchased from CAF.
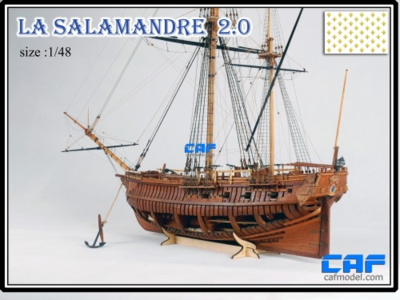
La Salamandre may not as popular as some other ships, but there are enough examples being built on forums so I am not completely by myself. I like the idea of a partially planked hull showing the frames and below decks, as well as the fact that she is rigged. There are some great examples being built from this kit - Koreets, Uwek, ADC, BigMike and Tedboat - and I will be happy if mine turns out half as well.
I don’t intend to do a review of the kit as this topic seems to be well covered by Uwek and others. I am pleased with the quality of the parts, but obviously assembling them is the challenge. The instructions are basic, but at least they provide a sequence for building. Hopefully, I can work out how each step should be undertaken to achieve the necessary results. Tom at CAF is a pleasure to deal with.
To help, I have a copy of the Boudroit and Berti monograph, as well as Frolich’s The Art of Ship Modelling which has a section devoted to this ship. I also have a small collection of other nautical books bought over the years, including Marquardt’s Eighteenth Century Rigs and Rigging, Harland’s Seamanship, as well as a number on traditional wooden boat building and rigging.
I am using a few basic hand tools. I don’t have any power tools, although I might change my tune when it comes to bolts and treenails. At present, my “workshop” is the end of the kitchen table.
I don’t expect this will be a quick build by any means, but I hope you will find it interesting.
Salty